What is Lubrication?
Lubrication is the process of reducing friction, wear, and heat between moving surfaces by introducing a lubricating substance, such as oil or grease.
The Purpose of Lubrication
If you walk into any industrial facility, you will find lubricants. While they come in all types of textures (greases or oils), viscosities, and packaging, one thing remains true: We need them. Lubricants were designed to reduce friction as their main function. However, that’s not their only use.
Although lubricants can effectively reduce friction, they can also reduce or transfer the heat built up in machines.
Although lubricants can effectively reduce friction, they can also reduce or transfer the heat built up in machines. This only applies to oils circulated through the systems and not grease that remains in place.
Additionally, lubricants can minimize wear by providing an adequate film to separate surfaces from rubbing on each other.
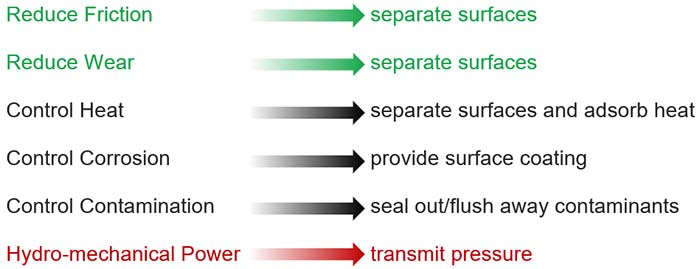
The 6 Functions of a Lubricant
Lubricants also help improve the efficiency of the machine by removing heat and reducing friction. They can also remove contaminants (for oils that are circulating, not grease) and transport them away from the machine’s internals. This is due to some additive technologies (such as dispersants or detergents).
Depending on the type of lubricant or its application, its function can also change. For instance, hydraulic oils are specifically used to transmit power, something that gear oils or motor oils cannot do. On the other hand, the lubricant can be considered a conduit of information if condition monitoring is considered.
Lubricants provide several functions depending on their application and environment. However, the main functions of a lubricant include reducing friction and wear, distributing heat, removing contaminants, and improving efficiency.
How Lubrication Reduces Friction and Wear
At the heart of lubrication is the main function of overcoming friction. When two parts move or two surfaces rub against each other, microscopic projections called asperities exist. Even on what appears to be smooth surfaces, asperities exist, and when these move over each other, friction is produced, which in turn can generate heat and cause wear.
Wear can typically occur in various forms, but in many of these, the touching of the asperities serves as the trigger point for wear to occur.
This is where lubricants really make a statement. They serve to provide a barrier between the two surfaces, almost allowing them to float over each other seamlessly. As such, friction is reduced once the asperities are kept apart, and this even influences a reduction in the occurrence of wear.
Wear can typically occur in various forms, but in many of these, the touching of the asperities serves as the trigger point for wear to occur. With the presence of the appropriate viscosity of lubricants, these asperities can be kept apart, and the occurrence of wear can be diminished significantly.
The Role of Lubrication in Preventive Maintenance
As we have noted above, proper lubrication can help to prevent wear. This is one of the many characteristics which make it ideally suited as a tool for preventive maintenance.
As defined, preventive maintenance can help maintenance professionals schedule time-based tasks / prescribed intervals1. Any maintenance manual will include prescribed intervals at which lubricants should be changed (typically after 500 hours or 5000km).
OEMs (Original Equipment Manufacturers) defined these intervals as general guidelines for machine operators. This gives operators an idea of the lubricant’s expected life or the duration after which it would no longer be able to perform its functions adequately. By changing the lubricants at these intervals, one could avoid unplanned downtime.
Another aspect of lubrication associated with preventive maintenance is relubrication intervals. In some machines, there are minimum required reservoir levels that need to be maintained.
However, depending on the system, there may be some expected loss of lubricants during its lifetime. As such, relubrication intervals can help prevent unwanted downtime by injecting new oil or grease (with fresh additives) and maintaining the required reservoir levels.
Types of Lubricants and Their Applications
Not all lubricants are created equally! In fact, they need to be designed differently for the various applications in which they are to be used. Typically, the overarching classification of lubricants can fall under either oil or grease. However, there are further categorizations that also include solid lubricants and specialty lubricants, as there are many varying applications of lubricants.
