Pour Point Temperature – What Is It?
The Pour Point Temperature is the temperature below which an oil loses its flow characteristics. It can be found in most Product Data Sheet (PDS) for an oil and in “Section 9: Physical and Chemical Properties” of the Safety Data Sheet (SDS).
To be more precise, the quoted temperatures are 3°C above the temperature at which the oil exhibits no surface movement when the tube in which the test oil is contained is tilted and then shows no signs of flow when the tube is then held horizontally.
What Is Causing the Oil to Stop Flowing?
Generally, the viscosity increases exponentially as the temperature drops, eventually resulting in the oil not flowing.
However, crude-derived mineral oils, specifically those of a paraffinic base, are more likely to thicken due to the solidifying of the wax, resulting in a crystalline matrix restricting the flow.
What Factors Typically Influence the Pour Point Temperature of An Oil?
The pour point temperature is primarily determined by the oil’s viscosity and molecular structures and the presence of paraffinic wax within the base oil. Consequently, the higher the viscosity, the higher the pour point temperature; similarly, the higher the pour point temperature for paraffinic base oils.
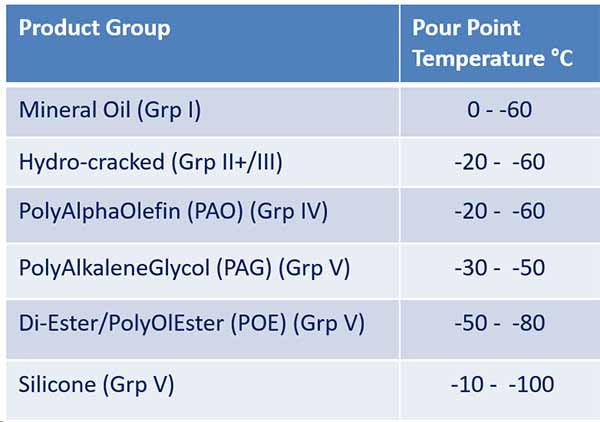
Ranges of Pour Point Temperatures for differing base oil types. Note that viscosity will affect the value with the lower viscosity oils capable of lower values.
The previous thermal history of an oil can also affect the Pour Point Temperature, which influences the result and, thus, the method used in testing the oil.
Two differing pour points can be measured, and a range can be determined based on thermal history. The sample may appear liquid or solid within this range because the wax crystals form less readily when the sample has been heated within the previous 24 hours, and this contributes to the lower of the two Pour Points measured.
Can Additives Control the Pour Point Temperature?
Pour Point Depressants or Improver additives can help lower the Pour Point Temperature. Typically, these consist of paraffin-alkylated naphthalenes, phenols, and polymethacrylates, which delay the contraction of the paraffin crystals.
How Is the Pour Point Temperature of An Oil Measured?
There are two test methods for testing the Pour Point Temperature:
Manual Method (ASTM D97, ISO 3016 or IP 15) in which the oil is cooled at a controlled rate in a glass container. On reaching a temperature 9°C above the predicted or expected Pour Point Temperature, the test container is removed and tilted to check for signs of movement.
This is repeated at drops of 3°C in temperature until such time that the oil shows no movement for 5 seconds when the container is held horizontally. The Pour Point Temperature is then quoted as this temperature plus 3°C or the temperature at the stage before the completion of the test.
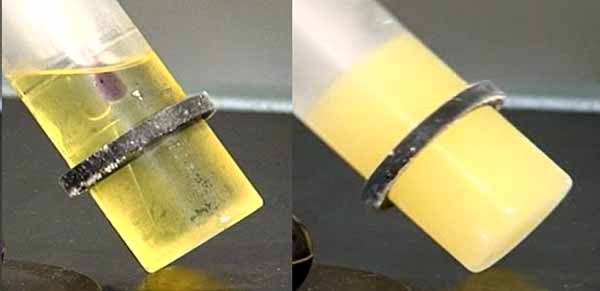
Manual testing inspection for movement when tilting the tube, with the image on the right showing no movement.
The Automatic Method (ASTM D5949) is an alternative to the manual method. A Peltier device (a thermoelectric form of cooling) heats and cools the oil sample at a rate of 1.5°C per minute.
A pressurized pulse of gas impacts the surface of the oil sample, and multiple optical sensors continuously monitor the sample for movement. The Pour Point is the lowest temperature at which movement is detected on the surface.
