Lubricants keep the world turning. Once something moves, a lubricant should be present to reduce friction or wear between the surfaces. But what makes lubricants so unique in our industry? Is it just the base oil?
No, this is where the power of lubricant additives truly shines, an area many overlook. This article focuses more on the industry’s unsung heroes, the types involved, their functionalities, and some challenges.
Why Do We Need Lubricant Additives?
Before getting into the world of additives, let’s step back to the basics: why are they needed? A lubricant is composed of base oil and additives. Depending on the type of oil, different ratios of additives will be used for the various applications. Additionally, each Lubricant OEM will have its unique formula for its lubricant.
To simplify this, we can think of making a cup of tea. The first thing we need is some hot water in a cup. This can be our base oil. It can be used on its own (some people drink hot water or use it for other purposes), but if we want to make a cup of tea, we must add stuff.
Depending on the purpose for which you’re drinking the tea, you may choose a particular flavor. Perhaps peppermint for improved digestion or to help improve your concentration or chamomile to keep you calm.
These flavors can represent the various types of oils: gear oils, turbine oils, or motor oils. Different blends are suited for different applications.
Now, while we’ve added the tea bag to the hot water (and some people can drink tea like this), others need to add sweetener or milk. These are the additives to the base oil (hot water).
Depending on the preference of the person drinking the tea, there will be varying amounts of sweetener (honey, stevia, or sugar) and varying amounts of milk (regular, low-fat, oat, dairy-free). The combinations are endless!
The same can be said of additives in finished lubricants. Depending on the type of oil (tea flavor, think gear or turbine oil) and its application (the person drinking the tea, with dietary preferences of being dairy-free or sugar-free), the combination of lubricant additives and their ratios will differ. The percentage of additives can vary from 0.001 to 30% based on the type of oil.
Additives have three main functions in a finished lubricant. They can;
- Enhance – improve some of the properties of the base oil
- Suppress – reduce some of the characteristics of the base oil
- Add new properties – introduce new features to the base oil
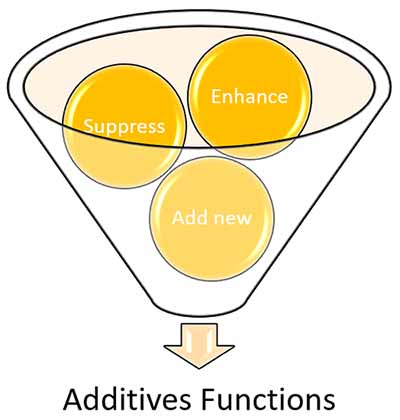
Figure 1: Functions of lubricant additives
The finished lubricant will have properties from the base oil and additives combined. Let’s explore how these additives function and their characteristics a bit further.
Types of Lubricant Additives
There are many types of lubricant additives, and various formulations exist from different suppliers. In this section, we will cover the most common additives found in finished lubricants.
Pour Point Depressants
All liquids have a particular temperature at which they can effectively flow. The liquid’s viscosity and current temperature determine how quickly it moves. As the name implies, pour point depressants can assist in lowering the temperature at which the lubricant flows1.
Viscosity Index Improvers
Viscosity Index Improvers are also known as Viscosity Modifiers2. They assist the lubricant in increasing its viscosity at higher temperatures, allowing lubricants to operate in wider temperature ranges.
Friction Modifiers
When two surfaces rub against each other, friction is formed. Depending on the type and extent of friction, some surfaces can experience welding and even adhesive wear. This is where friction modifiers can help by reducing frictional forces associated with stick-slip oscillations and noises.
Defoamants (Antifoam)
Some lubricants succumb to foam being created in their systems. When foam is made, it significantly impacts the functions of the lubricant and can lead to excessive wear due to lack of lubrication (they disrupt the surface of the lubricant), cavitation (due to the presence of air bubbles), and even increased oxidation (due to presence of air trapped in the system). Foam can also affect the ability of a liquid to transfer heat or cool. Defoamants or antifoam additives reduce the amount of foam being produced.
Oxidation Inhibitors (Antioxidants)
Oxidation occurs in most lubricants. During the oxidation process, free radicals emerge, propagating to form alkyl or peroxy-radicals and hydroperoxides, which eventually react with others to form oxidation by-products. During the propagation phase, antioxidants are usually deployed to neutralize the free radicals or decompose the hydroperoxides3. As such, these additives are sacrificial in nature, as they protect the base oil from oxidation by being depleted.
There are many types of antioxidants, including phenolics and aromatic nitrogen compounds, hindered phenols, aromatic amines, zinc dithiophosphates, and a couple of others.
Rust and Corrosion Inhibitors
If oxygen and water are present at a location containing iron, then rust can be formed. Corrosion affects the non-ferrous metals in the presence of acids in the lubricant1. Most pieces of equipment succumb to rust and corrosion quite easily, so these inhibitors were developed to mitigate these effects by forming protective layers on the surfaces of the equipment.
Detergents and Dispersants
Detergents and dispersants often get confused as they usually work together to prevent deposits from accumulating in the oils. Detergents neutralize deposit precursors (especially in engine oils), while dispersants suspend the potential sludge or varnish-forming materials4.
