What is Oil Viscosity?
Oil viscosity is the internal friction within an oil that resists its flow. It measures the oil’s resistance to flow and is one of the most important factors in lubricants. Viscosity is also defined as the ratio of shear stress (pressure) to shear rate (flow rate).
Understanding Oil Viscosity
Imagine walking through a swimming pool filled with water. While walking through the pool, your body experiences some resistance from the water. Now imagine walking through the same swimming pool, filled with molasses this time!
It takes someone much longer to wade through a molasses-filled pool than one filled with water. In this case, the molasses is more viscous than the water. Thus, it has a higher viscosity than water.
You can also apply this to using a straw for drinking water from a glass. Pulling the liquid from the cup will be easy using a big straw. However, getting the same liquid to the person using the straw would take longer if a thinner straw were used.
Engine Oil Analogy
We can draw this analogy to car engines over the last 30-40 years. These engines had larger clearances for the oil to flow throughout the engine. As such, most of these engines used a 50-weight (or straight 50) oil.
As the technology evolved, the size of the engines got smaller. The clearances also got smaller, and the engine oil was now required to flow faster, control the transfer of heat and contaminants and keep the engine lubricated.
A straight 50 oil could not pass through the smaller straw at the speed it should. This would be equivalent to the user using a smaller straw for drinking molasses. It could take a while!
However, if a lighter weight (or less viscous) engine oil was used (such as a 0w20 or 10w30), then this is like someone trying to drink water (0w20) with a smaller straw.
It will flow much faster than molasses (straight 50) with the same straw! The lighter-weight oil would also transfer heat and flow much faster than the heavier-weight (more viscous) oil.
Factors That Affect Oil Viscosity
Similar to the molasses and water examples above, different factors can affect the viscosity of a liquid. For instance, water can assume other states depending on the temperature.
If water is at its freezing point (0°C), it can turn to ice but remains liquid at room temperature (around 20-30°C). Then, at 100°C, it can turn into a vapor. Its viscosity can change depending on the influencing factors.
Four factors affect oil viscosity:
- Temperature
- Pressure
- Shear rate
- Oil type, composition, and additives
Temperature
As seen with the example of the water above, when the temperature decreases, the water can turn to ice. Similarly, for lubricants, as the temperature drops, the viscosity increases. This means the oil will get thicker or more resistant to flow at lower temperatures. Likewise, as the oil heats up, it can become thinner.
This is similar to a block of ice melting as temperatures increase. Its viscosity will decrease, and the ice will turn to water. In this case, the internal molecules gain more energy with the increase in temperature, lowering the internal friction within the fluid. As such, the viscosity also decreases.
Since the oil’s viscosity will change with temperature, most OEMs will supply a temperature–viscosity chart for their equipment to help ensure the correct viscosity is used depending on the operating temperature.
In the figure below, gear oils of varying viscosities are plotted against the temperature for a particular piece of equipment. OEMs will typically specify the optimum operational viscosity range for their equipment.
It is then up to the lubrication engineers to determine the ideal viscosity based on the conditions of their equipment (this can vary depending on the application).
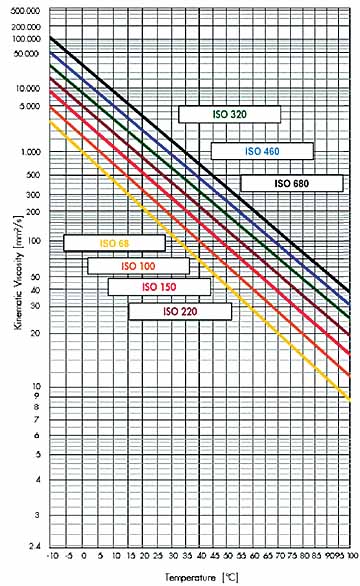
Figure 1: Temperature – Viscosity chart for Shell Omala S2 G (Source: Shell Lubricants TDS)
From the figure above, one can see that at 40°C, most of the gear oil grades correspond with their viscosities (ISO 68 corresponds with a 68 viscosity). However, at 0°C, an ISO 68 gear oil can become 1000 cSt, while at 90°C, this same grade of oil is around 11cSt.
