Online oil analysis sensors can prove to be a contentious topic. Social media comments vary from fitting them everywhere to claiming that they will never be a substitute for laboratory oil analysis.
Of course, there is a middle ground where online sensors should be considered in their proper context.
The Case for Online Oil Sensors
In the last issue of Precision Lubrication, I wrote:
“The sampling frequency will determine the cost of the analysis process. The more frequently the sampling is required, the higher the cost through a commercial laboratory where the cost per sample will generally be the highest.”
Consequently, to offset this, cheaper costs per sample are required. This means looking at simple on-site tests, portable instruments, or even permanently mounted sensors on the assets.
One school of thought suggests that anything other than laboratory testing is inaccurate. A fair point, but consider that accuracy is not our goal.
Repeatability and Reproducibility
The repeatability and reproducibility of the test method are essential when evaluating oil analysis trends, irrespective of the accuracy. In addition, owing to the frequently encountered times I have seen poor sampling undertaken, it could be argued that laboratory testing is far less representative of the actual condition within the machine.
Consider particle counting, moisture testing, wear debris testing, and several factors such as the sample location, sampling method, the sample container, and the tools used, then the laboratory results are usually creating incorrect readings that are not representative.
This is based on my experience supporting portable instruments and online sensors and comparing them to laboratory results. It does mean that two sets of limits need to be applied respectively where online testing is in place compared to bottle sample testing.
However, I reiterate that the change in the trend is our first alarm condition.
This exposure to supporting an online particle trending device for a major filter manufacturer during the mid-1990s highlighted the benefits of online and inline testing.
To give some background, I was a technical support engineer for a then-new mesh blockage trending device, the Pall PCM100, launched in 1994. There were frequent calls from users complaining that the instrument gave far cleaner results than their laboratory reported for their bottle samples.
Inevitably the conclusion reached was that poor sampling practices were the cause. I would get the customer to take a bottle sample, and I would take a bottle sample, too, and based on the evidence under the microscope, my result was far cleaner and closer to the instrument.
That said, I was never going to match the instrument with a particle count from a bottle sample, either, since several factors would also come into play, namely:
- The instrument did not have to deal with extraneous and background contamination, which is the case with bottle sampling,
- The volume of fluid the instrument would sample is far more significant and, therefore, more representative than the laboratory particle counters sample, given the minimal amount they measure.
- More so than the volume of fluid sampled, the repeated testing and, thus, flushing of the lines would lead to increasingly cleaner results.
Apart from the mesh blockage particle trending device, I also saw this with light blockage particle counters that could be used online; on one occasion, I recall an ISO4406 result of 5/3/0 after repeated testing over an hour of a hydraulic fluid power system with good quality filtration in place.
Therefore, when I moved on from technical support to product management, and the opportunity arose to develop a new line of oil analysis sensors, I could see this might be the future for several reasons.
The first and foremost reason that appealed to me was the repeatability and reproducibility of the data, albeit with a lowering of the alarm limits needed owing to the cleaner data, especially for particle counting. That said, with the improved consistency of the data, any change in the trend would be more indicative of an actual issue rather than the change resulting from poor sampling practices.
Cost
The second reason was that the price point for such sensors would be such that more sensors could be fitted to the machine train where required allowing for a more holistic view of what was happening throughout the system. With bottle sampling, this tends to be limited to such points available for extracting a sample, leading to compromises.
That said, no one sensor can manage all aspects, so several sensors would likely be required to cover issues such as lubricant health, contaminant monitoring, and wear debris detection.
Even as far back as the late 1990s, technology meant that it was possible to conceive of these as capable of real-time monitoring on a network. Apart from the 24 hours a day monitoring, this would allow for remote monitoring of assets in unmanned situations; a classic example of this is wind turbines which have increased in parts of the world over the last two decades.
Safety
We should primarily encourage using these to reduce safety risks in traditional bottle sampling. In some cases, fluid pressures can exceed 350 bar with fluid power systems. More to the point, in several situations, risk assessments result in the machine needing to be shut down for sampling, and the delay before taking the sample can lead to unrepresentative results.
More Frequent Testing
Apart from safety, the amount of time spent sampling is significant, especially where machines are not set up for best practices in sampling. Therefore, automating the sampling processes reduces the effort allowing the focus to be put to better use.
Still, it also allows for far more frequent sampling than a team of personnel could achieve, which would not be justifiable in cost terms on those measures of labor rates.
Sustainability
Sustainability is a big thing, and rightly so. Imagine shipping 50 million 100mL samples and finding that 80% had no reportable fault. That’s 4 million liters of oil needlessly shipped annually. This figure was put forward twenty years ago for North America though I do not recall the source, so I cannot provide a reference.
