It is common to hear about deposits or varnish in turbine oils, but can other oils also suffer from varnish? The short answer is yes. Once an oil (regardless of its application or type) has been exposed to thermally stressful conditions, contaminants, and severe operating environments, it will degrade, possibly producing deposits.
Hydraulic systems are susceptible to deposit formation due to the prevalent use of close-tolerance components and requirements for ultra-clean operating fluids.
Today, like many other industrial lube systems, hydraulic fluids are subjected to greater amounts of stress than in the past. This is the case across many industries, from injection molding and steel mills to off-road and construction equipment. To reduce cost, weight, and space, reservoirs are shrinking.
A recent survey of plastic injection molding machines revealed that a major manufacturer had reduced the oil reservoir volume in the same machine by 40% over the last ten years.
To improve performance, valves have tighter clearances while system pressures are increasing. Engineering hydraulic systems with increased power outputs and productivity also require higher speeds and shorter cycle times.
OEMs are also designing systems with reduced noise levels and lower carbon footprints, which require hydraulic oils to have great efficiency. These evolutionary changes in hydraulic system design place further demands on hydraulic oils.
End-users also share some responsibility for the increased stress on hydraulic oils. Their attention to leak reduction inadvertently results in fewer additions of new oil top-offs. Also, many hydraulic machines are operated at a higher rate than originally designed.
The confluence of system design changes and more severe operating conditions is more oxidative stress and less recovery time for the oil. Oxidation is now the most common form of fluid failure.
Lubricant manufacturers have responded to these stressful conditions by using more highly refined base oils with lower levels of wax, sulfur, and aromatics. Antiwear additives are also being upgraded.
The dominant antiwear additive technology in hydraulic oils remains zinc dialkyldithiophosphate (ZDDP). New formulations, however, are evolving to higher performing, more environmentally friendly, ashless antiwear technologies.
Since hydraulic fluids can directly impact the energy efficiency of the overall hydraulic system, formulations are being designed to provide improved energy efficiency. This is accomplished through improved viscometrics.
Shear-stable, high Viscosity Index (VI) hydraulic oils have shown energy efficiency improvements across multiple applications. Studies have shown that these advanced formulations may reduce energy by up to 10% in some applications. Shear-stable VI improvers are typically polymethacrylate polymers and can make up to 15% of the overall hydraulic oil formulation.
Finally, more antioxidants are used in hydraulic oils, producing a more oxidatively robust product that is less prone to deposits. Even with these changes, however, we still see hydraulic oil varnish occurring more frequently than in the past.
What Is Hydraulic Oil Varnish?
Varnish is a thin deposit in a lubrication system that is difficult to wipe away and comprises mainly organic residue. Its chemical composition is widely varied and classified by chemistry and degradation mechanisms. The terms varnish and sludge are often used interchangeably, but they mean different things.
Sludge can be considered easy to wipe, gooey in nature, and usually contains moisture. Conversely, varnish has a more cured, shiny appearance and is not easy to wipe. These definitions help users identify whether they have sludge or varnish in their system.
Varnish is primarily caused by the continual process of oxidation, which is accelerated by temperature, various metallic components, and gaseous catalysts.
Oxidation was originally defined as a reaction involving the combination with oxygen. However, its definition has now been expanded to include any reaction in which electrons are transferred from a molecule.
Oxidation is the predominant reaction a lubricant undergoes in service, accounting for significant lubricant performance problems.
Contaminants will also increase the rate of reaction. In hydraulic oils, there are three different types of contamination: dirt contamination (silt, wear metals), water, and air.
Oxidation is the major source of viscosity increase, varnish formation, sludge and sediment formation, additive depletion, base oil breakdown, filter plugging, loss of foam resistance, loss of demulsibility, acid number increase, rust, and corrosion. Deposits, however, are most often the link between oil degradation and machine performance.
Varnish can cause a wide range of operational challenges in lube systems. These can include; increased wear rates experienced due to the “sandpaper” effect. Heat exchanger efficiency declines as varnish creates an insulating layer on the tubes.
Oil flow is subsequently impaired, potentially causing starvation issues. Filters may blind off quickly as they become slimed. As such, oil life is shortened due to the reactive nature of these deposits.