Interestingly, all of the oils listed here can achieve a viscosity of 100cSt but at different temperatures, as shown below:
- 32°C – ISO 68
- 40°C – ISO 100
- 47°C – ISO 150
- 55°C – ISO 220
- 63°C – ISO 320
- 68°C – ISO 460
- 75°C – ISO 680
Temperature is a significant influencing factor of viscosity, but it is not the only factor.
Pressure
The effects of pressure on a lubricant’s viscosity are often overlooked. However, the viscosity-pressure behavior has become part of the calculation for elastohydrodynamic films. In these cases, oil viscosity can rapidly increase with pressure.
One such instance occurs with metal-forming lubricants, which are subjected to high pressures such that the oil’s viscosity can increase tenfold (Mang & Dresel, 2007). As the pressure increases, viscosity also increases, protecting the surface in these lubricant films.
The very definition of viscosity alludes to pressure’s impact on Newtonian and non-Newtonian fluids. For example, with Newtonian fluids (regular lubricating oils), the shear rate is proportional to the applied shear stress (pressure) at any given temperature.
As seen above, the viscosity can be determined once the temperature remains the same. However, Non-Newtonian fluids, such as greases, only flow once a shear stress exceeding the yield point is applied (Pirro, Webster, & Daschner, 2016).
Hence, this is why the observed viscosity of grease is called its apparent viscosity and should always be reported at a specific temperature and flow rate.
Shear Rate
For Newtonian fluids, viscosity does not vary with shear rate (Pirro, Webster, & Daschner, 2016). In fact, per the definition of viscosity for Newtonian fluids (regular lubricating oils), viscosity is a constant proportionality factor between the shear force and shear rate. Thus, even when subjected to greater shear forces, the viscosity will not change for Newtonian fluids.
On the other hand, for non-Newtonian fluids, the viscosity is influenced by the shear rate. Some non-Newtonian fluids can include; pseudoplastic fluids, dilatant fluids, and a Bingham solid, the effects of shear rate on these fluids are shown in the figure below.
A Bingham solid is a plastic solid such as grease that only flows above a particular yield stress. It can be seen that pseudoplastic fluids decrease viscosity with an increasing shear rate, while dilatant fluids show an increase in viscosity with an increasing shear rate. (Hamrock, Schmid, & Jacobson, 2004)
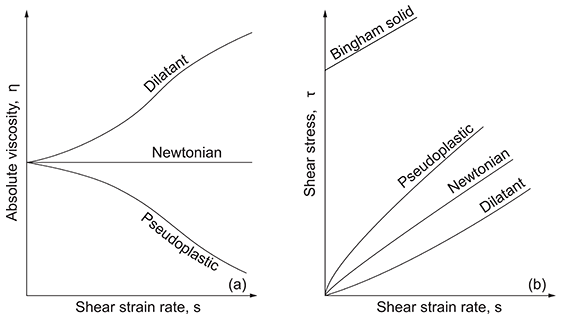
Figure 2: Characteristics of different fluids as a function of shear rate vs. viscosity (a) and shear rate vs. shear stress (b). Source: Fundamentals of Fluid Film Lubrication by Hamrock, Schmid & Jacobson, page 102.
The shear of a lubricant can influence its shear rate. Typically, longer-chain polymer viscosity index improvers can shear over time. When this happens, it can result in a decrease in oil viscosity. Similarly, non-Newtonian fluids, such as grease, experience a decrease in viscosity as a function of shear rate (Totten, 2006).
Another essential characteristic to note is whether a material is thixotropic or rheopectic. For a thixotropic material, if it is placed under a continuous mechanical load over a period of time, the viscosity will appear to decrease over this time.
However, the original viscosity is restored after a specific rest period, as shown in the figure below. On the other hand, for rheopectic materials, continuous shearing causes the viscosity to increase. (Mang & Dresel, 2007).
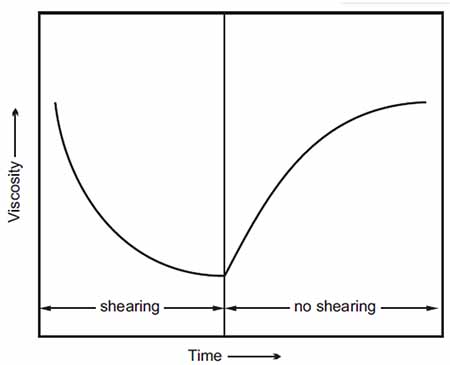
Figure 3: Flow characteristics of a thixotropic lubricant (Source: Lubricants and Lubrication edited by Theo Mang and Wilfried Dresel, page 30)
Oil Type, Composition, and Additives
Various oil types, compositions, and additives can influence a lubricant’s viscosity. For instance, the five groups of base oils all have varying characteristics, as shown in the figure below. One can note the differing viscosities for the various groups.
