It is often stated that viscosity is the most important property of a lubricant, and with good reason. Film thickness—the separation between moving machine surfaces—is primarily dictated by the lubricant’s viscosity under operating loads, speeds, and temperatures.
For this reason, viscosity is one of the first properties we measure when evaluating in-service oil samples. Unfortunately, labs may also be measuring the wrong type of viscosity!
Absolute vs Kinematic Viscosity: What’s the Difference?
In fluid dynamics, we need to consider two types of viscosity. The first is known as kinematic viscosity and measures how a fluid flows under the force of gravity.
Consider pouring two oils, the first an ISO VG 32 hydraulic fluid and the second an ISO VG 680 worm gear oil. At the same (ambient) temperature, the hydraulic fluid will flow faster since it has a lower resistance to flow and shear due to gravity; in other words, it has a lower kinematic viscosity.
By contrast, dynamic viscosity represents a fluid’s internal resistance to flow and shear. Imagine inserting a spoon or metal rod into two samples of the same ISO VG 32 and ISO VG 680 oils, again held at the same temperature. Which sample of oil would be more challenging to stir?
The ISO VG 680 would be harder to stir since it has a higher (internal) resistance to flow and shear, meaning it has a higher dynamic or absolute viscosity.
Kinematic and Absolute (Dynamic) viscosity are related by the specific gravity of the fluid as follows:
While the equation shown helps convert kinematic to dynamic viscosity, it strictly only applies to Newtonian fluids. A Newtonian fluid is one whose viscosity does not change with the shear rate. Examples of Newtonian fluids include water and air.
However, in the real world, most fluids tend toward some form of non-Newtonian behavior. Unlike water or air, non-Newtonian fluids exhibit an unusual property in that their viscosity will change with applied shear force.
For non-Newtonian fluids, the change of viscosity with shear rate can cause either an increase in viscosity (shear-thickening) or, more commonly, a decrease in viscosity (shear thinning) (Figure 1).
Everyday examples of non-Newtonian fluids include yogurt or ketchup, which tend to thin with agitation or stirring (increased shear rate), or a slurry of corn starch and water or quicksand, which becomes more viscous with increased shearing action (safety tip: when trying to escape from quicksand, move very slowly towards firmer ground; sudden rapid movement will cause the quicksand to (shear) thicken, increasing viscous drag!).
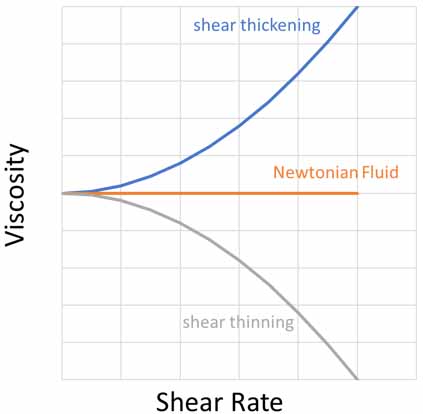
Figure 1: Newtonian vs non-Newtonian fluid mechanics
All commercial fluid analysis labs default to measuring kinematic viscosity as a trending tool. There are several reasons for this. The first is purely historical in nature. When commercial oil analysis emerged in the late 1940s, practitioners looked at simple, existing test methods to evaluate in-service oil samples.
Kinematic viscosity had long been used as a QA and QC tool in petroleum refining, so it was a natural choice when developing test methods for in-service oil analysis.
Because of its use in refining, kinematic viscosity was also chosen as the standard for the ISO 3448 industrial lubricants grading system.
The ISO viscosity grades are defined as an oil’s kinematic viscosity in cSt, measured at 40 °C. For an oil to qualify as a specific viscosity grade, the viscosity of the new oil must fall within a ±10% range from the designated grade (Figure 2).
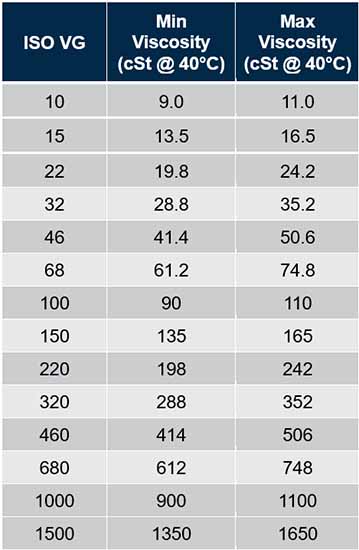
Figure 2: Industrial Oil Viscosity Grades per ISO 3448
However, simplicity may be the most common reason for adopting kinematic viscosity for in-service oil analysis. Even before the advent of automated kinematic viscometers, measuring the time it takes for an oil to flow under gravity was a quick and simple test procedure that required nothing more than basic lab equipment.
Which Is More Appropriate: Kinematic or Dynamic Viscosity?
But is kinematic viscosity the correct measurement? Is film strength dependent on how quickly an oil flows under gravity (kinematic viscosity) or how much resistance (force) the oil provides when a metal rod is rotated through the fluid (dynamic viscosity)?
While it would be fair to say that oil distribution, particularly in wet sump splash lubricated systems, does depend on kinematic viscosity, it would appear that dynamic viscosity is more closely related to what actually happens to oil under operating loads, speeds, temperatures, and shearing from fluid and mechanical friction.
In many cases, measuring the kinematic viscosity of an industrial lubricant is an adequate proxy for dynamic viscosity since most new, clean oils exhibit properties that are close to Newtonian in nature.
