Many lubrication engineers are faced with finding the most appropriate lubricant for an application. Therefore, they are tasked with selecting the “right” lubricant; subsequently, their decision can influence several outcomes.
A lot of the positive results are in the realm of extending the life of the oil, providing better energy efficiency, and even saving costs associated with downtime. However, can the choice of an “incorrect” lubricant impact its degradation process or lead to the presence of lube oil varnish?
Has the Lubricant Failed the Equipment, or Has the Equipment Failed the Lubricant?
Lubricants provide many different functions. These can range from moving heat or contaminants away from the components, minimizing wear and friction, improving efficiency, providing information about the status of the lubricant, or even transmitting power, as is the case with hydraulic oils.
There has been the time aged question of whether a lubricant fails the equipment or the equipment has failed the lubricant. If a deeper dive is performed into this question, one can deduce that lubricants are engineered to withstand particular conditions.
Once those conditions are met, lubricants can perform their intended functions. However, if the conditions exceed the tolerances of the lubricant, then one will notice a faster degradation. In this case, the environment and its conditions have failed the lubricant.
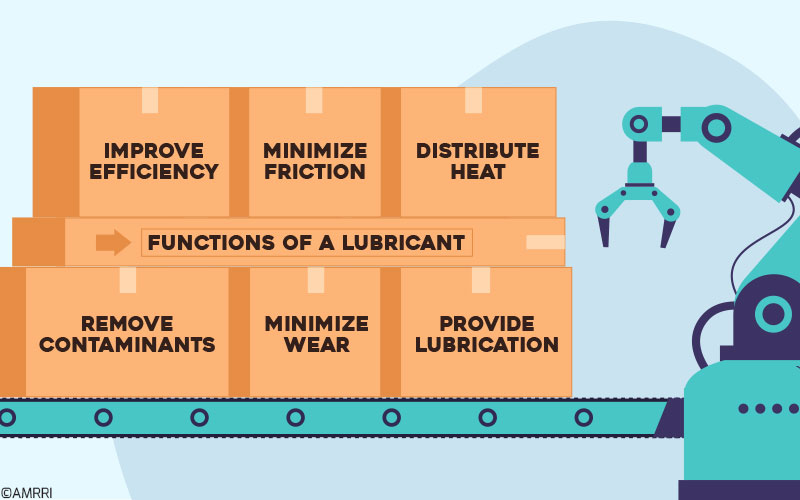
Some Functions of a Lubricant
On the other hand, lubricants are designed to be sacrificial and are used up while in service. Hence, it is normal to see additives’ values deplete when trending oil analysis values, especially for turbine oils. Quite notably, additives responsible for antiwear or extreme pressure will decrease over time as they protect the components.
For this instance, the lubricant would have been performing its function until it could no longer do so or has reached its end of life. The conditions in the environment cannot be blamed for the lubricant failing. This is the nature of the lubricant.
Lubricant condition monitoring lets analysts detect whether a lubricant is undergoing degradation and can even help determine some areas where it has begun to fail. For instance, if the RULER® test can quantify the remaining antioxidants in an oil. Analysts can easily interpret its results to determine if the process of oxidation is occurring within that lubricant.
Similarly, an FTIR test can detect whether contaminants are present in the lubricant or if the additive packages have become severely depleted. These tests all aid in allowing analysts to successfully determine whether or not a lubricant is performing at its full functional capacity.
Which Mechanism Is Affected?
My previous article published in Precision Lubrication covered six degradation mechanisms: oxidation, thermal degradation, microdieseling, electrostatic spark discharge, additive depletion, and contamination.
Upon further investigation, there are only three mechanisms where selecting the correct lubricant will impact the degradation mode. These are; oxidation, microdieseling, and electrostatic spark discharge. The properties of the lubricant can easily influence each of these degradation mechanisms.
