Onsite oil analysis is an effective tool to analyze samples and optimize maintenance activities quickly. As part of a comprehensive condition-based maintenance program (CBM), oil analysis effectively complements other diagnostic technologies like vibration analysis, infrared thermography, and ultrasound technology.
However, this critical lubrication monitoring step is often overlooked in grease-lubricated equipment. SKF states that 80% of the world’s bearings are grease-lubricated, leaving a vast opportunity to incorporate grease analysis techniques into the overall CBM strategy.
The Electric Power Research Institute (EPRI) suggests that nearly 50% of bearing failures are related to poor lubrication and contamination1. The development of grease condition monitoring standards, ASTM D7718 and ASTM D7918 have laid the foundation for a consistent methodology to sample and test grease to implement condition monitoring strategies.
By monitoring key data points, such as wear, oxidation, and additive health, the asset manager can transition from calendar-based to condition-based changeouts. This has the potential to save hundreds of thousands of dollars per year for an owner of a large fleet.
The wind, rail, and automotive robotics industries are implementing these strategies into their programs and potentially avoiding thousands in maintenance costs by predicting failures and extending greasing intervals3.
Historically, incorporating any CBM strategy into grease-lubricated components has been challenging.
The small quantity of grease typically available on an in-service component and the limited testing available for small amounts of grease often present barriers to routine grease sampling and analysis.
To address these challenges, grease sampling tools can capture a representative sample from bearings and gears requiring as little as one gram of grease. Onsite analysis tools are available to assess the wear and physical properties of the grease.
This simple sampling technique can be used in various industries, including but not limited to wind, rail, robotics, mining, and nuclear, to sample a large number of grease-lubricated components and evaluate the next actions based on the criticality of the data.
Periodic sampling and analysis of the grease from these components can give asset owners a clearer picture of equipment health, determine grease conditions for optimal change-out periods, and pinpoint latent issues that can be addressed before failure.
Grease Sampling
In most circumstances, procedures for obtaining grease samples from bearing housings and gears are not consistent and likely do not represent the actual condition of the “active” grease near the lubricated surface.
Therefore, the challenge in optimizing a grease analysis program is developing test methodologies that measure in-service grease conditions utilizing a small amount of grease and a sampling process that enables representative grease samples to be taken without disassembly of the component2.
While it is a reality that the user may need to scoop and scrap to the best of their ability to get a sample, there is a standard method that exists for taking in-service grease samples: ASTM D7718 Standard Practice for Obtaining In-Service Samples of Lubricating Grease.
This standard shows several standard methods to take a representative grease sample and utilizes the Grease Thief® sampling device to sample the grease from a bearing, valve, or gearbox.

Grease Thief
Depending on the instrumentation being used, some scoops or tubes may be available with the instrumentation. Speak with your instrument manufacturer and ask which tools are available to sample and measure grease within the instrument. But know, there are standard methods out there to be utilized.
Grease Analysis as a Screening Tool for Fleet Analysis
Routine grease analysis is common in high-value fleet applications such as locomotives, automotive robotics, and wind turbines, where a relatively straightforward set of screening tests for wear and oxidation can guide grease relubrication frequency, cases of mixup, and monitoring wear levels.
Bearing or joint failures could result in millions of dollars in lost product or power, or even worse, could threaten the safety of employees and customers. Asset owners must be able to look at a large quantity of data and pinpoint latent issues where they can focus their resources and prioritize accordingly.
Compared to other diagnostic technologies, grease analysis can detect issues earlier on the P-F interval than vibration analysis, allowing asset owners more time to address the problems and avoid potential downtime.
Once a representative sample is taken, onsite monitoring of the grease sample can be done using existing onsite equipment that was likely purchased for oil analysis.
Onsite Tools for Grease Analysis
Ferrous monitoring tools, handheld infrared spectrometers, and metals spectrometers can be used to measure ferrous debris, physical properties, and contaminants present in the grease. These onsite tools allow for quick monitoring of many samples so immediate action can be taken.
Ametek Spectro Scientific offers a variety of onsite tools like the Ferrocheck, FluidScan, and Spectroil M or 100 that can be used for both onsite oil and grease analysis:
Ferrous Debris Monitoring with the FerroCheck
Ferrous debris monitoring is the most common and cost-effective way to trend wear issues on bearings, gearboxes, or valves. The FerroCheck is a magnetometer that senses the disruption of the magnetic field due to the presence of magnetic particles in the grease.
The particles’ disruption can be directly correlated to the amount of ferrous debris in the grease. The FerroCheck provides a quick, straightforward, non-destructive solution for measuring the ppm of Iron in grease7.
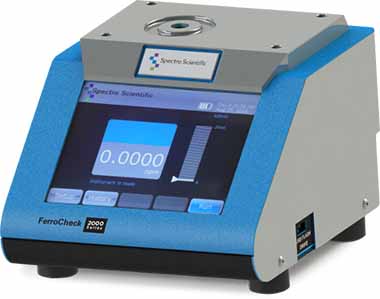
Ferrocheck
Based on the criticality of the component, the sampling frequency can be determined so wear trend analysis and alarm limits can be determined. It’s important to understand that wear particulates in grease are cumulative and, unlike oil, wear particles will remain in the grease until deliberately purged or flushed from the component.
With the ability to detect up to 15% ferrous wear, the FerroCheck is an effective tool for trend analysis and can identify outliers in a fleet application.
Infrared Spectroscopy with the FluidScan
Utilizing the FluidScan (compliant with ASTM D7889), Infrared Spectroscopy is a powerful tool that can be used onsite to measure grease oxidation and identify potential contaminants like moisture or mixtures with other greases.