The automated method is generally quicker than the manual method, with less complex cooling apparatus required. It can provide Pour Point values from 50° down to almost -60°C, with some test equipment manufacturers claiming an even broader range as low as -80°C. The automated method is also found to have better repeatability and reproducibility than the manual method.

The automated Pour Point Tester from Ducom (www.ducom.com)
Is The Pour Point Temperature the Same As the Solidification Point?
The Solidification Point Temperature is sometimes erroneously confused with the Pour Point Temperature. The Solidification Point is the temperature at which the oil must solidify entirely and is usually 3°C to 5°C below the Pour Point Temperature.
Is the Pour Point Temperature Relevant to Grease?
Greases contain oil, so they can be affected by low temperatures, too, but greases are not tested for their Pour Point Temperature. More likely, though, an operating temperature range is shown in the PDS, with the lower values typically being temperatures of -20°C and down to as low as -60°C for specialist greases.
Is the Pour Point Temperature Measured for Used Oil Analysis?
In short, no. Unlike the Flash Point Temperature test, which could indicate contamination, the Pour Point Test is unlikely to yield any valuable values routinely with used oil analysis. However, that is not to say that the test is irrelevant in a failure investigation and could be undertaken to eliminate or confirm the possible cause, or part of the cause, of the failure.
What Relevance Does the Pour Point Temperature Have with Maintenance And Reliability?
One of the primary concerns when selecting an oil is the ambient and machine operating conditions, particularly the cold start temperatures. Therefore, the viscosity, the viscosity index, and the pour point are especially important when evaluating a candidate oil.
The Pour Point Temperature is extremely important when ambient conditions are below freezing, which impacts the cold start and oil coolers in use.
Depending on the lubricant’s base oil type, the oil becomes cloudy as the paraffins crystallize and cross-link, the viscosity increases exponentially, and the lubricant becomes a solid waxy lump.
The oil cannot flow to the machine’s required parts, whether splash lubricated or pumped, and the lubricant’s wear and friction control properties begin to fail.
Consequently, oils with a much lower pour point temperature (at least 10°C or more) than the expected worst-case ambient conditions should be selected, as it is never a good idea to be within the limit of the lubricant’s pour point.
Typically, industrial machinery may be at risk when not operated continuously, outdoors, or close to the edge of buildings, where wind chills may be an issue.
However, in such situations with hydraulics and turbo-machinery fed from larger tanks, an oil heater will most likely be used to maintain a reasonable temperature to prevent oil cooling issues and aid start-up by lowering the viscosity.
Is It Just a Case of Those In Cold Climates Need To Worry?
Primarily, yes, especially where Winter conditions fall below freezing. However, even in hot climates, the Pour Point Temperature may still be an issue where cold storage is used, as in such cases, the temperatures may be below -18°C, especially in the food, beverage, and pharmaceutical industries.
What About the Storage of Oils?
The storage of industrial oils is also a concern, as with oil, the waxes forming can bind the additive formulations and drag them to the floor of the storage container.
Should these industrial oils be exposed to temperatures below the Pour Point Temperature, selective heating and circulation of the warmed oils can help. For water-miscible lubricants, these should not be used after such a scenario.
What About Automotive Situations?
In the automotive world, vehicles are often left overnight outdoors exposed to both low temperatures and wind chill.
While the Pour Point Temperature is necessary, the Society of Automotive Engineers (SAE) viscosity grading system for engine oils provides viscosity grade categories for Winter grades: 0W, 5W, 10W, 15W, 20W and 25W with a 0W required to give an Absolute Viscosity of 60,000mPa.s or centiPoise at -40°C that allows the oil to be still pumped, with a cold cranking value of 6,200mPa.s.
The SAE transmission oils Winter grades 70W, 75W, 80W, and 85W are required to not exceed 150,000mPa.s at proscribed temperatures with a 70W still able to flow down to -55°C.
As with industrial plants, where criticality and machine complexity require heating, automotive applications may also utilize in-sump heating from an external power source. For example, drivers in Scandinavian countries and North America will be familiar with plugging in a power supply to their vehicle to maintain the oil at a suitable temperature above the Pour Point Temperature.
Pour Point Temperature is essential where there are low ambient temperatures. However, it is not the only value that requires review. Other factors, such as the Viscosity Index, must be considered regarding the extreme between the cold start and the operating temperature.
For this reason, it is also essential to consider the base oil type since a synthetic is likely to provide a lower Pour Point Temperature and a higher Viscosity Index.