Varnish is a type of deposit that forms on the surface of equipment in lubrication systems. It is caused by the oxidation of the base oil and the buildup of additives in the oil over time, forming a sticky, varnish-like substance. Lube oil varnish can cause problems in equipment operation by clogging filters, reducing oil flow, and leading to valve sticking and pump failures.
Lube oil varnish is no stranger to the manufacturing industry. It constitutes the substance of most operators’ worst nightmares and plant managers’ ultimate fears. For those who have been in the industry for the last decade, varnish is the sticky subject that unites all facility departments.
It can cause an entire manufacturing plant to shut down while sending the finance department into a frenzy trying to balance production loss with incoming repair costs. In the fight against lube oil varnish, all teams need to work together to ensure that it can be managed and possibly eliminated from the system.
What Is Oil Degradation?
Before diving into the world of varnish, one must first understand how it forms and the circumstances which have led to its existence. Within the industry, the term varnish is used loosely to define any form of lubricant-derived deposit found in industrial.
However, oil can degrade by several mechanisms, which require various conditions for degradation—as such, using the term varnish to describe any deposit formed within a machine does not suggest its mechanism of formation.
The lubricant begins its degradation journey from the moment the lubricant enters the machine.
A lubricant is composed of base oil and additives, of which infinite combinations exist. Additives are carefully engineered to protect the base oil and the equipment. As such, they can become depleted over time, leading to the degradation of the lubricant.
This becomes concerning when the additive levels have depleted to a threshold where they can no longer protect the base oil or the machine. At this stage, degradation is the most serious concern because its rate is greatly accelerated.
According to Mathura (2020), there are six major forms of degradation under which a lubricant can undergo. While some may argue that these can be grouped, some characteristics set these mechanisms apart.
Each mechanism has unique environmental factors which contribute to producing different types of deposits. It is critical to note that identification of the type of mechanism can assist operators in performing remedial works on their equipment to aid in preventing the formation of varnish.
6 Modes of Oil Degradation
The Six Forms of Lubricant Degradation
Oxidation
The most common form of degradation is oxidation. While this is the most recurrent form of degradation, the term is often misused to describe all forms of degradation. During Oxidation, a free radical is formed, which is highly reactive. Its primary purpose is to create other free radicals which can attack the base oil.
However, lubricants have been formulated with antioxidants. These knights in shining armor react with the free radicals to neutralize them and protect the base oil. As such, during the oxidation process, one will notice a decline in the concentration of antioxidants typically evaluated using the RULER® (Remaining Useful Life Evaluation Routine) test.
Eventually, the antioxidants become depleted, and the free radicals begin attacking the base oil. During this stage, polymerization can occur, which leads to the formation of deposits within the lubricant. Not every deposit is chemically similar.
The deposit will gain its characteristics from its environment and the products present during the chemical reaction. When these deposits occur, they can get lodged in the smaller clearances (particularly servo valves), which leads to possible malfunctioning of the equipment. Due to the nature of lube oil varnish, it can act as an insulating layer that increases the temperature throughout the equipment.
Thermal Degradation
Another form of degradation is called thermal degradation. As its name suggests, heat is one of the environmental conditions required for this degradation mechanism. During thermal degradation, the oil can experience temperatures over 200°C.
The Arrhenius equation is one of the industry’s rules of thumb whereby for every 10°C rise over 60°C, the life of the oil is essentially halved. At 200°C, the oil is cooked and produces carbon-based deposits, which is this mechanism’s characteristic type of deposit. The FTIR (Fourier Transform Infrared) test is instrumental in identifying the presence of these deposits.
Microdieseling
One can argue that microdieseling is a form of thermal degradation and should be classed as such. However, during microdieseling, air becomes entrained in the oil and moves from a low-pressure zone to a high-pressure zone.
If the oil does not have good air release properties, then the entrained air will not make its way to be dissipated at the surface. This entrained bubble in the oil can cause temperatures to rise to 1,000°C.
The bubble interface usually experiences some carbon accumulation and then implodes. This can be through a high implosion pressure which results in soot, tars, or sludge, or through a low implosion pressure which can form carbon insolubles such as coke, tars, or resins.
Electrostatic Spark Discharge
Electrostatic spark discharge may be classified under thermal degradation as it involves temperatures over 10,000°C. During this mechanism, oil builds up static electricity at a molecular level when the dry oil passes through tight clearances in the equipment.
Eventually, the static will build to a point where it produces a spark, and free radicals are formed. This can lead to uncontrolled polymerization producing varnish, sludge, or other insoluble materials. One of the tell-tale signs of this mechanism is the presence of burnt patches of membranes on the filters.