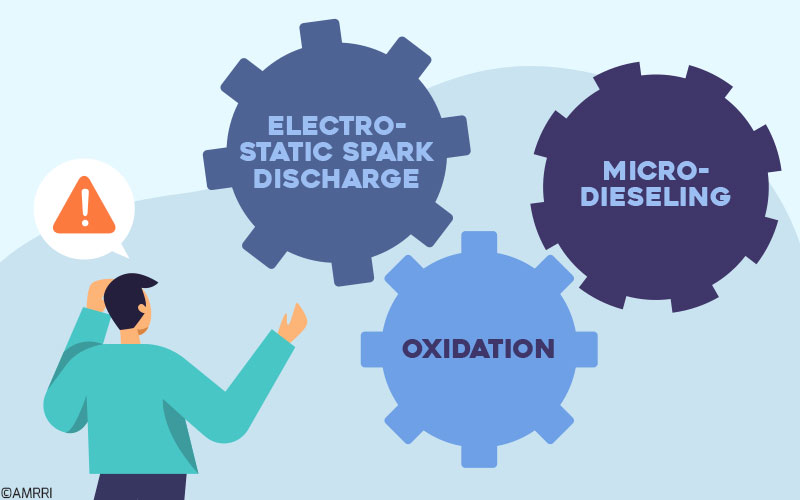
Mechanisms That are Affected by Incorrect Lubricant Selection
When selecting a lubricant, especially for rotating equipment, one of the critical areas of importance is the performance of the antioxidants. When formulated, oils must be balanced to protect the components in various aspects.
Thus, some oils that boast a high level of antioxidants may suffer from low levels of antiwear, or these increased levels can react with other components to reduce the performance of the oil. During oxidation, antioxidants are depleted at an accelerated rate which can lead to lube oil varnish. Hence, the choice of lubricant can influence this degradation mechanism.
A good trending test, in this case, would be the RULER test to accurately quantify and trend the remaining useful antioxidants for the oil. This test can easily distinguish and quantify the type of antioxidant rather than providing an estimate of the oxidation, as with the RPVOT test.
It has been noted that oils with an RPVOT of more than 1000 mins have a low reproducibility value which can mislead users during trending of lubricant degradation. Corrosion inhibitors, not just antioxidants, have also influenced the RPVOT values. Thus, there are better tests for monitoring the presence of antioxidants and helping operators to detect the onset of possible lube oil varnish.
On the other hand, during microdieseling, entrained air can lead to pitting the equipment’s internals and eventually the production of sludge or tars depending on whether the entrained air experiences a high or low implosion pressure.
If bubbles become entrained in the lubricant and do not rise to the surface, this can directly result from the lubricant’s antifoaming property. The antifoaming property is essential when selecting an oil, especially for gearboxes. Typically, OEMs will have recommendations for their components that should be followed.
Another degradation mechanism that can be influenced by lubricant selection is electrostatic spark discharge. This mechanism occurs when the lubricant accumulates static electricity after passing through tight clearances. These then discharge at the filters or other components inside the equipment, providing sharp points or ideal areas to allow static discharge.
This is frequently seen in hydraulic oils due to the very tight clearances within the equipment. If fluid conductivity is above 100 pS/m, the risk of static being produced is reduced. Some OEMs also provide particular values the lubricant should meet for this property.
The Influence of Lubricant Selection
Guidelines should always be followed when selecting a lubricant for a particular application. OEMs will have specific criteria ranges for specialty applications that must be satisfied. Some general guidelines which should be considered can be summarized in the table below based on the listed mechanisms above.
Based on the three listed mechanisms above, one can identify that choosing a lubricant can impact the type of degradation which occurs during its lifetime. As such, when selecting lubricants, it is critical to note their applications and the conditions they will endure.
Having a history of lubricant failures for particular equipment can also assist in this regard by informing users of past failure trends. Therefore, when selecting a lubricant, operators can be more mindful of the properties which should not be compromised during the selection process.
The process of troubleshooting degradation in lubricants has been covered in detail in the book, “Lubrication Degradation – Getting Into the Root Causes” by Bob Latino and myself, published by CRC Press, Taylor and Francis.