Additionally, many oil analysis programs default to predictive rather than proactive, so consider the emissions generated by producing spares and undertaking equipment rebuilds. If we consider the online and inline sensors more than a protection system, small proactive steps can be taken to minimize machine wear and waste.
I hope I have presented a clear case for the advantages of sensors in general.
Online Oil Analysis Sensors Today
Sadly, over the last twenty years, the OEMs or end users have had no significant take up of these.
In the case of the end user, it is a matter of presuming that they’re an unnecessary expense since the OEM did not see fit to equip the asset with sensors. In addition, initially, it was the cost and complexity of adding such systems. Still, with the proliferation of wireless networks and, more importantly, a move to adopt Industry 4.0, one hopes this will change.
Another issue that has held back the situation is the lack of a comprehensive or holistic solution for sensors. Some manufacturers have focused on lubricant health, others on contaminant monitoring, and others on wear debris.
In addition, some manufacturers’ claims for their sensors, particularly in the field of wear debris monitoring in terms of size, have not been met, leading to the need for further and ongoing development of the technology.
Types of Online Oil Analysis Sensors
So, what types of oil analysis sensors are available? As mentione, most sensors focus on one aspect, which will be reviewed accordingly.
Lubricant Health Online Sensors
Lubricant health sensors are typically based on measuring the dielectric constant.
One of the leaders in this field is TANDELTA. Apart from online sensors, the technology is also packaged as portable instrumentation.
In its simplest form, it is more of a subject scale of change in the oil condition; however, research in the 1990s led to the ability to focus on several parameters. The typical values that this sensor can monitor include:
- Viscosity
- Acid/Base Number
- Oxidation
In addition, it can detect contaminants such as water, soot, and wear debris.
The sensor will work with most types of base oils on a range of machine types.
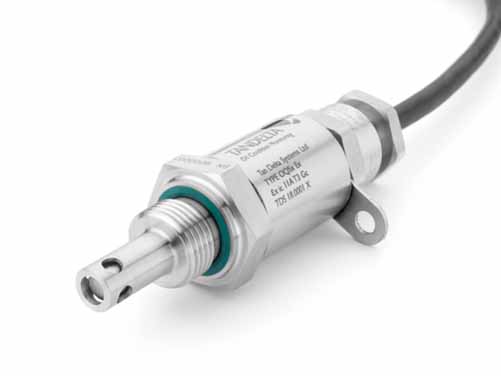
Reference: www.tandeltasystems.com – The ATEX rated sensor by TANDELTA.
However, for this technique to be effective, it needs to reference the new oil values to determine change, which is why these are best used inline as a permanent fitting rather than something portable and used to test a range of oils. Personal experience has shown that the sensors need thorough cleaning between oil samples in this portable fashion.
Oil Contaminant Monitoring Online Sensors
The next category of sensor is the contaminant monitoring type. The two most destructive contaminants are solid particles and moisture.
Starting with moisture, there are many techniques for measuring water in oil, which is usually presented as Parts Per Million (ppm) or percentage by volume.
The reference technique is usually Karl Fischer. In the 1990s, I was involved with developing capacitance sensors that report moisture as a percentage of the Relative Humidity of an oil.
While Pall Corporation did research converting this to a ppm reading, the saturation plot of an oil changes as it ages. These capacitance sensors need a shift in mindset to trend in %RH at a reported temperature, with the limit being 80% or lower, as this ensures that any moisture is dissolved in the oil.
The real benefit of these low-cost sensors is that they can be mounted immediately downstream of any potential ingress points on the machine, and even minor changes in the moisture levels will be rapidly detected.
These sensors are limited to mono-phase oils with minimal likelihood of reaching the saturation point and thus are ideal on hydraulic and turbine systems. These can also work well on gear oils where the ambient conditions permit, but should saturation be reached, the sensor will merely read 100% RH.
However, free and emulsified water should be more obvious visually. Used as a portable to dip between samples is not advised, as mentioned previously, owing to the risk of carry-over of high readings from a wet sample unless the sensor is dried thoroughly following saturation.