Servo valves are the most sensitive component impacted by varnish. Often the oil flow to these components is intermittent, increasing the likelihood of deposits forming in these components. A leading cause of valve hysteresis and chatter due to the increased friction required to move varnished components.
Some of the operational impacts of a hydraulic system are:
- Valve lock resulting in high levels of static friction
- Loss of clamp speed or cycle time impacting production
- Reduced repeatability and precision impacting scrap rate
- Increased set-up and interchangeability times due to additional maintenance and variance adjustments impacting production.
An increased amount of energy required to move these valves results in major energy losses for the overall system. Additionally, due to the loss of hydraulic control of the system, they are often replaced prematurely, costing more maintenance dollars. Since the issue causing the varnish was not initially solved, then the newly replaced valves will also become coated with varnish and can fail more rapidly.
The Critical Role of Condition Monitoring
Failure Modes and Effects Analysis (FMEA) has been a dominant part of reliability programs since its conceptualization in the 1940s. FMEA provides a systematic method of evaluating failure modes, their causes, and their effects. This should be the basis of any oil analysis program.
Why perform an oil analysis test if it does not detect a lubricant’s failure mode? Conversely, if one knows the primary failure modes, shouldn’t your condition monitoring program be set up to detect this failure? Unfortunately, many hydraulic oil analysis programs are not aligned with the fluid’s primary failure mode, resulting in unexpected problems.
Case Study: “But my oil analysis reports look good!”
A plastic injection molding facility started having machine performance problems that increased their scrap rate and reduced productivity. The maintenance manager increased their oil sample test slate and frequency to ensure it wasn’t an oil-related issue. Most of the machines came back in acceptable condition. Here’s an example report from Machine 15, which uses AW46 hydraulic oil in their presses:
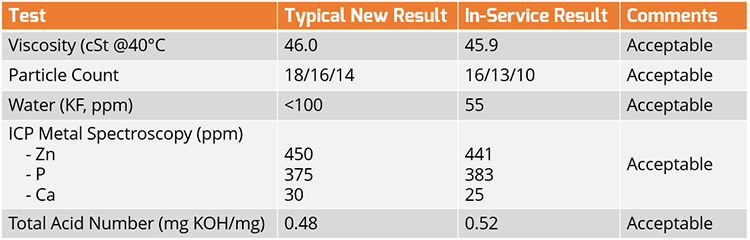
Table 1: Oil Analysis Results from Machine 15
This “acceptable” oil analysis report gave the maintenance manager a false sense of security. During the next maintenance activity, the maintenance manager noticed varnish deposits on his valve components and in the hydraulic oil reservoir. This prompted further analysis.
A voltammetry (RULER) test was used to measure the antioxidant health in the fluid, as seen in Figure 1.
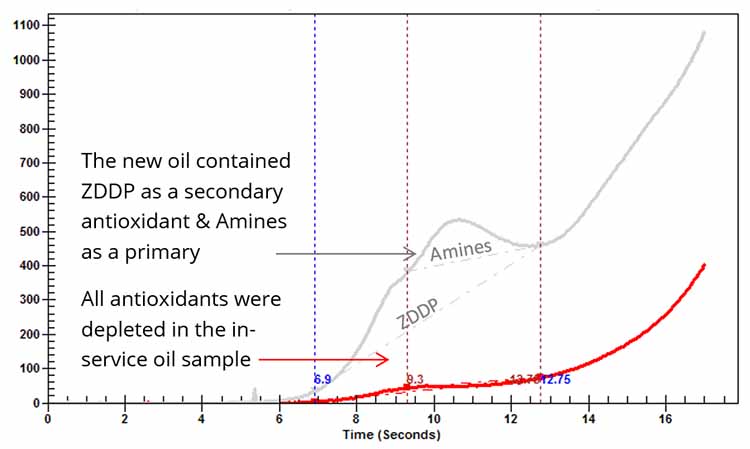
Figure 1: A RULER Voltammogram determined that the in-service oil had no remaining antioxidants.
Next, the maintenance manager performed a Membrane Patch Colorimetry (ASTM D7843) test on the in-service hydraulic oil. The result was a DE of 61, determined to be in the critical range.
