Additives can enhance, suppress, or add new properties to oils. Defoamants, dispersants, and detergents are no exceptions. This trio of additives can be found in most finished lubricants, albeit in varying ratios.
Let’s discuss the main differences among these three, why each is so important, and ways to confirm their presence.
What’s the Difference?
While they are all additives (which begin with the letter D), their functions are distinctively different. They all work to protect the oil from various types of contaminants.
For instance, defoamants reduce the air bubbles in the oil. At the same time, detergents keep the metal surfaces clean, and dispersants encapsulate the contaminants so they are suspended in the lubricant.1 This is illustrated in Figure 1.
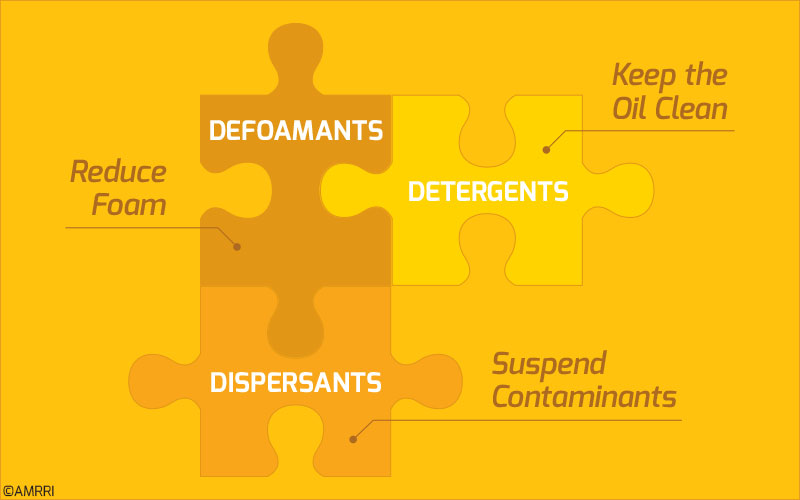
Figure 1: Defoamants, detergents and dispersants explained.
From our last article on Lubricant Additives – A Comprehensive Guide, here are some detailed descriptions of how each of these additives functions.
Defoamants
When foam forms in the lubricant, tiny air bubbles become trapped either at the surface or on the inside (called inner foam). Defoamants work by adsorbing on the foam bubble and affecting the bubble surface tension. This causes coalescence and breaks the bubble on the lubricant’s surface1.
For the foam that forms at the surface, called surface foam, defoamants with a lower surface tension are used. They are usually not soluble in base oil and must be finely dispersed to be sufficiently stable even after long-term storage or use.
On the other hand, inner foam, which is finely dispersed air bubbles in the lubricant, can form stable dispersions. Common defoamants are designed to control surface foam but stabilize inner foam2.
Dispersants
On the other hand, dispersants are also polar, and they keep contaminants and insoluble oil components suspended in the lubricant. They minimize particle agglomeration, which in turn maintains the oil’s viscosity (compared to particle coalescing, which leads to thickening). Unlike detergents, dispersants are considered ashless. They typically work at low operating temperatures.
Detergents
Detergents are polar molecules that remove substances from the metal surface, similar to a cleaning action. However, some detergents also provide antioxidant properties. The nature of a detergent is essential, as metal-containing detergents produce ash (typically calcium, lithium, potassium, and sodium)1.
Are Defoamants Necessary?
Defoamants, also called antifoam additives, are found in many oils. Most oils need to keep foam levels to a minimum, and it is very easy for foam to form in lube systems due to their design and flow throughout the equipment.
When foam enters the oil, it can affect its ability to provide adequate surface lubrication. This can lead to wear occurring at the surface level, damaging the equipment.
Many oils require defoamants to provide various functions and in differing ratios depending on their application. In automatic transmission fluids (ATFs), defoamants are usually needed in concentrations of 50-400ppm to prevent excessive foaming and air entrainment3. On the other hand, for manual transmission fluids and axle lubricants, defoamants are required in slightly lower concentrations, between 50 and 300 ppm.
However, OEMs must verify these concentrations. If the concentration of defoamants is too high, this can actually increase foaming. Additionally, defoamants must be properly balanced with the other additive packages to ensure they do not negatively counteract another additive.
There are two main types of defoamants: silicone defoamers and silicone-free defoamers. Silicone defoamers are considered the most efficient defoamants, especially at low concentrations of around 1%. These defoamants are typically pre-dissolved in aromatic solvents to provide a stable dispersion.
However, there are two significant disadvantages associated with silicone defoamers. Due to their insolubility, they can easily transition out of the oil and have a powerful affinity to polar metal surfaces.
On the other hand, silicone-free defoamers are another alternative, especially for applications that require silicone-free lubricants. Such applications include metal-working fluids and hydraulics, which are used close to silicone-free ones, and even those involved in applying paints or lacquers to these pieces.
Some silicone-free defoamers include poly(ethylene glycol)s (PEG), polyethers, polymethacrylates, and organic copolymers. Tributylphosphate is also another option for defoamers4.
Why Are Dispersants Important?
