Technologies for monitoring machine vibration levels have been around for decades. The further development of such technologies, however, has been relatively slow.
With the rapid advancement of digital component technologies providing ever-new opportunities, time has caught up with conventional vibration monitoring methods.
HD ENV® is a new vibration enveloping technology taking advantage of these advances, using sophisticated digital algorithms to provide earlier warning of machine faults than conventional vibration monitoring technologies.
The rapid development of digital component technologies in recent years has enabled the first significant improvement of conventional vibration enveloping. Thanks to highly advanced and patented digital algorithms, HD ENV® is extremely sensitive to changes in vibration levels, making it possible to identify gear and bearing faults very early and closely monitor their continued development.
This fact provides the opportunity to optimize corrective and predictive maintenance scheduling, thus potentially driving maintenance profitability to new levels.
The Evolution of Vibration Monitoring Techniques
Historically, in the best-case scenario, gear and bearing damage detection using overall velocity readings may reveal severe damage in the very late stages, leaving limited time to plan maintenance. At best, an increasing velocity RMS trend could provide some guidance to avoid unplanned downtime.
Applying spectrum analysis based on velocity readings may reveal gear and bearing damages sooner, but it was still a rather crude process.
As vibration enveloping was eventually introduced, it became possible to distinguish the signals coming from gears or bearings, even if the transducer signal was dominated by the low-frequency content typically caused by unbalance forces.
However, while introducing vibration enveloping enabled somewhat earlier detection of mechanical problems, it was still hard to identify them in the incipient stages.
Condition monitoring aims to detect the gear and bearing signals at the earliest possible stage. Why is it so difficult to discover the early signs of fault development? This is quite a challenge for several reasons. Within the vibration community, describing the mechanical spalling process in stages is commonly accepted, from the first microscopic sign to a state of severe damage.
Generally, the vibration transducer is not sensitive to the elastic, low-energy waves generated at high-stress contact points in the initial stages of a developing bearing or gear fault. In addition, the signals originating from such defects are often drowned out and/or distorted by noise caused by other mechanical problems.
The HD ENV® Technology
The early fault detection capability of HD ENV is attributed to digital signal processing algorithms, which — combined with low-noise hardware and ICP-compatible accelerometers — extract and enhance relevant gear and bearing information with exceptional clarity from noisy industrial environments.
The ability to present disturbance-free vibration data in high-definition quality sets HD ENV apart from other technologies. Crystal clear spectrums and time signals, where the source of the signal is easily identified, provide a snapshot of machine condition, giving the maintenance department a heads-up on potential problems.
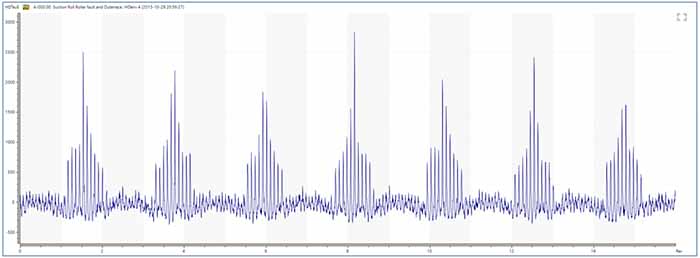
Roller damage in a suction roll (paper machine). The time signal very clearly shows a damaged rolling element entering and leaving the bearing load zone. The 0.45X modulation is the cage frequency.
Predefined filters in the software make it possible to detect and monitor damage development from a very early stage right up to when the time has come to replace or repair the bearing or gearbox. Digital enveloping is applied to ensure an optimal signal-to-noise ratio.
RPM is measured parallel to the vibration measurement with very high precision to handle varying rotational speeds. Using HD Order Tracking, the results are very distinct despite RPM variations up to +/- 50%.
The ‘Symptom enhancement’ function highlights repetitive signals — such as those caused by bearing and gear damage — by attenuating irrelevant, random signals and refining the pertinent portions. The result is clear and precise time signals and spectrums that can be used to identify faults even in complex machines.
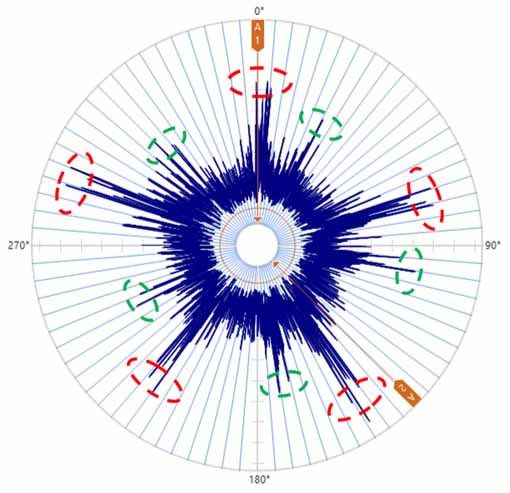
A circular plot showing gear teeth surface condition. For this eighty-teeth gear, the plot indicates surface damage/wear in the five red areas, with less damage/wear in the green ones. The gear ratio is exactly 5 (80:16). The condition measurement was carried out with HD ENV® and time synchronous averaging (TSA).
In addition to a Time signal HD and a Spectrum HD, each measurement produces a value called HD Real Peak, representing the true strongest signal caused by bearing or gear damage. HD Real Peak reacts early in the damage development process and is highly sensitive to incipient damages. Making equipment condition trends easy to understand and to work with, HD Real Peak is the primary parameter for trending and alert management.
Maximized Forewarning Times
The main benefit of using HD ENV is the increased forewarning time for impact-related damages such as those originating from gears and rolling element bearings. An added benefit is the ability to ‘see’ gear and bearing-related signals in complex machines.
The method’s accuracy makes it possible to identify the signal of interest in an otherwise noisy environment with plenty of signal sources. Standard vibration enveloping may fail in these situations, while HD ENV provides meaningful results at the earliest possible stage.