Degradation of the lubricant circulating through your system can impact equipment performance, reliability, and lifespan. When an oil degrades, it loses its ability to properly lubricate, meaning friction increases – accelerating wear and tear on the components. This wear and tear in the metals leads to the failure of the equipment’s bearings, gears, and other moving parts.
Degraded oil becomes more and more susceptible to contamination of dirt, soot, fuel, and water and requires more frequent changes – increasing costs and downtime. Going undetected can cause severe failures and shut down operations quickly.
What Causes Oil to Degrade?
Oxidation and other contaminants can cause the formation of acidic degradation compounds (carboxylic acids, ketones, and esters) that corrode metal surfaces, leading to pitting and the damage of critical components. In addition, nitration (common in high-temperature operating environments) further accelerates the formation of nitric acid and damage to components.
Most often found in natural gas engines, nitration results from a reaction of nitrogen oxides (NOx) from the air with the oil, leading to acid formation, and most often is a result of combustion byproducts reacting with the lubricant.
Nitric acid formation can cause corrosion of engine parts as well as an increase in the oil’s viscosity, making it less effective at reducing friction. An increase in nitration compounds in high-temperature operating conditions can accelerate the breakdown of the oil, leading to a decrease in the oil’s ability to lubricate and do its job effectively.
Determining Oil Degradation
Oxidized oil loses its ability to dissipate heat, leading to increased operating temperatures and overheating. When degraded, oil becomes more susceptible to contamination, which causes the buildup of particles and clogging filters, reduces oil flow, and causes pressure drops that put strain on the system to work harder.
If you’re experiencing these issues, your oil could be degrading. To make matters worse, overheating can lead to faster oxidation of the fluid (Arrhenius Rate Rule – the rate of oxidation doubles for every 10°C).
Oxidized oil loses its ability to dissipate heat, leading to overheating and pressure drops.
Performing oil analysis regularly can identify rising oxidation and nitration levels in your engine oil, allowing you to take corrective action before significant damage occurs.
Using FTIR (ASTM E2412) to Measure Oxidation and Nitration
Fourier Transform Infra-Red Spectroscopy (FTIR) is a very powerful analytical testing technique for quantifying many parameters of used fluids for condition monitoring purposes. During testing, infrared light is passed through the oil sample, measuring which wavelengths are absorbed by the molecules, allowing identification of specific function groups and chemical compounds and properties. (Figure 1).
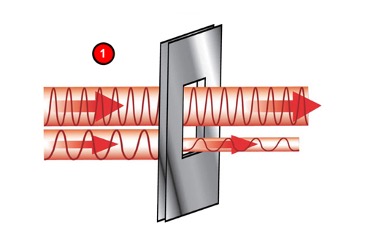
Figure 1
At POLARIS Laboratories®, we use FTIR, ASTM E2412, which monitors contaminants like water and soot. Oxidation, nitration, and sulfation of base stocks are observed as evidence of degradation. The objective of ASTM E2412 is to diagnose the operational condition of the machine based on fault conditions observed in the oil.
If you are not performing FTIR analysis, you really should. It is a low-cost, simple test that sheds a lot of “light” on the condition of the fluid that cannot be done easily with other tests.
Oxidation testing performed by FTIR measures the breakdown of a lubricant due to age and operating conditions and is reported in abs/cm (absorbance units per centimeter). By observing specific absorption, FTIR testing detects the presence of carbonyl groups (C=O), such as ketones, esters, and carboxylic acids, that result from oxidation in the oil.
Nitration testing is also performed using FTIR (ASTM E2412 method), which indicates the presence of nitric acid, which speeds up oxidation. Nitrates exhibit peaks in the infrared spectrum, allowing FTIR to identify their presence in the oil.
Too much disparity between oxidation and nitration can point to air-to-fuel ratio problems.
Too much disparity between oxidation and nitration can point to air-to-fuel ratio problems. As oxidation and nitration increase, so can acid number and viscosity, while base number can begin to decrease.
In the results example here (Figure 2), high levels of oxidation and nitration reported on this sample can be correlated to oil degradation, resulting in high levels of wear metals and concerns related to the oil’s viscosity. Maintenance actions to diagnose further and address the root cause are recommended in the comments.
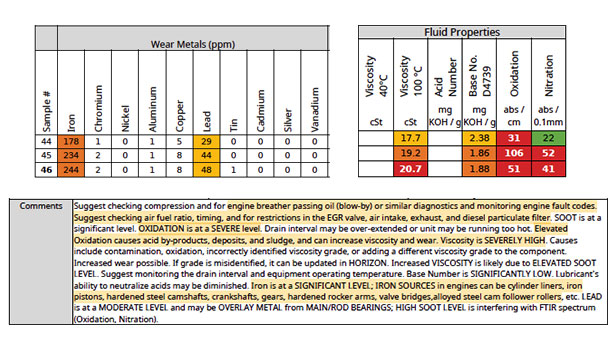
Figure 2
In this graph (Figure 3) of FTIR results, you can see the increases in oxidation and nitration results indicated by the FTIR testing compared to the new lubricant values.
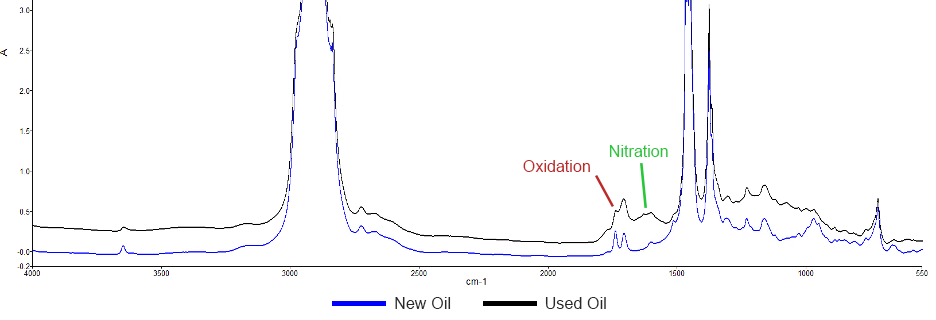
Figure 3
Oxidation/Nitration Results Reported
When analyzing and reporting on the test results, the starting values of the new lubricant (product and grade) are considered. It’s good to note that the starting values of conventional lubricants will differ from synthetic. Customers can send in a baseline or new lube reference sample, which will be included in reports for reference and trending history comparisons. When the data analysts review test results, they look for deviations from the baseline lubricant values.
Based on the results, maintenance actions are recommended to address the root cause of lubricant oxidation and nitration.
Importance of Oxidation/Nitration Testing
POLARIS Laboratories® recommends oxidation/nitration for industrial and mobile test packages as it’s imperative to protect equipment that performs under high temperatures or combustion environments and prolongs machine life.
Detecting wear-causing oil degradation early can avoid unplanned failures and downtime.
This includes industrial machinery like gasoline, diesel, natural gas engines, turbine engines in power plants, gearboxes, transmissions, high-pressure hydraulic systems, and reciprocating compressors. Detecting wear-causing oil degradation due to oxidation/nitration early can avoid unplanned failures and keep operations running without interruption.