Quite often, detergents and dispersants are grouped together mainly because their functions can complement each other. As noted above, the significant difference is that dispersants are ashless, while detergents are more metal-containing compounds.
However, some ashless dispersants also offer “cleaning” properties, so the two are not mutually exclusive.
A large oleophilic hydrocarbon tail and a polar hydrophilic head group can categorize detergents and dispersants. Typically, the tail solubilizes in the base fluid while the head is attracted to the contaminants in the lubricant.
Dispersant molecules envelop the solid contaminants to form micelles, and the non-polar tails prevent the adhesion of these particles onto the metal surfaces so that they agglomerate into larger particles and appear suspended.
Ashless dispersants are, by definition, those that do not contain metal and are typically derived from hydrocarbon polymers, with the most popular being polybutenes (PIBs).
For example, dispersants are typically required in concentrations of 2-6% in ATFs and are used to maintain cleanliness, disperse sludge, and reduce friction and wear3. These values in manual transmission fluids and axle lubricants vary from 1-4%.
Do Detergents Really Clean?
Traditionally, detergents were given their name as it was assumed that they provided cleaning properties to the oil, similar to laundry detergents. However, these metal-containing compounds also provide an alkaline reserve used to neutralize acidic combustion and oxidation by-products.
Due to their nature, these compounds disperse particulate matter, such as abrasive wear and soot particles, rather than removing them (in a cleaning action). There are four main types of detergents: phenates, salicylates, thiophosphate, and sulfonates4.
Calcium phenates are the most common type of phenate. They are formed by synthesizing alkylated phenols with elemental sulphur or sulphur chloride, followed by neutralization with metal oxides or hydroxides. These calcium phenates have good dispersant properties and possess a greater acid-neutralization potential.
Salicylates have additional antioxidant properties and a proven efficacy in diesel engine oil formulations. They are prepared through the carboxylation of alkylated phenols with subsequent metathesis into divalent metal salts. These products are then overbased with excess metal carbonate to form highly basic detergents.
Thiophosphonates are rarely used today as they are an overbased product.
Sulfonates generally have excellent anticorrosion properties. The neutral (or over-based) sulfonates have excellent detergent and neutralization potential. These neutral sulfonates are typically formed with colloidally dispersed metal oxides or hydroxides.
Calcium sulfonates are relatively cheap and have good performance. On the other hand, magnesium sulfonates exhibit excellent anticorrosion properties but can form hard ash deposits after thermal degradation, leading to bore polishing in engines. Barium sulfonates are not used due to their toxic properties.
Detergents in ATFs are used in concentrations of 0.1-1.0% for cleanliness, friction, corrosion inhibition, and reduction of wear3. However, these values are a bit higher in manual transmission fluids, at 0.0 – 3.0%. On the other hand, no detergents are required for axle lubricants!
What Happens When These Additives Are Used Up?
For the three additives we spoke about earlier, each of them is sacrificial in one way or another.
Defoamants get used up when they are called upon to reduce the foam in the oil. On the other hand, detergents and dispersants use their characteristics to suspend contaminants in the oil.
In all of these scenarios, each of these additives can be considered to become depleted over time. While performing their functions, they will undergo reactions that reduce their capability to perform them more than once.
Hence, it can be concluded that these additives become depleted over time even though they may not have physically left the oil but now exist in a different form.
The air release property of the oil is affected by the loss of defoamants. This value will see a significant rise, indicating that it takes longer for air to be released from the oil. As such, air remains in the oil in either a free, dissolved, entrained, or foam state.
Consequently, this impacts the ability of the oil to lubricate the components properly and can even result in microdieseling and increased oil temperatures in the sump.
On the other hand, as the detergents and dispersants are reduced, the capacity of the oil to hold contaminants also decreases.
Therefore, one will begin noticing that deposits may start forming on the equipment’s insides, leading to valves sticking (especially in hydraulic systems) or a general increase in the system’s temperature as these deposits can trap heat.
With the introduction of an increased temperature, the oil can begin oxidizing, leading to more deposits being formed and possibly even varnish.
Essentially, these additives are essential to the health of the oil in your system. The detergents and dispersants can help to keep your system clean (free from contaminants such as soot).
The defoamants can even reduce the risk of wear, increased temperatures to the lube system, the potential to form varnish, or the possibility of succumbing to microdieseling.
References
1 Bruce, R. W. (2012). Handbook of Lubrication and Tribology – Volume II Theory and Design – Second Edition. Boca Raton: CRC Press, Taylor & Francis.
2 Mang, P., & Dresel, D. (2007). Lubricants and Lubrication – Second Edition. Weinheim: WILEY-VCH Verlag GmbH & Co KGaA.
4 Mang, P.-I., Bobzin, P.-I., & Bartels, D.-I. (2011). Industrial Tribology Tribosystems, Friction, Wear and Surface Engineering, Lubrication. Weinheim: WILEY-VCH Verlag & Co KGaA.
3 Mortier, D. M., Fox, P. F., & Orszulik, D. T. (2010). Chemistry and Technology of Lubricants – Third Edition. Dordrecht Heidelberg: Springer.