Oil Lubricants: Characteristics and Uses
Most of us are very familiar with oils. They are liquid; we use them in our cars or trucks, but what are they? An oil is comprised of base oil and additives. The additives can be used to either enhance, suppress, or add new characteristics to the base oils2.
Typically, oils can be used in many different applications and provide the advantages of having various viscosities according to the application3. These can range from oils with a viscosity similar to that of water to oils as thick as tar.
One of the main advantages of using oils as lubricants is their ability to dissipate heat from the system. Since they are fluid and circulate, they can “move” heat away from specific components and even help to remove some contaminants.
Oils can be used in gasoline-engine passenger cars, diesel-engine applications, circulating systems, turbines, gear applications, hydraulics, compressors, or even natural gas engines. Each application represents a different ratio of additives to base oils, ranging from 30% (motor oils) to a mere 1% additive (turbine oils).
Grease Lubricants: Advantages and Limitations
While the industry is familiar with oils as lubricants, there are some places where grease works better than oils! Greases are oils to which a thickener has been added. As such, they comprise base oil, additives, and thickener. The thickener holds the oil in place, allowing it to perform its main functions of reducing friction and providing lubrication.
One of the main advantages of greases is their ability to stay in one place. Consider a bearing placed at a 90° or 180° angle. If oil were used to lubricate this, it would drain out very easily. However, grease stays in place and still ensures that lubrication occurs.
While staying in place is a major advantage of grease, there are also some disadvantages to using it. A couple of those include the fact that grease cannot transfer heat away from components and keeps contaminants in place. These can both negatively impact the equipment.
Similar to oil, grease has different viscosities as per the NLGI (National Lubricating Grease Institute). These range from a 000 (almost the consistency of oil) to a 6 (similar to that of a block) and are all made for varying applications, as shown in the figure below.
While these viscosities define the application, one must also remember that the base oil viscosity can also differ. As such, operators must be mindful of NLGI grade, base oil viscosity, and additive package when selecting an appropriate grease.
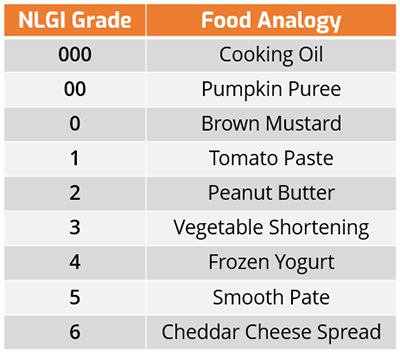
NLGI grades of grease
Solid Lubricants: When and Why to Use Them
Why do we need a solid lubricant if we already have oils and greases in different states? Particular applications make these lubricants mandatory as they are the only ones that can meet the conditions and specifications involved.
Unlike oils or greases, these solid lubricants are designed to work in one lubrication regime, boundary lubrication4 (more on this later in the article). What sets these lubricants apart is their ability to form very thin films on the surfaces of moving components, which reduces friction due to their very low shear strength.
Some examples of solid lubricants include graphite, Molybdenum Disulfide (MoS2), Boren Nitride, and Fluoropolymer (PTFE). These solid lubricants can usually be used as grease additives (such as MoS2 for greases in mining with high load, low-speed applications) or even in the space industry for dry lubricant coatings on spacecraft.
Lubrication Regimes: Understanding the Science of Lubrication
The primary purpose of lubrication is to create an acceptable lubricant film to sufficiently keep the two moving surfaces apart while allowing them to move with reduced friction. This is the ideal condition, but a lubricant can undergo a couple of different regimes before it achieves this full film format.
The figure below shows the overall relationship between film thickness and the related regime and the associated regime relationships with the coefficient of friction.