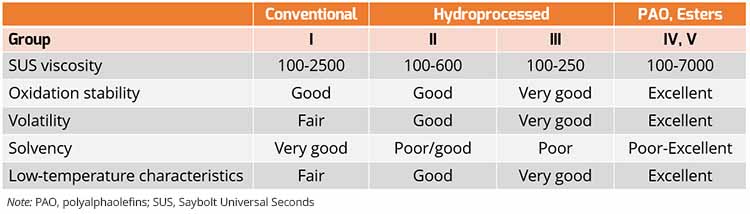
Figure 4: Base Stock property comparison (Source: Lubricants and Lubrication edited by Theo Mang and Wilfried Dresel, page 13)
When a finished lubricant is made, it usually consists of a base oil and additives. Hence, the base oil will have a significant role in determining the final viscosity of the oil. However, with the advent of Viscosity Index Improvers, desired viscosities can be engineered regardless of the base oil type being used.
Measuring Oil Viscosity
The viscosity of oil is one of its most essential characteristics. Thus, it is important to understand how this is measured and quantified. There are two main types of viscosity, dynamic (or absolute) and kinematic viscosity.
The dynamic viscosity measures the force required to overcome fluid friction in a film and is reported in centipoise (cP) or in SI units Pascal Seconds (Pa s) where 1 Pa s = 10 P (Poise). It can also be considered the internal friction of a fluid. This is usually used for calculating elastohydrodynamic lubrication related to rolling element bearings and gears.
On the other hand, the kinematic viscosity of a fluid is the relative flow of a fluid under the influence of gravity. Its unit of measure is centistokes (cSt) which in SI units is mm2/s, 1cSt = 1 mm2/s. (Mang & Dresel, 2007).
Kinematic Viscosity = Dynamic Viscosity / Density
Other units of measure for viscosity include; Saybolt, Redwood, and Engler, but these are less widely used than the cSt or cP, especially for lubricants.
Oil Viscosity Grades and Standards
One of the best-kept secrets about viscosity is that a particular grade often represents a range. When oils are classified, one may see an ISO 32 or ISO 220 and believe that the oil will have this exact viscosity (32 cSt or 220 cSt). However, this is not the case.
There are three general classifications where viscosity grades have particular ranges based on the fluid type. The fluid may behave differently in each application, hence the need for these three scales. However, there is a chart that allows users to convert the various scales into the one needed.
Engine Oil Classification (SAE J300)
As per the Society of Automotive Engineers (SAE), the SAE J300 standard classifies oils for use in automotive engines by viscosities determined at low shear rates and high temperature (100°C), high shear rate and high temperature (150°C) and both low and high shear rates at low temperature (-5°C to -40°C) (Pirro, Webster, & Daschner, 2016).
Engine manufacturers have widely used this system to aid in designing lubricants suited for these applications. As such, oil formulators also adhere to these classifications when engineering lubricants.
One will note the use of the suffix letter “W” in some of the grades below. These oils are intended for low ambient conditions, whereas those without the “W” are intended for oils that will not encounter low ambient conditions.
These are commonly described as multigrade (where the “W” is found between two numbers) and monograde oils (where the “W” is at the end or the grade is identified by a number only) in the table below.
The table shows that the viscosities must fall within a particular range to be classified. For instance, a 5W30 oil should meet the specifications of:
- Low temperature, Cranking viscosity of 6600 cP at -30°C
- Low temperature, Pumping Viscosity Max with No Yield Stress of 60,000 cP at -35°C
- Low shear rate Kinematic viscosity at 100°C should be between 9.3 -12.5 cSt
- High Shear rate viscosity at 150°C Max at 2.9 cP
One will notice the range of 9.3 to 12.5 cSt (at 100°C). This is where oils can be blended to either end of this scale but still achieve the classification of a 5w30 oil.