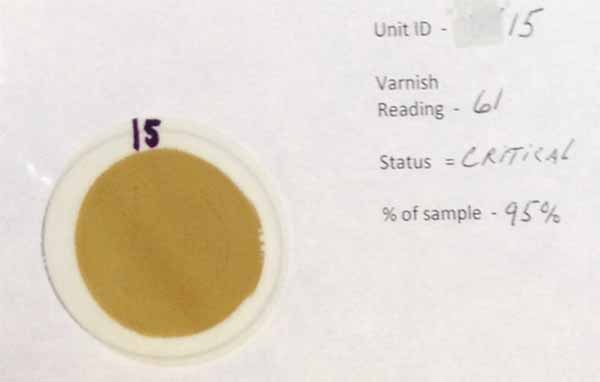
Figure 2: The MPC patch is shown above, with a critical rating of 61 indicating a high potential for varnish deposits.
The additional analysis revealed the source of the plastic injection molding machine performance problems – oxidation and varnish development.
What can we learn from this case study?
The maintenance manager thought that he was testing for oxidation and varnish tendencies. He mistakenly thought that elemental spectroscopy would indicate the health of his ZDDP additive package and that acid number and viscosity would identify oxidation. Here’s why those tests were ineffective at identifying oxidation and deposit formation:
Elemental spectroscopy is a powerful oil analysis tool and is effective for identifying metallic additive elements. For example, it can identify the presence of zinc to determine if the formulation is ashless. However, this test does not measure additive health. The ZDDP molecule may no longer be intact and effective. It may have degraded to form sulfates and phosphates. However, the zinc and phosphorus elements will remain in solution until they eventually settle out as sludge.
Acid Number has been integral to hydraulic oil analysis for decades. The final component in an oxidation reaction is acid, so this test has shown value in measuring the results of oxidation. However, because Group II and III base oils have lower solubility, the degradation products may not remain in the oil long enough to be converted to an acidic molecule. Also, acids will only start to develop in the oil once all the antioxidants have been depleted, which is often too late.
Viscosity increases may be due to oxidation; however, by the time a noticeable change has occurred, many other problems have already started.
Appropriate tests for detecting oxidation and its effects on hydraulic oils
To adequately predict hydraulic oil failure due to oxidation, the following tests are recommended:
- Voltammetry, RULER (ASTM D6971) – This test identifies the antioxidant health of both primary and secondary antioxidants used in hydraulic oils.
- Molecular Spectroscopy using Fourier Transform Infrared (FTIR) – Several ASTM methods can be of value in monitoring hydraulic oils.
- ASTM D7414 measures oxidation
- ASTM D 7412 measures antiwear additives
- An ASTM draft method is currently drafted to measure acid number
- FTIR is also effective at measuring phenolic antioxidants
- Membrane Patch Colorimetry (ASTM D7843) – This test method effectively determines a hydraulic oil’s propensity to form varnish. Its results are reported on the CIE LAB ΔE scale, as can be seen below in Fig. 3
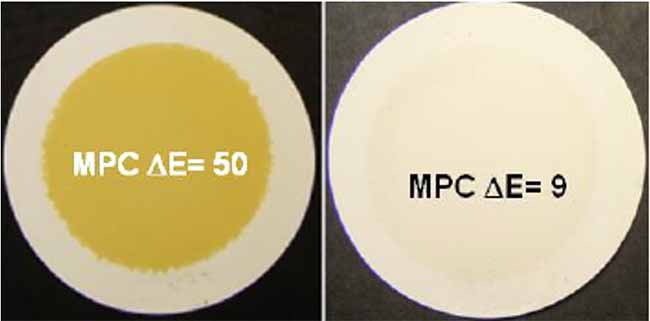
Figure 3: Example Patches and values from the Membrane Patch Colorimetry (MPC) test. A value of 50 would be considered critical, warranting immediate action. A result of 9 would be considered acceptable. Typically, anything over an MPC of 30 warrants immediate attention.
- Colorimetric Analysis – A revised version of the MPC test, colorimetric analysis is based on research by Dr. Sasaki and Prof. Honda. In addition to varnish potential, it provides further insight into the mode and rate of degradation.