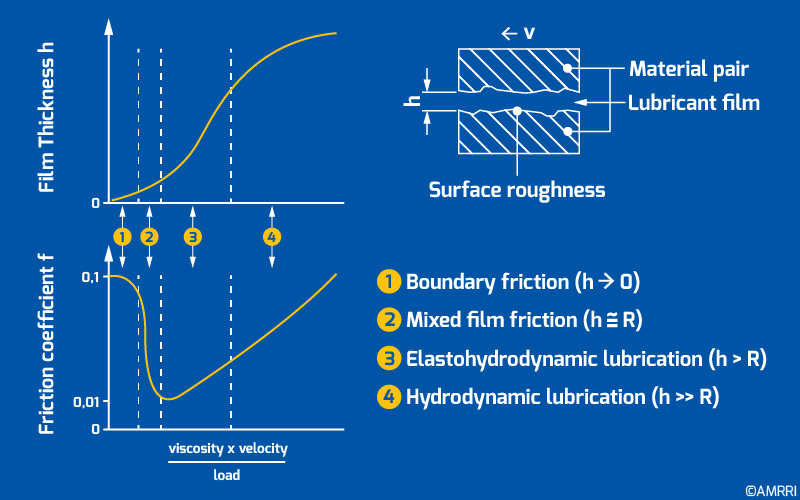
Stribeck curve showing the friction levels associated with the various lubrication regimes from Lubricants and Lubrication, Second, Completely Revised and Extended Edition edited by Theo Mang and Wilfried Dresel (2007)
Boundary Lubrication
At startup or rest, lubricants are usually residing in the sump. For this example, let us think about a car at rest. Since the vehicle has not moved, all the oil should have been drained and settled in its sump at the bottom of the engine. When the car starts, all the parts on the inside will begin moving.
Only after it starts does the oil begin its swift journey from the bottom of the sump to all the moving parts. That means that there is a delay between the oil getting to perform its function or reaching the moving parts.
In boundary lubrication, the oil has not fully formed its film, and there isn’t adequate separation of the asperities.
During boundary lubrication, the oil has not fully formed its film, and there isn’t adequate separation of the asperities. In this state, wear can still occur, and it is in this state that most wear occurs. A similar situation occurs during equipment shutdown, where the components also experience this boundary state of lubrication.
The figure below shows the various film conditions. In boundary lubrication (c), the asperities touch, whereas they are fully separated in (a).
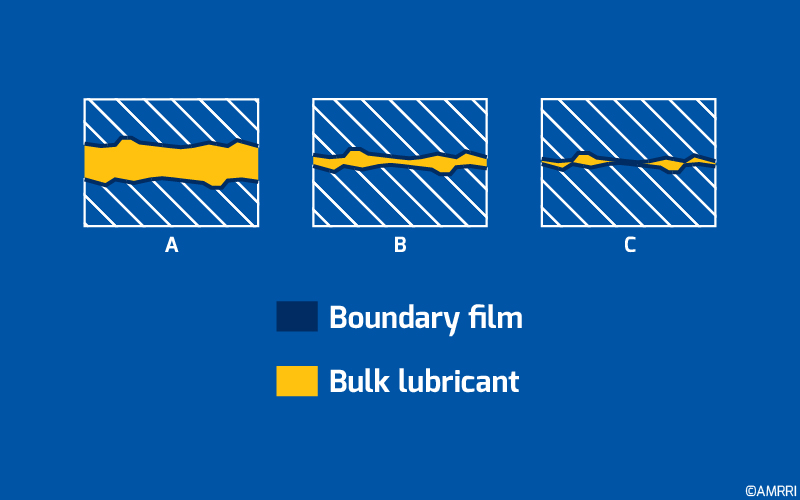
Different regimes as it relates to the lubricant
Surface-active additives are critical for boundary lubrication and become activated under certain conditions. One of the most popular additives is EP (Extreme pressure) additives, which become activated when temperatures are increased (usually as a result of increased friction).
A surface film is typically formed during boundary lubrication. This can be the result of physical adsorption (physisorption), Chemical adsorption, or Chemical reactions involving or not involving stearate.
Physical adsorption occurs under mild sliding conditions with light loads and low temperatures. Chemical adsorption (chemisorption), stronger than physisorption, occurs when fatty acids react with metals to form soaps, which may or may not be attached to the surface.
On the other hand, chemical reactions that do not involve a substrate allow for slightly stronger bonds than chemisorption. However, with phosphorus-containing compounds, the phosphorus exists in a soluble carrier molecule that degrades at elevated temperatures, plates out on the metal surfaces, and forms a phosphorus soap (typically found in the Antiwear additive packages).
The last and strongest bonds to protect the surface are the chemical reactions involving a substrate where sulfide layers are formed on the surface. These provide low friction and good adhesive wear resistance5.
Mixed Lubrication
This state of lubrication exists as the lubricant transitions between Boundary and Full-Film lubrication. Its average film thickness is less than 1 but greater than 0.01μm. Some exposed asperities and roller element bearings can still experience this state during their start-stop cycles or if they are experiencing excessive or shock loads. These thin films are exposed to high shear conditions, leading to increased temperatures and reducing the lubricants’ viscosity6.