Antiwear Additives
Antiwear additives reduce friction and wear, especially during boundary lubrication conditions. They are designed to reduce wear when the system is exposed to moderate stress2.
Extreme Pressure Additives
Extreme Pressure additives are usually confused with antiwear additives, or the names are used interchangeably. However, extreme pressure additives begin to work when the system experiences high stress and try to prevent the welding of moving parts, unlike antiwear additives, which work when the system experiences moderate stress.
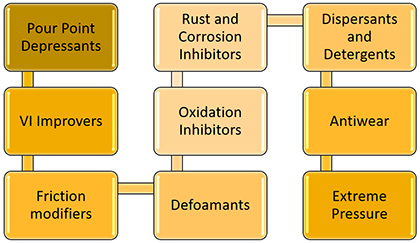
Figure 2: Types of Lubricant Additives
How Do Lubricant Additives Work?
Each additive works differently to produce its function on the base oil and the overall finished lubricant. This section will explore how each of the lubricant additives works and some of the challenges they may experience.
Pour Point Depressants
As noted above, the pour point depressants help control the flow of the lubricant. This is achieved by modifying the wax crystals present in the lubricant’s base oil. At lower temperatures, the liquid usually has trouble being poured due to the presence of wax molecules in the base oil1.
There are two main types of pour point depressants, namely;
- Alkylaromatic polymers adsorb on the wax crystals as they form, thus preventing them from growing and adhering to each other. This effectively controls the crystallization process and ensures the lubricant can be poured.
- Polymethacrylates co-crystallize with wax to prevent crystal growth.
While these additives do not entirely prevent wax crystal growth, they lower the temperature at which these rigid structures are formed. These additives can achieve a pour point depression of up to 28°C (50°F); however, the common range is typically between 11-17°C (20-30°F).
Solubility thresholds may limit the use of this type of additive to achieve the desired effect on the base oil.
Viscosity Index Improvers
These additives are typically long-chain, high-molecular-weight polymers that change their configuration in the lubricant based on temperature4. When the lubricant is in a cold environment, these polymers adopt a coiled form to minimize the effect on viscosity. On the other hand, in a hot environment, they will straighten out, allowing the oil to produce a thickening effect.
While it is more desirable to use high molecular weight polymers (since they provide a better thickening effect), these long-chain molecules are also subject to degradation due to mechanical shearing. Therefore, a balance must be reached between the molecular weight and shear stable service condition.
Another challenge for formulators is to balance the polymer’s tendency to shear with the expected viscosity thickening due to oxidative processes and the viscosity thinning due to the dilution of fuel1.
Friction Modifiers
These usually compete with the antiwear and extreme pressure additives (and other polar compounds) for surface room. However, they become activated at temperatures when the AW and EP additives are not yet active. Thus, they form thin mono-molecular layers of physically adsorbed polar soluble products or tribochemical friction-reducing carbon layers, which exhibit a lower friction behavior than AW and EP additives2.
There are different groups of friction modifiers based on their function. Some are mechanically working FMs (solid lubricating compounds, e.g., Molybdenum disulfide, graphite, PTFE, etc.), adsorption layers forming FMs (e.g., fatty acid ester, etc.), tribochemical reaction layers forming FMs, friction polymer forming FMs and organometallic compounds.
Defoamants (Antifoam)
When foam forms in the lubricant, tiny air bubbles become trapped either at the surface or on the inside (called inner foam). Defoamants work by adsorbing on the foam bubble and affecting the bubble surface tension. This causes coalescence and breaks the bubble on the lubricant’s surface1.
For the foam that forms at the surface, called surface foam, defoamants with a lower surface tension are used. They are usually not soluble in base oil and must be finely dispersed to be sufficiently stable even after long-term storage or use.
On the other hand, inner foam, which is finely dispersed air bubbles in the lubricant, can form stable dispersions. Common defoamants are designed to control surface foam but stabilize inner foam2.
Oxidation Inhibitors
As noted above, antioxidants are usually deployed during the propagation phase to neutralize the scavenging radicals or decompose the hydroperoxides3. There are two main forms of antioxidants: primary and secondary antioxidants.
Primary antioxidants, also known as radical scavengers, remove radicals from oil. The most common types are amines and phenols.
Secondary antioxidants are designed to eliminate peroxides and form non-reactive products in the lubricant. Some examples include zinc dithiophosphate (ZDDP) and sulphurized phenols.
Mixed antioxidant systems also exist where two antioxidants have a synergistic relationship. One example is the relationship between phenols and amines, where phenols deplete early during oxidation while amines deplete later. Another example is using primary and secondary antioxidants to remove radicals and hydroperoxides.
Rust and Corrosion Inhibitors
Rust and Corrosion inhibitors are usually long alkyl chains and polar groups that can be adsorbed on the metal surface in a densely packed formation of hydrophobic layers.
However, this is a surface-active additive, and as such, it competes with other surface-active additives (such as antiwear or extreme pressure additives) for the metal surface. There are two main groups for corrosion additives: antirust additives (to protect ferrous metals) and metal passivators (for non-ferrous metals2).