Monitoring these parameters via trending and direct property analysis makes it possible to inform the user when the grease has completed its useful service. Using a comparison library (over 800 oils and greases), FluidScan can compare the grease sample to the reference to identify potential grease mixing.
If possible, mixing greases is a practice that should be avoided. Mixing of greases can lead to changes in the rheological properties of the grease and eventual separation of the oil from the thickener. If considering mixing two greases, it is best to perform a compatibility study (ASTM D6185) to determine if mixing is acceptable.
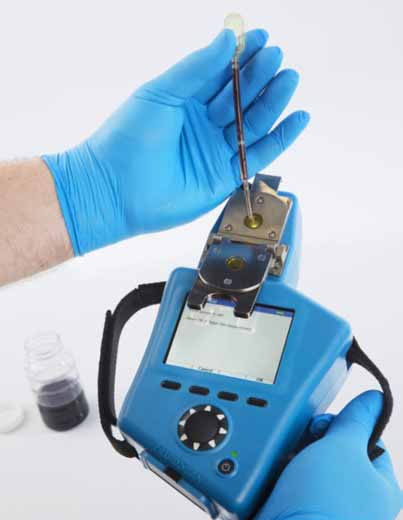
Fluidscan
Moisture and oxidation can also be determined on the FluidScan. A typical moisture peak can appear on the IR Spectrum around 3400cm-1. As these greases age and oxidize, the buildup of oxidation products may be monitored by the FluidScan infrared analysis.
This is translated into an oxidation value and water index. It’s important to note that some polyurea-thickened greases also have a peak on the IR spectrum in this region, and care should be taken not to mistake this peak for moisture.
The polyurea peak at 3400cm-1 will be a short, small peak versus a moisture peak, which will be a larger, broader peak. These same IR masking issues can also occur in greases formulated with an ester-based synthetic base oil.
These greases will show a peak at 1750cm-1, where oxidation also appears. It’s essential to understand when these greases are being used and note this could impact the oxidation and moisture trend values.
As with any effective CBM program, it is important to establish trends and focus on how the grease deviates from the trend. Any significant deviations from the trend would require action. Over time, alarm limits can be established for particular components based on equipment load, runtime, and environmental conditions.
Spectroil M and 100 Series Spectrometer
Using a Rotating Disc Electrode (RDE) Spectrometer, the concentration of metals in the grease can be compared to the new grease to identify significant differences in additive metals that could point toward grease mixing.
Also, the presence of wear metals (Iron, Lead, Tin, and Copper) can be determined. RDE Spectroscopy has been a common laboratory and field method for quick grease analysis over the last 15 years. Sample preparation is important; however, it differs based on early adopter experiences.
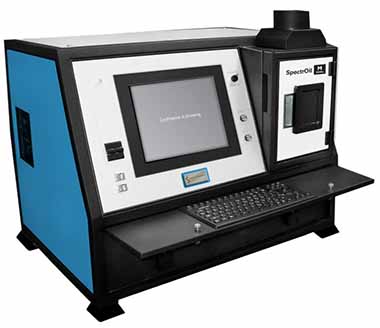
Spectroil M
The two most common preparation methods are dilution (slurry) and wet smear. In the case of dilution (slurry), the grease sample is diluted with a solvent to create a low-viscosity slurry that may be placed in the sample cup and excited as normal.
A second method is the smear (wet) approach whereby a rotrode is rolled in the grease sample to create a coating on the disk edges, and then it is mounted on the shaft, and a sample cup of base oil is used. Either method relies on the consistency of the operator and an understanding of the goals.
The tests and instrumentation listed here for in-service grease testing are not exhaustive.
For a complete list of recommended tests, consider reviewing ASTM D7918 Standard Test Method for Measurement of Flow Properties and Evaluation of Wear, Contaminants, and Oxidative Properties of Lubricating Grease by Die Extrusion Method and Preparation, which discusses additional points to monitor like moisture, color, and consistency. For more information on adding those tests to your grease analysis program, contact MRG Labs.
Acknowledgments & References
Special thanks to Rich Wurzbach, MRG Labs, for sharing his grease analysis knowledge with me over many years.
[1] E. (2001, October). EPRI_Lubrication Guide 1003085. Retrieved from https://www.scribd.com/doc/128347108/EPRI-Lubrication-Guide-1003085
[2] Williams, L. A., & Wurzbach, R. N. (2016). Managing the Health and High Costs of Robotics Using Grease Sampling and Analysis (Tech.). Hot Springs, VA: NLGI National Meeting.
[3] Kowalik, G., & Janosky, R. (2017). Advancements in Grease Sampling and Analysis Using Simple Screening Techniques (Tech.). York, PA: MRG Labs.
[4] Williams, L., Wurzbach, R., & Alarcon, J. (2016). Integrating Grease Sampling and Analysis into Wind Turbine Maintenance Programs (Tech.). Bilbao Spain: LUBMAT.
[5] https://www.awea.org/wind-energy-facts-at-a-glance
[6] McKenna, P., Subramanian, M., Berwyn, B., Kusnetz, N., Jr., J. H., Lavelle, M., . . . Spiegel, J. E. (2017, June 01). U.S. Wind Energy Installations Surge: A New Turbine Rises Every 2.4 Hours. Retrieved from https://insideclimatenews.org/news/03052017/wind-power-rising-clean-energy-jobs
[7] Oil Analysis Handbook (3rd ed.). (2017). Chelmsford, MA: Spectro Scientific.