In most industrial facilities, over 50% of all lubrication points are lubricated with grease instead of oil. Don’t believe me? Just count the number of electric motors in your plant. Unlike most oil-lubricated assets, where OEM recommendations provide at least a starting point for lubricant selection, greased lubricated components often don’t have simple guidelines for choosing the proper lubricant.
This lack of information frequently leads to many “experiential” grease selections (red grease worked well the last time…) instead of solid lubrication engineering. In my experience, incorrect grease selection is one of the most common failures in many lubrication programs.
What Is Grease?
Greases are comprised of three main “ingredients”: base oil, additives, and a thickener. The amount of each will vary based on grease type and NLGI grade but is usually in the range of 60-75% base oil, 5-20% additives, and 5-25% thickener. Just like lubricating oils, they are formulated for specific applications by choosing the appropriate base oil, additives, and, in the case of grease, thickener chemistry for optimum performance.
Base Oil Basics: Building Blocks of Lubricating Grease
Just like lubricating oil, the purpose of the base oil is to provide oil with sufficient viscosity to create an oil film capable of maintaining the complete separation of moving parts in the load zone of the bearing or other lubricated component. Base oils used in grease conform to the same API base stock categories as lubricating oil:
API Group I
Base oils derived from refined crude oil containing relatively high concentrations of unsaturated and aromatic compounds and sulfur. These oils provide good natural solvency and help enhance additive solubility but are prone to oxidative breakdown.
API Group II
More highly refined base oils with lower levels of unsaturated aromatics and sulfur compounds exhibiting better oxidation resistance and higher viscosity indices than Group I oils.
API Group III
Hydrocarbon base oil that has undergone significant chemical treatment and processing to remove almost all undesirable impurities, resulting in better oxidative stability and a higher viscosity index than either API Group I or II.
API Group IV
These oils are synthetic hydrocarbons, with the overwhelming majority being poly alpha olefin (PAO) based. Most greases labeled “synthetic” are manufactured using API Group IV or highly refined API Group III base oils.
API Group V
Oils in Group V comprise a host of different synthetic fluids, such as die-esters, polyol esters, poly glycols, and fluorocarbons. Greases containing API Group V base oils are far less common and are typically only found in highly specialized lubricants, such as those used for very high temperatures, extreme service life, or radiological applications.
Just like lubricating oils, the viscosity of the base oil within the grease can usually be found in the Product Datasheet (PDS) and is one of the most important properties when deciding the most appropriate grease for any given application.
Understanding Grease Additives: Roles and Benefits
The additives found in greases are similar in form and function to oil additives. The most common being antioxidants and rust and corrosion inhibitors.
Common Additives and Their Functions
Antioxidants help to prevent the base oil from degrading through a combination of free radical scavenging and breaking the chain reaction of oxidation. Rust and corrosion inhibitors coat metal surfaces to prevent rust and other corrosive processes, and they serve to neutralize corrosive materials through an acid-base reaction.
In addition, many greases contain anti-wear (AW) and/or EP additives (EP). These additives protect components under mixed-film or boundary lubrication conditions by providing a heat-activated layer on the surface of the component under elevated loads and temperatures.
AW and EP additives found in grease are similar in function to AW and EP additives found in lubricating oils. They are comprised of organo-sulfur and phosphorus compounds such as zinc-dialkyl-dithiophosphate (ZDDP).
The one class of additives that can be slightly different in lubricating greases is the incorporation of solid additives, such as molybdenum disulphide, often referred to simply as “Moly.” While some oils contain solid additives, their use is far more prevalent in lubricating grease since the grease matrix can more readily hold these additives in suspension.
Greases that contain moly or other solid additives are often used in slow-turning, heavily loaded applications, particularly where shock loading is anticipated. Moly is similar in crystalline structure to graphite, existing in mineral “plains.” While very strong in supporting radial loads, the weekly bonded crystals plains allow for a reduction in the coefficient of sliding friction under “stick-slip” conditions.
The Role of Thickeners in Grease Performance
Grease thickeners have a minimal bearing (pun intended!) on how well a grease lubricates.
Types of Grease Thickeners Explained
While some thickening agents, such as calcium, have been shown to have some mild EP properties, the number one role of the thickener is as a carrier of the base oil and additives. For this reason, grease thickeners are sometimes referred to as “sponges,” much like dish sponges that carry water (base oil) and dish detergent (additives) to clean dirty dishes.
Grease thickeners are usually made from one of three types of compounds. Simple and Complex soaps of inorganic elements such as lithium, calcium, and aluminum are the most common.
Soap-Based vs. Non-Soap Thickeners
The term “soap” refers to the chemical nature of these compounds and how they are made through a saponification reaction. Simple soaps are made by reacting an organic long-chain acid, such as stearic acid derivatives, with an alkali metal to form an organic salt.