Additive Depletion
Additive depletion is often a form of degradation which gets left behind. As stated earlier, additives are sacrificial and will be depleted over time. Their purpose is to protect the lubricant and the machine, but they can be significantly depleted in some instances, leaving them vulnerable.
This type of degradation can produce two types of deposits, organic or inorganic. During degradation, rust and oxidation additives can become reacted with other components. These types of reacted additives can form organic deposits.
Alternatively, inorganic deposits such as ZDDP (Zinc dithiophosphate) can deplete and form a tenacious layer. The Depletion of ZDDP will impact the wear rate as this is the antiwear additive.
Contamination
Often, the most unrecognized form of degradation is contamination. Some may argue that this is not a form of degradation. On the contrary, this degradation mode can be the initiator for other mechanisms such as oxidation, thermal degradation, or even microdieseling.
Essentially, contamination occurs when foreign material is present in the lubricant. Often, this foreign material can become a catalyst for one of the other forms of degradation. Therefore, it must be acknowledged separately, as only the degradation mode can be eliminated by removing the contaminant.
Can Lube Oil Varnish be Detected?
Detecting something is the first step towards formulating a solution to minimize its effects or eliminate it from a system. In the case of varnish for lubricated assets, a few technologies are currently being used to detect its presence.
As seen at the beginning of this article, varnish can exist with various characteristics depending on the degradation mechanism which aided in its formation. For this article, the degradation mechanism of oxidation will form the main focus as it is the most prevalent pathway to lube oil varnish formation.
During oxidation, the first chemical change which can be observed in the lubricant is the depletion of the antioxidant additives. This is where the knowledge of phenols and amines is critical.
As per Livingstone et al. (2015), these antioxidants can form synergistic mixtures in mixed antioxidant systems. When the free radicals react with the phenols, they become depleted but can regenerate amines. Thereby, the phenols are sacrificial.
Thus, when performing the RULER analysis, one can find that the concentration of the phenols will typically deplete quicker than the amines. This provides the analyst with a good overview of the amount of oxidation that has taken place in the lubricant.
The RULER analysis is one of the oil analysis methods which can provide early detection of the occurrence of oxidation.
It has been shown that the physical changes, such as polymerization, will only begin after this chemical change of the depletion of antioxidants. It is at this point that the actual deposits will begin formation.
Unfortunately, oil analysis tests such as viscosity and acid number only show significant changes after the deposits have been formed. At this time, it may be too late to implement technologies to mitigate varnish formation.
The Membrane Patch Calorimetry (MPC) oil analysis test (ASTM D7843) can offer analysts insight into the estimated amount of insoluble varnish currently within the system. These results have three main ranges which identify the severity of the varnish, namely, 0-20 (Normal), 20-30 (Abnormal), and >30 (Critical). Oil analysis tests can effectively provide the operators with some awareness of the current condition of the lubricant and its tendency to form varnish.
Is Oil Analysis the Only Method of Varnish Detection?
Varnish will deposit in layers and adhere to the metal surfaces inside the equipment. As it continues to deposit, the layers will eventually accumulate until it reaches a point whereby it can cause significant changes to the clearances of the components.
There have been instances where shafts in rotating pieces of equipment have been moved due to the build-up varnish. This is where vibration analysis can be instrumental.
When the vibration analysis method is used, it can detect any small changes in the alignment of the shaft in rotating equipment. As varnish continues to build on the inside of the component, vibration analysts can detect if the shaft observes some misalignment over a period.
This may be easy to miss as sometimes the varnish which has built up can be wiped away, causing the shaft to resume its proper alignment. Thus, these technologies should be used in tandem before conclusions are made about the presence of varnish.
Another detection method that can be employed is the monitoring of temperature fluctuations. As stated earlier, varnish can form an insulating layer trapping heat. There have been case studies that demonstrate that bearings experiencing varnish tend to display temperature increases.
Typically, these temperature patterns assume a saw-tooth pattern where temperatures rise continuously as the varnish builds up. The varnish becomes wiped away, and the temperature is reduced drastically.
This saw tooth pattern of temperature variation is characteristic of varnish formation. In some cases, the formation of localized deposits on bearing surfaces may cause temperature escalations without a corresponding MPC increase. In this case, the bulk oil may not show any degradation, yet temperature excursions may be experienced at the bearing surface.
Can Lube Oil Varnish be Eliminated?
Varnish can be likened to cholesterol in the human body. It can build up in our arteries and eventually clog those, causing restrictions in blood flow to our heart which may lead to a heart attack.