Axle and Manual Transmission Lubricant Viscosity Classification (SAE J306)
As per the SAE recommended practice J306, automotive manual transmissions and drive axles are classified by viscosity, measured at 100°C (212°F), and by the maximum temperature at which they reach the viscosity of 150,000 cP (150 Pa s) when cooled and measured in accordance to ASTM D2983 (Method of Test for Apparent Viscosity at Low Temperature Using Brookfield Viscometer). (Pirro, Webster, & Daschner, 2016).
The table below shows that for an SAE grade of 190, the kinematic viscosity must fall within the range of 13.5 to 18.5 cSt at 100°C. While most viscosities tend to fall mid-range of these values, it also indicates that if the lubricant achieves 18 cSt at 100°C, it can still be classified at an SAE grade 90.
The most common multigrade lubricants within this grade fall within the 80w90 or 75w140 classifications.
Another factor for these types of lubricants is API GL4 or GL5 ratings. It must be noted that a GL5 lubricant is recommended for hypoid gears operating under high-speed, high-load conditions.
On the other hand, a GL4 lubricant is usually recommended for the helical and spur gears in manual transmissions and transaxles operating under moderate speeds or loads. These should not be used interchangeably as the GL5 lubricants tend to adhere to the surfaces and may cause more damage in a GL4 application.
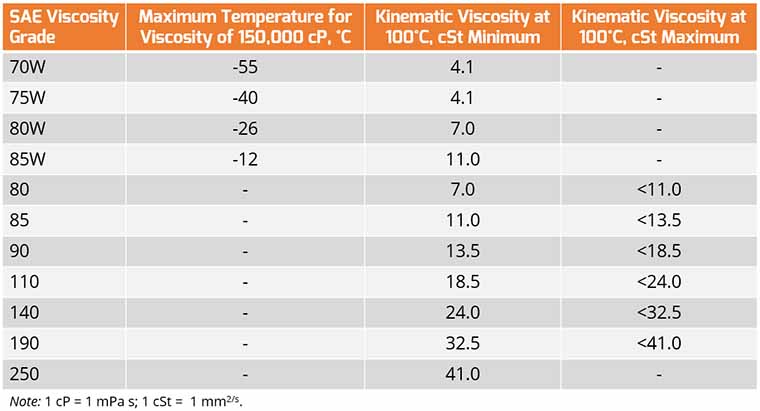
Figure 5: Automotive Gear Lubricant Viscosity Classification. Source: Lubrication Fundamentals, Third Edition Revised and Expanded by Pirro D. M., Webster M., and Daschner E. pg 52
Viscosity System for Industrial Fluid Lubricants
This classification was jointly developed by the ASTM and STLE (Society for Tribologists and Lubrication Engineers). Initially, the system was based on viscosities measured at 100°F but converted to viscosities measured at 40°C.
ASTM D2422 and ISO 3448 are the references for this system. In this system, it is clearer to see the variances in the ranges of viscosities. In this case, the mid-point of the range is used as the ISO viscosity. To determine the range of any ISO viscosity, one can calculate ±10% of the mid-point value to get the minimum and maximum values of the range.
