Lubricants are the lifeblood of machines. Like a blood test, lubricant analysis can provide early warnings of impending failures, far in advance, before it is too late to take timely action. But not all oil samples can give such alerts completely!
Only representative samples lead to correct conclusions regarding machine performance and lubricant health. Drawing a representative sample is the oil analysis program’s cornerstone and a fundamental step to achieving its related goals.
Getting a representative oil sample is about more than just the right sampling location, the right sampling method, and the right sampling tools. It is about the right identification of the sample as well!
Many laboratories and consultancy firms specializing in lubrication and reliability have published articles about sampling locations and methods. But in this article, I would like to focus on how the proper labeling of an oil sample is as important as choosing the best sampling location and following the most accurate sampling methods.
Equipment Identification
Equipment identification includes providing the equipment name, description of component sampled (e.g., hydraulic tank and engine crankcase), equipment OEM, equipment model, equipment serial number, fleet number, etc.
This identification should be precisely the same for each sample. If not, the equipment could be registered with the oil lab as the wrong equipment, and the trending history will be lost. Using a unique ID provided by the laboratory for each piece of equipment is better.
Additional identification data to be provided: Sump capacity and cooling mode (air, oil, or glycol-based liquid ) are also helpful when submitted with the oil sample.
Oil in Use
For the oil in use, make sure to identify its brand, its name, its type, and its viscosity grade. Since oil manufacturers produce hundreds of products, providing only the oil brand, such as Shell or Total, or providing only ISO VG 320 or SAE 5W30, with no additional information, is not enough.
Oil analysis is about assessing oil properties, wear, and contamination. The lab must know the oil that is in use so that the analysis can be performed correctly.
Molybdenum, for instance, is a metallic additive used by some lubricant manufacturers, whereas it is considered wear or contaminant for other lubricants. In this case, the diagnostician could make a wrong conclusion simply because he is unaware that Molybdenum is within the oil formulation.
Component Age
Component age can be provided as the number of operating hours, kilometers, or miles on the equipment since commissioning. Providing this information will help the oil analyst benchmark with similar equipment operating in a similar environment.
Oil Age
Oil age reflects the oil usage between the last complete oil change and the moment of sampling. It is typically reported in hours, kilometers, or miles. This information is essential to accurately identify a divergence from normal wear patterns by normalizing elemental data to “Rate of Wear” calculated by the formula below.
Hours of operation could be kilometers, hours, or days. Recording the sampling date is complementary information, especially if oil sampling is triggered on a calendar basis.
Let’s look at the elemental analysis values extracted from a gearbox oil analysis report. The first reading of iron content in sample 04 and sample 05 will tell us that sample 04 wear is higher than sample 05. But the oil in sample 04 was in service for 73 more hours. The oil age is helpful in correctly assessing elemental analysis data.
Top-up Amount
The top-up amount refers to the volume of oil added between the last complete oil change and the moment of sampling. Topping-up oil helps normalize wear, contaminants, and additives. Adding fresh oil to your equipment between oil samples affects oil analysis data because of dilution.
Additional Information
The more information provided to the oil analyst, the more accurate and relevant the findings will be. These include:
- Lubricant abnormalities such as bottom sediment and sludge, foam, and varnish.
- Work performed on the sampled equipment like an overhaul.
- Operating conditions like speeds, loads, service duty, ambient temperature, operating temperatures, and potential exposure to contamination such as dust or salt water.
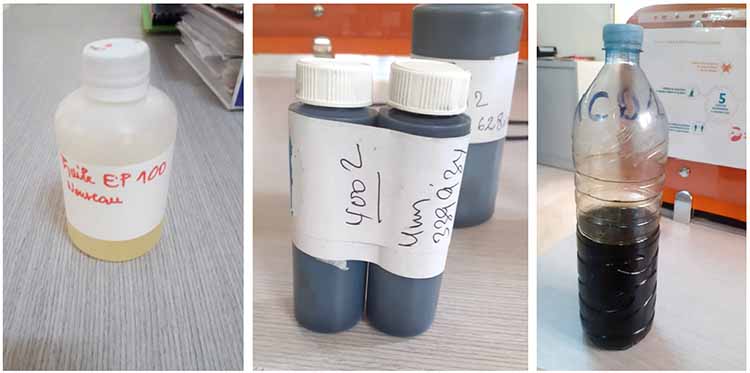
These oil samples are poorly labeled, and oil sampling best practices need to be followed. The sampling bottles are not suitable, and there is not adequate ullage in the bottle to allow sample agitation in the laboratory during its preparation before testing.
Completing the standard oil sample form is often a source of errors, either needing missing information or poor handwriting. In this era of digitalization and to reduce the risk of inadequate sample labeling, many laboratories provide web platforms and mobile applications, which are not only for oil samples pre-registration but also for analysis data management.
In such cases, the laboratory provides sampling bottles already labeled with barcodes. Equipment should already be registered, and there is no need to enter information like equipment ID or machine serial number – only changing information like running hours and top-up amounts.
The key takeaway is that oil analysis results are interpreted based on the sample submitted and the supporting information accompanying it. The more accurate information you share with the lab, the more precise the diagnosis.
So, labeling the oil sample accurately and thoroughly, either by handwriting or registering online, is urged to guarantee an accurate oil analysis interpretation.