Humans cannot simply change their blood to remove the cholesterol build-up. However, cholesterol is controlled through proper diet, exercise, and with some condition monitoring in the form of blood tests to help gauge the presence of it in the bloodstream. Similarly, a couple of approaches can be used to reduce the varnish build-up or eliminate it.
As per Livingstone et al. (2011), the lifecycle of varnish is critical. Particular attention should be paid to the double arrows between the stages of Solubility to Varnish formation in the figure below.
This means that even after varnish has been deposited, it can be solubilized back into the oil. This can only occur if conditions are met per Hansen’s Solubility principles where the solvent and degradation products meet using the three parameters of Polarity, Hydrogen Bonding, and Dispersive Forces as discussed in “The Hansen Solubility Principles and Its Relation to Varnish” (2022).
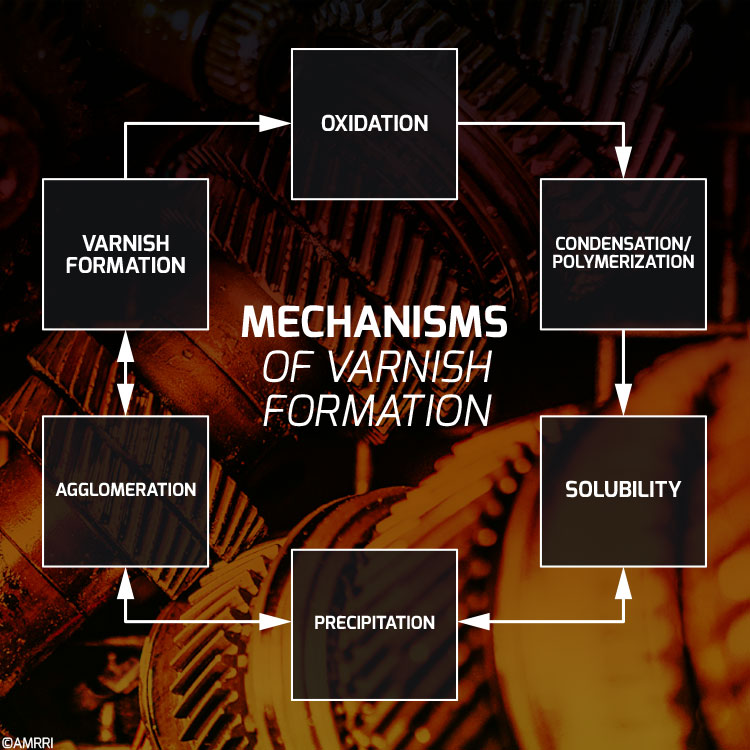
The Varnish Lifecycle as per Livingstone et al. (2011)
Varnish exists in various forms and can consist of differing compositions. Hence, it is essential to understand the characteristics of the varnish being formed in a system before attempting to eliminate it.
There are certain technologies, such as solubility enhancers or specifically engineered filtration media, which can be effective at removing lube oil varnish. However, this technology is heavily reliant on the type of varnish being formed and can be customized as per the system accordingly.
Solubility enhancers can solubilize the varnish back into the oil solution. When these deposits are reintroduced into the oil, they can be removed using resin-based filtration. In this method, the media is specifically designed to allow for the adsorption and removal of the varnish which presently exists in the oil.
When these methods are used together, they can prove quite effective and prevent manufacturing plants from experiencing unwanted downtime.
To summarize, it is of utmost importance to first understand the characteristics of the varnish being produced in your equipment before attempting to remove it from your system.
There is no cookie-cutter method to eliminate varnish from a system as it is a complex deposit. Similar to practices we observe with our bodies in the instances of cholesterol build-up, we can employ methods of dissolving the varnish and removing it while monitoring for possible recurrences in the future.
References:
Livingstone, Ameye, & Wooton. (2015.). Antioxidant Monitoring as Part of Lubricant Diagnostics – A Luxury or a Necessity? OilDoc, Rosenheim, Germany.
Livingstone, Overgaag, & Ameye. (2011). Advanced removal Techniques for Turbine oil Degradation Products. Powergen Milan.
Mathura, S. (2020). Lubrication Degradation Mechanisms (CRC Press Focus Shortform Book Program) (1st ed.). CRC Press.
The Hansen Solubility Principles and its Relation to Varnish. (2022, July 31). Fluitec International. https://www.fluitec.com/the-hansen-solubility-principles-and-its-relation-to-varnish/
Photo credit: Asset Reliability LLC www.assetreliable.com