Oil analysis on oil reservoirs, such as a paper machine, provides much more value than most maintenance managers realize.
Regular reservoir oil sampling can provide the following:
- Reactive information, such as a spike in wear metals identifying a failed bearing or another component.
- Predictive information, such as a slight increase in wear metals indicating early stages of an impending failure.
- Or, most valuable of all, it can provide proactive information. Oil analysis can tell you when your additives are getting depleted, contamination levels are getting to a point where additional filtering may be needed, moisture levels are to the point where corrective measures are required to prevent damage, and with enough data, may even tell you if your equipment is operating outside of its intended design (too hot, too slow, cavitation).
It’s all about using facts and data to help us make better maintenance decisions and get the most out of our investments. Improving the life expectancy of equipment, extending the life of oil life, and reducing unplanned downtime (which also improves safety) are just a few reasons the value of oil analysis far outweighs the cost.
So, would continuously monitoring the oil add more value if oil analysis provides that much value? We recently decided to add a continuous oil monitoring system to the main lube on our paper machine lubricating system.
We then took that information and sent it to our historian to be trended 24/7. We are trending the oil temperature, the moisture level, and the ISO 4/6/14 particle counts.
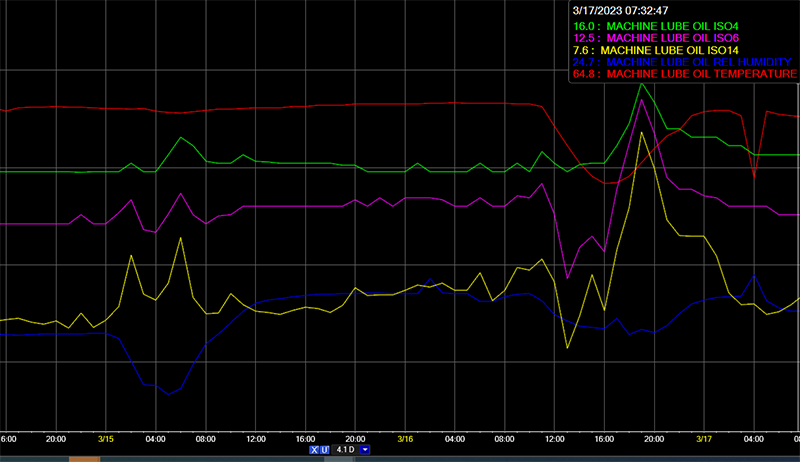
Particle Count, Relative Humidity and Temperature Trending
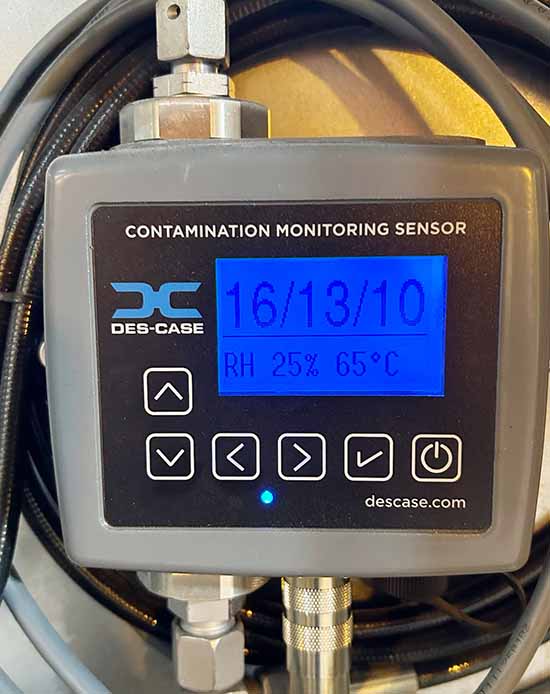
Contamination Monitoring Sensor
When we started this project, we did not realize how fast it would pay for itself! Shortly after getting the system online (but before trending), the maintenance manager notified us that the paper machine dryer head had developed a steam leak.
We watched the oil condition and saw no change. A few days later, the moisture levels began to climb rapidly. Thanks to the monitoring system, we reacted to this issue by periodically draining some oil and hooking up a vacuum dehydrator.
Within 24 hours, we reduced the moisture to an acceptable level and returned to normal within 72 hours. No doubt, this quick response minimized the amount of damage the water in our system caused.
Nicholas Knott, a colleague at another paper mill, had the same experience while trending moisture levels in his paper machine. He also caught it quickly and believes this technology prevented many bearing failures. Below is the trend showing how quickly the moisture reaches unacceptable levels and how fast his team could resolve it.
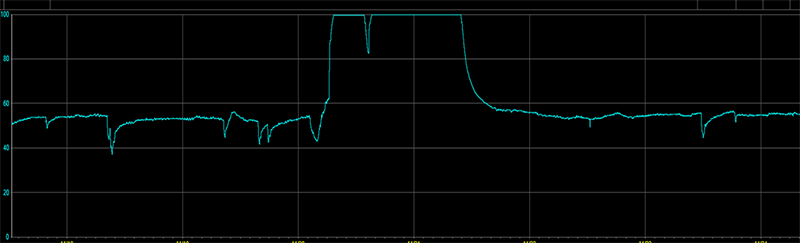
Moisture-in-Oil Trend
The lesson from these unfortunate situations is that if we were not doing continuous monitoring, how much damage would’ve occurred? We will never know, but we know that steam leaks on a dryer head were common in the past, and oil analysis was rare.
We also know that we had to replace many bearings in the past, which is rare now. Using continuous oil monitoring systems may only be necessary for some situations. Still, in a challenging application like a paper machine, it adds way more value than it costs.
Soon we expect to have enough data to understand if situations like start-ups, shutdowns, wash-ups, and machine speeds have impacted our oil quality.