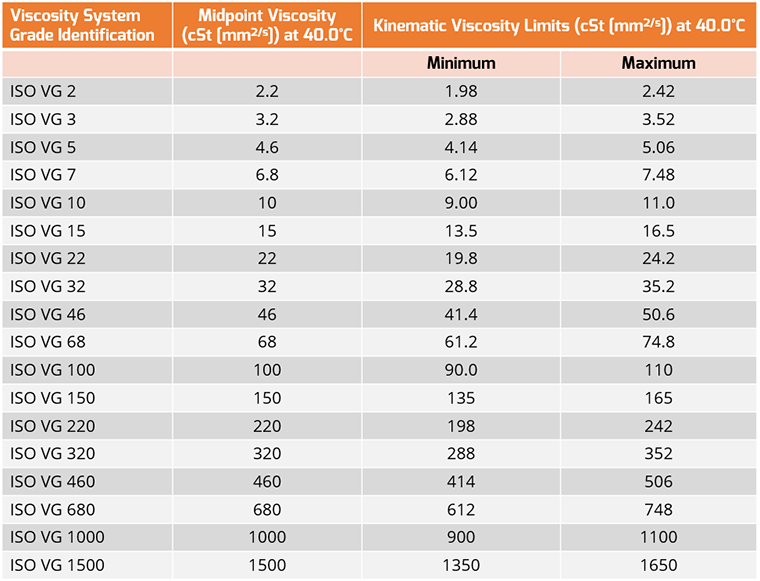
Figure 6: Viscosity System for Industrial Fluid Lubricants. Source: Lubrication Fundamentals, Third Edition Revised and Expanded by Pirro D. M., Webster M., and Daschner E. pg 52
All of these systems can be represented in the figure below, where it is easy to calculate the oil viscosity using another system:
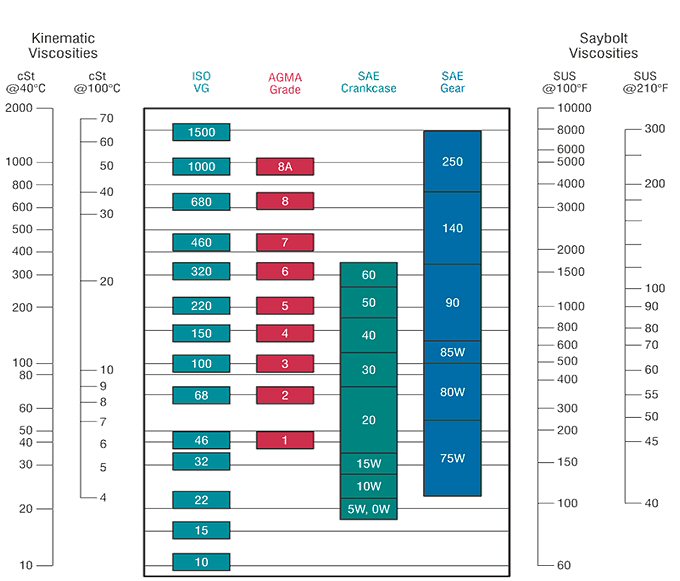
Figure 7: Various viscosity systems in one chart.
Future Developments and Research in Oil Viscosity
As explained at the beginning of this article, the changes in technology (such as smaller engines) will demand more from lubricants, especially in viscosity. Thirty years ago, a 0w16 engine oil was unfathomable, but today, it is being integrated into our newer model vehicles.
Some of the concepts which will continue in the future can include:
- Reducing viscosity – as seen in the examples above, with most pieces of equipment getting smaller, the need for lighter weight (lower viscosity) oils will continue as OEMs constantly evolve and push the boundaries of their equipment.
- Measuring viscosity – traditionally, viscometers have always been used where the difference in the height of the liquid at particular temperatures (or under certain conditions) is measured. Given the advancements in technology, this may be subject to change very shortly into a more reliable and even more accurate method.
- Viscosity-dependent parameters – temperature and pressure have the most significant impacts on the oil’s viscosity. However, some of these challenges can be overcome with the advent of viscosity index improvers. With enhancements in the formulation of viscosity index improvers, one can expect oils of varying viscosities to be used in parameters they could not have used in the past.
- Alternative oils – more sustainable options are constantly being explored. Whether this lies in using plant-based oils or other alternative bio-based oils, these may introduce new ways or conditions under which different viscosities can exist.
Overall, viscosity is one of the most important characteristics of a lubricant. It can easily influence the impact of the oil on the internal surfaces of the equipment and its overall energy efficiency.
It is important to remember that oil viscosity should be determined by the application in which it is being used. Parameters such as temperature, pressure, and shear rate should all be considered when selecting the lubricant’s viscosity.
References
Hamrock, B. J., Schmid, S. R., & Jacobson, B. O. (2004). Fundamentals of Fluid Film Lubrication, Second Edition. New York: Marcel Dekker, Inc.
Mang, T., & Dresel, W. (2007). Lubricants and Lubrication. Weinheim: Wiley-VCH.
Pirro, D. M., Webster, M., & Daschner, E. (2016). Lubrication Fundamentals, Third Edition Revised and Expanded. Boca Raton: CRC Press, Taylor & Francis.
Totten, G. E. (2006). Handbook of Lubrication and Tribology, Volume I Application and Maintenance, Second Edition. Boca Raton: CRC Press, Taylor & Francis.