Complex soaps use a shorter (smaller) compounding organic acid in addition to the long-chain fatty acid to “bind” the thickener together. The net result is a thickening agent with a more “entwined” network of fibers that helps with better grease stability properties such as bleed rate, dropping point, and shear stability.
Non-soap thickeners are most commonly a class of thickeners called “polyurea.” Polyurea thickeners are made from the reaction of a diisocyanate with a mono or di-amine. Because polyurea thickeners are “ashless” (do not contain any metals), they have better oxidative and structural stability, which is why they are sometimes preferred for electric motor greases and other applications with longer regrease intervals.
High-Temperature Applications and Clay Thickeners
Clay thickeners are used for high-temperature applications (for example, lubricating bearings in a kiln or oven). Most commonly, bentonite clay is purified and milled to an exacting particle size before being blended with base oil and additives. Clay works in a similar fashion to adding corn starch to a gravy or sauce, binding together other constituents into a thick slurry (grease). Like corn starch, the more thickener you add, the “thicker” the grease.
As stated earlier, the primary role of the thickener is as a carrier for the base oil and additives. As such, grease performance properties shown on a grease’s Product Datasheet (PDS) include a series of tests determining how the grease thickener will work during application and in-service.
Essentially, these seek to answer the questions, “How easy will it be to get the grease from the grease gun (or automatic greasing system) to the bearing, and how long will it retain its chemical and structural integrity during prolonged use?”?
Grease Performance Properties
Consistency
Consistency is one of grease’s most important properties. It is measured using the ASTM D217 cone penetration test (Figure 1).
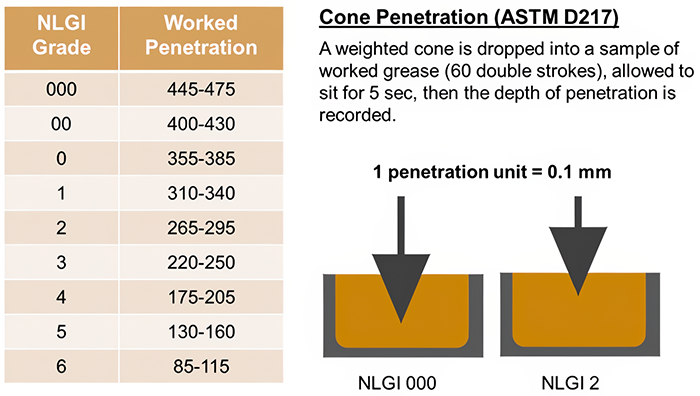
Figure 1: Grease Consistency per ASTM D217
Prior to the test, grease is forced through a mechanical grease worker to apply a shearing force to it. After working for 60 double strokes, a metal cone is dropped into the grease sample, and the depth of penetration is measured in tenths of a millimeter. The result is used to assign the grease’s NLGI grade, referenced when greases are labeled AW1 or EP2, for example.
Consistency, sometimes called thickness, should not be confused with viscosity. The viscosity of grease is the viscosity of the base oil contained within the grease, not how “thick” or “thin” the grease appears when it is pumped from the grease gun. In fact, grease consistency and grease viscosity often trend in opposite directions.
For example, grease that is to be used for a high-speed open bearing needs to be thick enough that it will not get displaced by centrifugal force but will be formulated with a low base oil viscosity due to the high operating speed. We might choose a “thick” NLGI Grade 3 grease with a low viscosity ISO VG 100 cSt base oil.
Grease consistency and viscosity often trend in opposite directions.
By contrast, if we elect to use grease for a small gear reducer to prevent shaft seal leakage, we need a base oil with a higher ISO VG grade due to the output shaft’s slow speed. Still, we would likely choose a “thin” grease (NLGI 00 or 000) so that the rotating gears can properly distribute the lubricant throughout the gear case.
In some cases, where grease is to be applied in cold-temperature conditions or through long lines in a centralized lubrication system, it is advantageous to use a very low consistency (“thin”) grease such as an NLGI grade 0 or 1. Compared to the equivalent NLGI grades 2 or 3, these greases may appear to be thinner.
However, as stated previously, consistency is unrelated to lubrication performance once the grease enters the load zone. Table 1 shows the relevant performance properties for four commonly used multipurpose greases from a major lubricant supplier.
As can be seen from the product specifications, viscosity and viscosity index, as well as load-carrying tests, show identical results for all four grades. As such, each of these greases would provide the same lubrication performance, assuming again that the difference in grease consistencies does not prevent the grease from getting to and staying at the load zone of the bearing.