During this state, antiwear and EP additives protect the surfaces (similar to boundary lubrication). Most lubricants transition through this phase, and the additive packages must be able to help protect the surfaces.
Hydrodynamic Lubrication
During this regime, the two surfaces are usually fully separated. They are thick hydrodynamic fluid films that tend to be more than 0.001 inches (25μm) in depth, experiencing pressures between 50-300psi7. Ideally, friction only results from the shearing forces of a viscous lubricant8.
In this state, the surfaces are conformal, meaning that the angles between the intersecting surfaces remain unchanged. It is important to remember this, as it differentiates the hydrodynamic regime from the elastohydrodynamic regime. As shown in the figure below, the coefficient of friction changes for the various regimes, with the hydrodynamic regime having the lowest value.
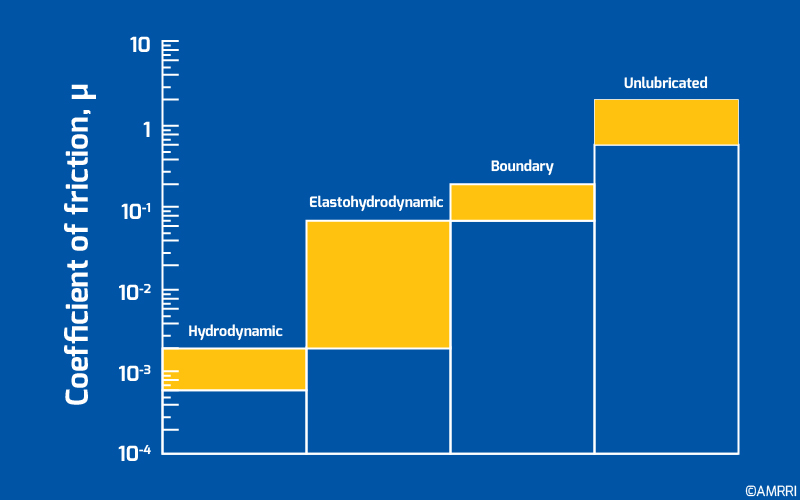
Coefficient of Friction for the various regimes
Elastohydrodynamic Lubrication (EHL)
One of the main defining factors with EHL is that the oil’s viscosity must increase as the pressure on the oil increases, such that a supporting film must be established at the very high-pressure contact areas. Due to the pressure of the lubricant, elastic deformation of the two surfaces in contact will occur. These films are thin, typically around 10-50 μinches (0.25 – 1.25μm).
The surfaces in EHL are non-conformal (unlike Hydrodynamic lubrication), and the asperities of the contacting surfaces do not touch. However, the high pressures can deform either of the contacting surfaces to ensure that a full fluid film is maintained. This can increase the coefficient of friction.
Common Lubrication Mistakes and How to Avoid Them
Mistakes can happen all the time, but when we repeat them, they can become a habit or, worse, be viewed as a “best practice” within our industry. In the lubrication realm, there are a few common mistakes that occur quite frequently. In some cases, the operators may not understand or be aware of the full gravity of these mistakes. In this section, we will explore ways to avoid these mistakes.
Over-Lubrication vs. Under-Lubrication
“Some grease is better than no grease” is a common saying in the industry. However, there is such a thing as over-lubrication! Think about swimming pools. The pool usually has different levels: a minimum fill level, then a mid-tier level, and finally, the maximum level.
If we don’t fill it to the minimum level, it’s basically a puddle of water, not a swimming pool. We need a certain volume of water to function as a swimming pool. The same applies to our equipment.
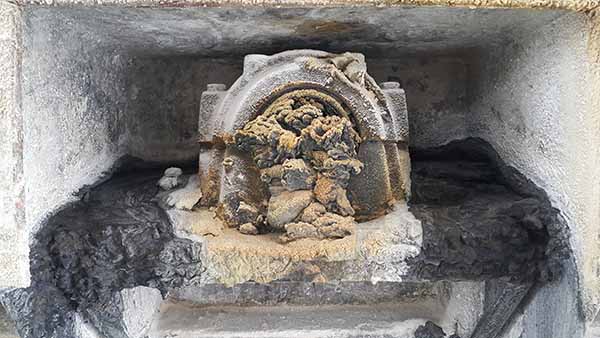
Over-lubrication of a bearing
We will under-lubricate our equipment if we do not provide enough grease or oil. In these cases, there is not enough lubricant to form the full required film to keep the two moving surfaces apart and perform all the lubricant functions. Therefore, there will be increased friction, wear, and heat, all leading to system inefficiencies.