Rus inhibitors have a high polar attraction to metal surfaces. They form a tenacious, continuous film that prevents water from reaching the metal surface. It must also be noted that contaminants can introduce corrosion into an oil, just as organic acids are produced.
Detergents and Dispersants
Detergents are polar molecules that remove substances from the metal surface, similar to a cleaning action. However, some detergents also provide antioxidant properties. The nature of a detergent is particularly important as metal-containing detergents produce ash (typically calcium, lithium, potassium, and sodium)1.
On the other hand, dispersants are also polar, and they keep contaminants and insoluble oil components suspended in the lubricant. They minimize particle agglomeration, which in turn maintains the oil’s viscosity (compared to particle coalescing, which leads to thickening). Unlike detergents, dispersants are considered ashless. They typically work at low operating temperatures.
Antiwear Additives
These are typically polar with long chain molecules that adsorb onto the metal surfaces to form a protective layer. This can reduce friction and wear under mild sliding conditions. Usually, these additives are formed from esters, fatty oils, or acids, which can only work at low or moderate levels of stress within the system.
The most common form of antiwear is ZDDP, which is used in engine or hydraulic oils. On the other hand, an ashless phosphorus type of antiwear also exists for systems that require that characteristic, and tricreysl phosphate is the usual choice.
Extreme Pressure Additives
Since extreme pressure additives only become active when higher temperatures or heavier loads are on a system, they have earned the name “Anti-scuffing additives.”
Unlike antiwear additives, extreme pressure additives react chemically with the sliding metal surfaces to form relatively insoluble surface films. This reaction only occurs at higher temperatures, sometimes between 180-1000°C, depending on the type of EP additive used1.
It must be noted that even with the presence of EP additives in a lubricant, there will still be some wear during the break-in period as the additives have yet to form their protective layers on the surfaces.
EP additives must also be designed for the system they protect as different metals have varying reactivity (EP additives designed for steel-on-steel systems may not be appropriate for bronze systems as they are not as reactive with bronze).
EP additives also contribute to polishing the sliding surfaces as they experience the most significant chemical reaction when the asperities are in contact and the localized temperatures are at their highest. They tend to be created from compounds containing sulphur, phosphorus, borate, chlorine, or other metals4.
Do Lubricant Additives Degrade Over Time?
As noted earlier, most additives can deplete over time as they get used up in their various functions. Antiwear and rust protection additives continuously coat the surfaces of the interfacing metals.
This can cause their initial concentrations to decrease over time until it reaches a point where the concentration of the additive is too low to offer any protection. In this case, it has not degraded but depleted.
In earlier years, there used to be prevalent issues with the separation of additives from the finished lubricant due to filtration. However, with the evolution of technology and better practices, this is no longer a common problem operators face.
In the past, operators would notice frequent clogging of their filters and subsequent reduction of additive concentrations, rendering the oil unprotected. It was common to notice additives settling to the bottom of a drum of oil after standing still for some time.
In essence, lubricant additives do not really degrade over time; rather, their concentrations get depleted, which assists in the lubricant degrading faster than a finished lubricant with higher additive concentrations.
Innovation and Future Trends for Additives
What does the future look like for additives within our industry? Will they go away completely?
From my estimations, we’re a long way from that happening. The lubricant industry has evolved over the years, with many advances from the chemical side, which has developed better-suited additives, and the OEM side, which has pushed the chemists to develop lubricant additives that can adapt to equipment changes.
OEMs are creating more components that can withstand higher temperatures, increased pressures, and more demanding environments. Lubricants must also be developed for this specific use, and additive technology will continue to evolve as these boundaries are pushed.
We are also being driven towards more environmentally friendly products, and additives are also on that list. Most of the metals used in the production of additives (such as EP or AW additives) are toxic to the environment, and alternatives are being discovered.
In the field of tribology, there has also been continued research into ways of reducing friction and wear. This is coupled with research into the interaction of varying surfaces and ways lubricants can effectively reduce the coefficient of friction, leading to increased energy efficiency and fuel efficiency in some cases.
Lubricant additives will be around for some time as everything that moves needs to be lubricated, and base oils do not have all the required properties to handle varying temperatures and other conditions that the machine encounters.
While their structure will change to adapt to provide a more environmentally friendly impact, their functions will also evolve based on their future requirements.
References
1 Bruce, R. W. (2012). Handbook of Lubrication and Tribology, Volume II Theory and Design, Second Edition. Boca Raton: CRC Press.
2 Mang, T., & Dresel, W. (2007). Lubricants and Lubrication – Second Completely Revised and Extended Edition. Weinheim: WILEY-VCH GmbH.
3 Livingstone, G., Wooton, D., & Ameye, J. (2015). Antioxidant Monitoring as Part of Lubricant Diagnostics – A Luxury or a Necessity?
4 Pirro, D. M., Webster, M., & Daschner, E. (2016). Lubrication Fundamentals – Third Edition Revised and Explained. Boca Raton: CRC Press.