- Ultracentrifuge – Extracting and qualitatively measuring the amount of degradation products through high centrifugal forces has successfully predicted the onset of varnish.
- Air release – measures the fluid’s ability to dissipate air bubbles which can be of value, especially in the areas where hydraulic oil is required to do the work of moving a valve or lifting a bearing shaft. The deterioration of air release values is linked to both hydraulic oil degradation and contamination.
Solving the Deposit Challenge for Hydraulic Oils
One of the easiest and most cost-effective methods of eliminating deposits from hydraulic oils is using a solubility enhancer. Solubility enhancers should be considered under the following conditions:
- The solution must be added when the machine is in operation.
- It must be compatible with the in-service oil and other system materials.
- It cannot affect the oil’s interaction with contaminants, inhibit corrosion, or antiwear performance. Therefore, surface active chemistries such as dispersants or detergents should never be used.
- It must also work under intense conditions without breaking down.
- Does not give in to oxidative stress.
- Using the solubility enhancer eliminates the need to install any other mitigation system.
- Works under extreme oxidative conditions and does not produce deposits when burnt.
The Fluitec team developed Solvancer® technology (patent pending) after the exhaustive categorization of the various deposit chemistries in hydraulic systems. Three essential properties were studied during this categorization; polarity, hydrogen bonding, and dispersive forces.
Solvancer has been optimized to consider these three characteristics to ensure that lube deposits are quickly dissolved into the lubricant. It is typically added at a rate of 3-5% to an in-service lubricant and has no adverse effects on the performance of the fluid. It goes to work immediately to dissolve deposits and prevent further varnish from forming.
The case study below shows the immediate and long-term impact of adding Solvancer to an in-service oil. The graph also shows the results from a 6-week accelerated oxidation test (120°C) without and with Solvancer.
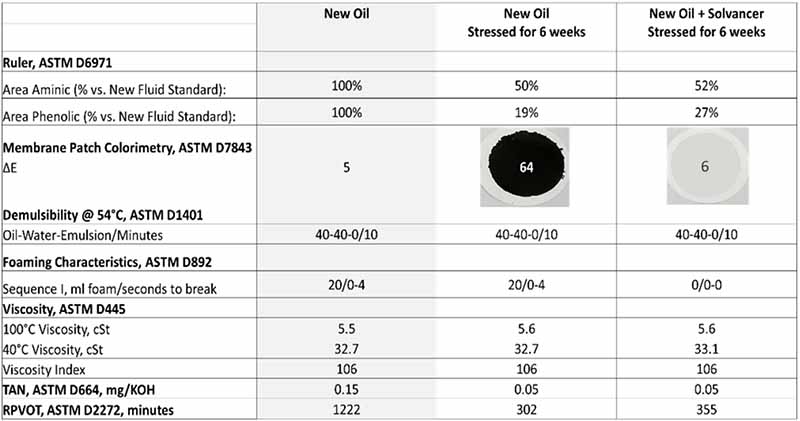
Figure 4: Results after six weeks of TOPP test without and with Solvancer.
Hydraulic oils are subjected to increased thermal and mechanical stress in modern hydraulic systems causing system deposits and fluid failure. Hydraulic oil formulations are being tweaked to accommodate this more stressful environment; however, problems persist.
The leading reason hydraulic oil users experience performance problems with their fluid is inadequate oil analysis testing. Most condition monitoring programs do not measure oil degradation and deposit formation. By upgrading your oil analysis package to include monitoring your antioxidant system’s health and deposits’ formation, many hydraulic oil degradation problems can be avoided.
A deposit-free hydraulic oil can exist with a solubility enhancer such as Solvancer®, which will not affect the hydraulic oil’s performance properties. The RULER and MPC tests can effectively monitor the health of the lubricant to amply warn operators of the presence of deposits in hydraulic systems. These can be coupled with FTIR, Air release, and elemental spectroscopy to provide a full suite of tests.
Adapted from the paper, “Managing hydraulic oil deposits by using novel solubility enhancing technology” written by; Jo Ameye, Greg Livingstone & Cristian Soto of Fluitec, presented at OilDoc 2023.