On the other hand, if we filled the swimming pool beyond the maximum level, it would be pretty tricky for us to stand in it (while touching the bottom) or walk across the length of the pool without having lots of opposition from the water compared to walking across the length of the pool when it’s filled mid-way.
Something similar is happening with our equipment. If we over-lubricate it, we place additional stress on the components to perform extra work, as they must move on a thicker layer of lubricant, which will cause frictional losses. This can cause the equipment to heat up, leading to degradation of the lubricant and loss of efficiency.
Both over-lubrication and under-lubrication can be detrimental to your equipment. Instead, use the optimal level of lubricant, or (in the case of greases) use ultrasound to determine the required amount of grease for your application. In both cases, the ideal amount of lubricant is the volume at which the coefficient of friction is significantly lowered.
Choosing the Wrong Lubricant for the Application
Quite often, the wrong lubricant is chosen for the application. This can happen in several ways, whether unintentional or an error passed down through shift changes. Selecting the correct lubricant for your application begins with knowing the environmental and operational conditions and the equipment specifications.
Your first guide/resource should be the equipment’s OEM. They designed the equipment to perform within specific tolerance limits and can advise on the most appropriate lubricant given these tolerances. If they cannot be contacted, an alternative would be contacting your lubricant supplier to help determine the best lubricant based on their expertise with similar types of equipment in varying conditions.
Selecting the correct lubricant for your application begins with knowing the environmental and operational conditions and the equipment specifications.
Another misconception about selecting lubricants is that they should be chosen based on their initial cost. Instead, the total lifecycle cost of the lubricant should be considered, and the properties of the lubricant should also be factored into the decision-making process. The initial cost of the lubricant pales compared to the cost associated with unplanned downtimes, the short life span of the lubricant, and its disposal.
Inadequate Lubricant Storage and Handling
Lubricants should be handled with care. They can be affected by temperature, light, water, particulate, or even atmospheric contamination. They must be stored properly in a dry, clean, cool space (not exposed to the elements).
When transferring lubricants from larger containers into smaller ones, think of how you would perform this operation if you transferred blood from the blood bank to one of your family members. Would you use any container you found on the ground, or would you ensure that it is a sterilized container (needle or equipment)?
Lubricants can easily become contaminated with particulates, which can then be transferred to machines, leading to unplanned shutdowns. When transferring lubricants, it is critical to ensure that we do not introduce contaminants or transfer these contaminants to our equipment. We must keep the lubricants clean and free from contaminants.
Ignoring Environmental and Operational Conditions
Not all lubricants are created equally. Some are designed for harsher environments, while others can only function in regular operating conditions. Mineral oils can typically work in many circumstances. However, when higher temperatures or loads are involved, this may be a job more suited for a synthetic lubricant.
On the other hand, if the lubricants are geographically close to waterways or come into contact with them in any way, then these should be environmentally acceptable lubricants (EALs). Depending on the load and temperatures experienced by your equipment, your lubricant provider or OEM for the machinery can advise on the best-suited lubricant that will perform in these conditions.
Lubrication Maintenance Best Practices
We’ve already covered some mistakes; it’s time to look forward to some lubrication best practices. To some of us, these may seem trivial, but they can lead to big impacts on your overall maintenance budget and can even manage to decrease some unplanned downtime.
Creating a Lubrication Maintenance Schedule
Every component in your industrial facility needs to be lubricated. The frequency at which this occurs, alongside the type of lubricant, can vary greatly. However, by properly mapping out your lubrication points and frequency intervals, you can develop a lubrication maintenance schedule that your planner will be proud of!
The first task on your list would be to have a detailed listing of all your assets, their locations, the type of lubricant being used, and suggested relubrication frequency. Next, this can be consolidated into daily, weekly, monthly, and quarterly tasks.
Afterward, you must bring your mapping skills into place as you incorporate the lubrication tasks with other maintenance tasks in the same area. This way, your assigned personnel maximize their time in one geographical location.