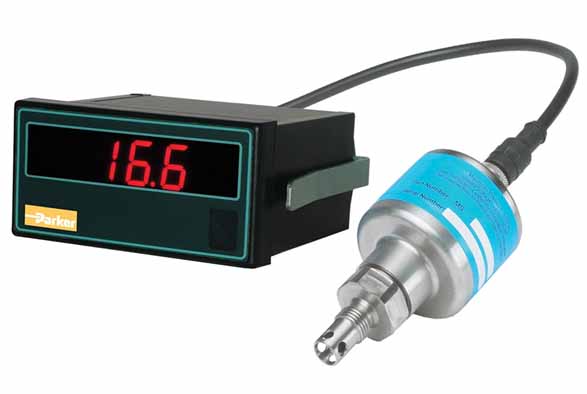
Reference: ph.parker.com – Parker Fluid Moisture Sensor
In the case of particle counting, this is a little more complex as most sensors sample a side stream of fluid rather than the main flow. While attempts have been made at a full flow inline sensor, this has had issues with turbulent flow on the light blockage type units.
Consequently, these sensors make the most sense on hydraulic and turbine machines where particle count is critical and the oil conditions (air, water, clarity) permit light blockage readings. Engine oils with soot, gear oils with water, and larger wear debris cause issues.
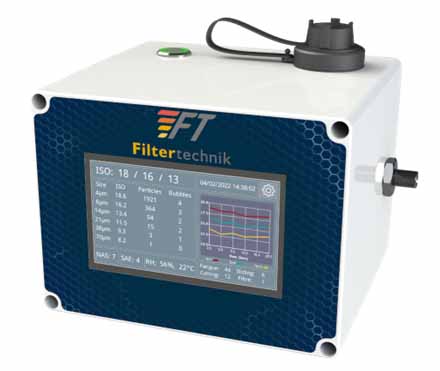
Reference: www.filtertechnik.co.uk – S120-PM Digital Imagining Particle Counter + Data-logging
Wear Debris Online Sensors
Moving onto wear debris sensors, these tend to utilize coil wound technology that detects Ferrous and non-Ferrous material passing through the coil. Ferrous material can be detected down to smaller sizes than non-Ferrous.
Still, OEM claims of 50µm for Ferrous have been questionable since getting that resolution requires smaller diameter passages through the coils. However, this is still a significant improvement over the 500µm chip detectors and the magnetic plugs.
Hall effect is another possibility, but again, that measures a subjective scale of the amount of Ferrous material. It could be argued that at 50µm, were the sensor capable of detecting debris of that size, the wear mode is now abnormal since, in normal wear, the debris is generally much smaller.
However, as already said, if the sensors are thought of as more than just a protection system such as chip detectors, then they at least provide earlier warning than would be the case with infrequent bottle sampling.
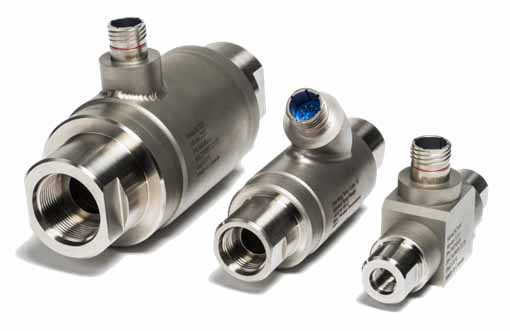
Reference: www.gastops.com – MetalSCAN Wear Debris sensor.
A more simplistic and Ferrous focused device utilizes magnets. These are more sophisticated than the simple magnetic plug as they can determine the amount and size of Ferrous debris trapped on the sensor probe.
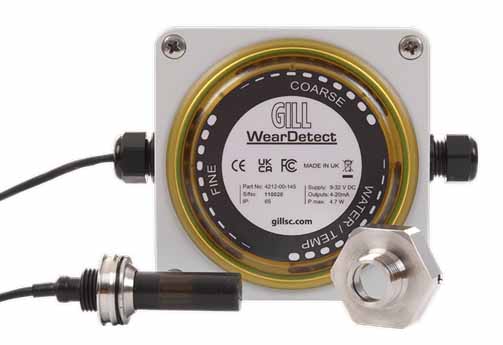
Reference: gillsc.com – The Gill WearDetect oil debris sensor.
Having reviewed what is capable, one can immediately discount the possibility of a “Lab-on-a-chip” sensor covering all tests. However, if one focuses on the critical parameters identified in a Failure Modes and Effects Criticality Analysis (FMECA), some sensors can cover these, such as moisture or lube condition.
Remember that even if the sensor can cover all tests, it should be complemented by a quality laboratory program.
The sensors are the traffic light that flags up the need for a sample should the sensor detect an issue.
In addition to routine laboratory testing alongside the sensors, the sensors should identify when something is amiss within the system.
As a result, if used correctly and within the limitations, the sampling frequency for laboratory testing can be reduced. When conditions change, a sample can be drawn immediately for urgent analysis.
However, the use of the sensors must be treated in a sensible manner that looks for changes in trends based on the more consistent readings from the sensors with less interference or noise caused by bottle sampling.