However, as an oil ages, becomes contaminated, or is formulated with higher additive concentrations, it will diverge from Newtonian behavior, meaning what’s happening at the contact zones in a bearing or gear may not bear any resemblance to how the oil flows at 40 °C in a controlled lab environment.
The two biggest issues that could cause significant non-Newtonian behavior in industrial oils are contamination with either water or air.
Common logic would suggest that mixing a low-viscosity fluid—water—which by definition has a kinematic viscosity of 1 cSt—with an oil would lower the overall kinematic viscosity, but not so!
When an oil mixes with water and becomes either an emulsion or an inverted emulsion, the kinematic viscosity goes up! This is the characteristic behavior of a non-Newtonian fluid.
Don’t believe me? Try making salad dressing by mixing a low-viscosity fluid (vinegar) with a higher-viscosity (olive) oil and agitating the two. What happens to the pourability of the salad dressing when the vinegar mixes with the oil?
Particularly if you add a binding (emulsifying) agent such as a few drops of milk, the mixture will form a tight emulsion that will not separate and will flow at a much slower rate due to the higher kinematic viscosity of the (non-Newtonian) mixture compared to the two constituent elements.
A similar effect can occur in lubricating oils if an oil forms a tight emulsion with water. While the kinematic viscosity may increase, an oil-water emulsion will not exhibit anywhere close to the same film strength, which could lead to boundary lubrication.
By measuring and reporting the kinematic viscosity of an in-service oil with water contamination, we may get a false sense of security if the viscosity is unchanged or has slightly increased.
However, things may be very different in the contact zone. Similarly, water contamination prevents oil from flowing to where it’s needed – for example, inside a pump or gearbox with oil galleries, slingers, flingers, or paddles.
Likewise, air contamination. Blending air (a gas) into an oil can also reduce fluidity. Think shaving foam or whipped cream. If we beat enough air into a fluid, we can cause a significant increase in the oil’s kinematic viscosity.
But if aerated oil enters the load zone inside our machine, there will almost certainly be a loss of oil film or cavitation due to a reduced dynamic viscosity.
What About Engines?
In the automotive world, kinematic and dynamic viscosity measurements are more routine. The SAE J300 standard, which determines an engine oil’s SAE grade as SAE 16, 20, 30, 40, 50, or 60, is a measure of the oil’s kinematic viscosity at 100°C.
While this is well known by most car owners, what is less commonly understood about the SAEJ300 standard is that in addition to kinematic viscosity at 100°C, qualifying an oil as a specific SAE grade also requires that the oil passes a high temperature, high shear stress test under ASTM D4683. This measurement, reported in centipoise (cP), is a dynamic viscosity measurement (Figure 3).
In multigrade engine and automotive gear oils, an oil must qualify not just at (high) engine operating temperatures and shear stress but also demonstrate appropriate pumpability at very low temperatures. This is the basis for an oil’s “W” or “winter” grade.
For engine oil, the pumpability is measured using a cold cranking simulator or rotary viscometer as dynamic viscosity in centipoise (cP), which is the basis for the SAE J300 winter grades such as 0W, 5W, 10W, 15W, 20W or 25W (Figure 3).
Many multigrade engine oils with a large “stretch” (difference between winter and operating grade) will include viscosity index (VI) improvers.
These large chain polymers artificially increase viscosity at higher temperatures due to the change in polymeric structure at low temperatures compared to high temperatures. However, too much VI improver may increase the kinematic viscosity but may not necessarily increase film thickness (dynamic viscosity).
This is related to an effect known as temporary shear thinning. While a long-chain polymer may influence fluidity (kinematic viscosity) at high rates of speed, the long-chain polymer can align in the direction of shear force, effectively lowering the dynamic viscosity, which will impact film thickness.
For this reason, increased scrutiny has been raised by oil suppliers and additive manufacturers of late to ensure adequate film thickness with the latest SAE J300 viscosity grades developed to reduce fluid friction in support of better fuel economy.
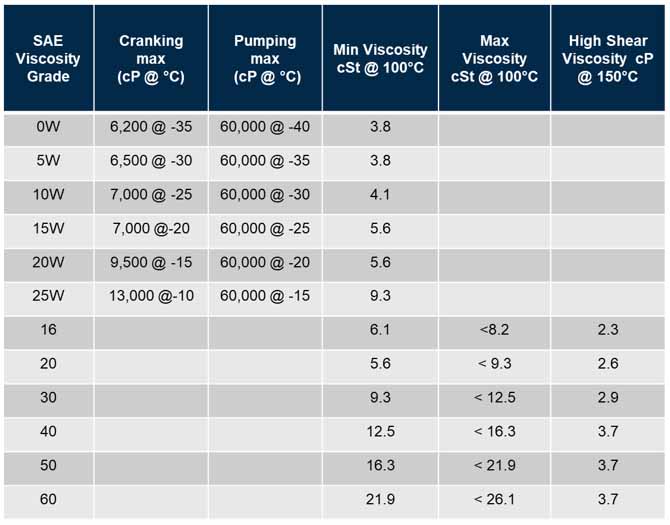
Figure 3: SAE J300 Engine Oil Viscosity Grades
While measuring kinematic viscosity for routine trending of in-service oil samples is unlikely to change any time soon, don’t take a tiny change in the reported kinematic viscosity lightly. Particularly if the oil is severely degraded, aerated, heavily contaminated with water, or contains a high concentration of VI improvers.
Under these circumstances, the dynamic viscosity and, by inference, the film thickness may be very different at the load zone of the bearing or gear contacts.