Importance of Lubricant Analysis and Condition Monitoring
How often do you perform blood work for yourself or visit your doctor? Performing blood work is similar to taking an oil sample for our equipment as we investigate what’s happening inside it. This can give us a heads-up on an impending failure (if there is a high wear metal concentration or the presence of contaminants) or an issue in the oil (changes in viscosity or additive packages).
By effectively monitoring the health of your oil, you can prevent unplanned shutdowns or even extend its life. This can save your company from significant losses and increase your production output.
Lubrication Training for Maintenance Teams
Quite often in our industry, we hear, “Oil is oil, or grease is grease,” but after reading this article, I’m sure you will agree that those words are a very big misrepresentation. This is why training is so important for our teams. We want to ensure we all understand why we’re not leaving the oil drums out in the rain and pouring them into our equipment!
This will lead to water getting into the oil drums. Then, we include the water in our equipment alongside our oil, which will change the oil’s viscosity, possibly leech out some of the additives being used for protection, and can act as a catalyst for further, rapid degradation of the oil.
This simple storage and handling concept can cost our company unplanned downtime and loss to production, but by adequately training our teams to understand lubrication and some of the best practices, we can transform our facilities into world-class lubrication sites. The only way to do this is as a team working together to achieve a goal that we all understand.
Frequently Asked Questions About Lubrication
How Often Should Equipment Be Lubricated?
This can change depending on your environment and operating conditions. A machine operating in a clean environment with ambient temperatures and a typical load should be lubricated according to its schedule. However, if this same machine is in a dusty, high-temperature environment working 24/7, its change or relubrication intervals will be shorter than the regular ones.
Lubrication reduces friction in your system. Hence, you can detect when friction levels increase if you’re monitoring your assets using ultrasound. This would allow you to apply a small volume of lubricant to lower these levels. (This is specifically for greases.)
You are always advised to check with your OEM, who will have recommended lubrication schedules for your equipment in varying environments and operating conditions.
What Are the Signs of Poor Lubrication?
Poor lubrication can mean under- or over-lubricated assets or incorrect use of a lubricant in a particular application. If your lubricant is not meeting the expected intervals and the components constantly fail due to lubrication issues, these are some telltale signs of poor lubrication.
How Do I Know If I’m Using the Right Lubricant?
All lubricants are required to meet standards to prove their performance, or OEMs may approve some for their suited applications. The lubricant’s performance standards should be compared to those outlined by the OEM for a particular piece of equipment. If they don’t match or there are discrepancies, then the OEM or lubricant supplier should be contacted for verification. Sometimes, an over-qualified lubricant may be used in your application, and it can also give you the expected results, but of course, at a higher cost.
Lubricants are the lifeblood of our equipment and keep our industry moving. We need to understand them fully, their roles in our equipment, and how we can optimize them for maximum performance.
References
- Debshaw, B. (2023, February 02). Reducing Costs, Increasing Production: The Remarkable Impact of Predictive Maintenance. Retrieved from Precision Lubrication Magazine: https://precisionlubrication.com/articles/predictive-maintenance/
- Mathura, S. (2024, April 01). Lubricant Additives: A Comprehensive Guide. Retrieved from Precision Lubrication Magazine: https://precisionlubrication.com/articles/lubricant-additives/
- Mathura, S. (2023, March 26). Oil viscosity: A practical guide. Retrieved from Precision Lubrication Magazine: https://precisionlubrication.com/articles/oil-viscosity/
- Britton, R. (2023, January 26). How do Solid Lubricants work? Retrieved from Precision Lubrication Magazine: https://precisionlubrication.com/articles/solid-lubricants/
- Hamrock, B. J., Schmid, S. R., & Jacobson, B. O. (2004). Fundamentals of Fluid Film Lubrication Second Edition. New York: Marcel Dekker Inc.
- Pirro, D. M., Webster, M., & Daschner, E. (2016). Lubrication Fundamentals, Third Edition, Revised and Expanded. Boca Raton: CRC Press.
- Pirro, D. M., Webster, M., & Daschner, E. (2016). Lubrication Fundamentals, Third Edition, Revised and Expanded. Boca Raton: CRC Press.
- Hamrock, B. J., Schmid, S. R., & Jacobson, B. O. (2004). Fundamentals of Fluid Film Lubrication Second Edition. New York: Marcel Dekker Inc.