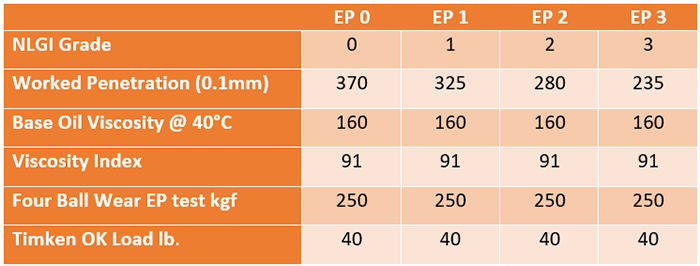
Table 1: Comparison of Four NLGI Grades of a commonly used multipurpose EP grease
Dropping Point (ASTM D2265)
The dropping point of a grease refers to the lowest temperature at which the grease will start to liquify and is a measure of how well a grease can resist elevated temperatures. The test grease is slowly heated until the grease is observed to have liquefied, as signified by a “drop” of liquid falling from the bottom of the test grease.
Grease should never be used close to its rated dropping point. As a rule of thumb, a grease’s maximum sustained operating temperature should be 100-150 °F (50-80 °C) below the dropping point. Typically, complex metal soap thickeners such as calcium complex, lithium complex, and aluminum complex exhibit the highest dropping point compared to other commonly used greases (Table 2).
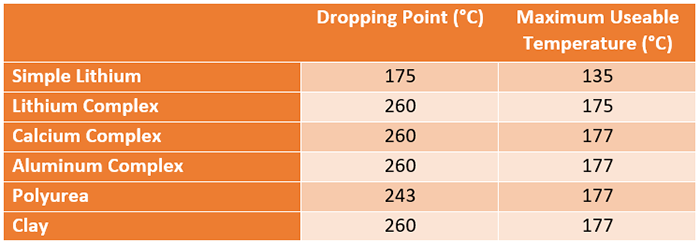
Table 2: Example dropping points for different grease thickeners
Other Performance Tests
Other tests are used to ensure the chemical and mechanical stability of grease of different thickener types, depending on the application. These include water washout (ASTM D1264), grease bleed rate (the rate at which the base oil separates from the thickener) (ASTM D1742), roll stability (ASTM D1831), wheel bearing leakage (ASTM D1263), and water spray test (ASTM D4049).
Compatibility between grease types can make or break lubrication success.
When selecting a grease for a specific application, it is important to choose the correct thickener type and consistency. This should include the anticipated operating temperature and ambient stressing conditions. Table 3 compares different thickener types and their performance under different conditions.
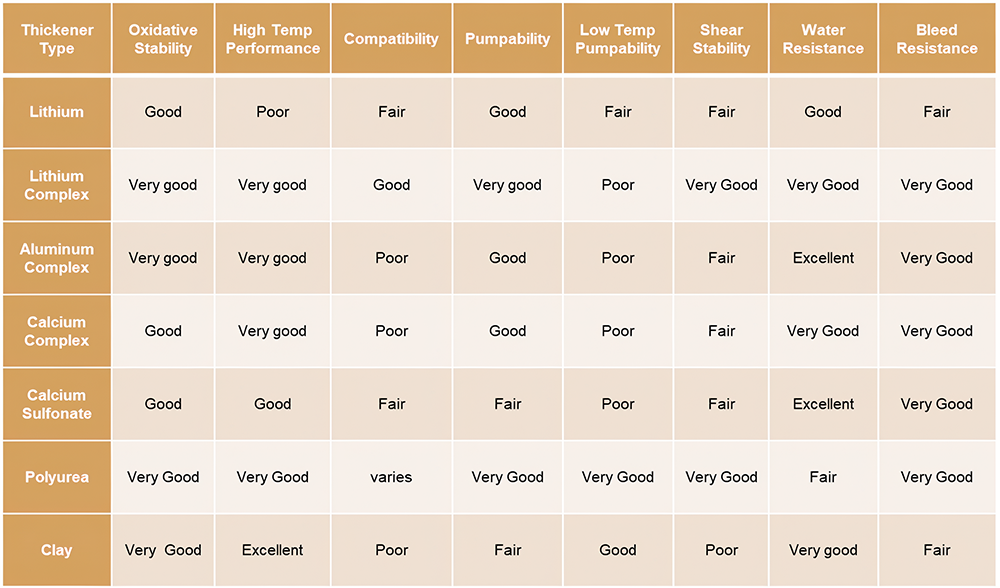
Table 3. Comparing thickener types and their performance under various operating conditions
Because thickeners are made from such a wide array of chemistries, compatibility must always be considered when intentionally or accidentally mixing different greases. Whenever two greases are incompatible, the consistency of the mixed greases will either increase to the point of solidifying or decrease and liquefy; neither condition is desirable.
A quick internet search for “grease compatibility” will yield any number of compatibility charts identifying which grease thickener types might be compatible with another type. These charts are very misleading and are often inaccurate.
While it is true to say that when mixing two different greases, there is a 30-50% chance of incompatibility, it is almost impossible to predict how two greases will react based on their chemical constituents.
For this reason, whenever switching from one grease to another, the question of compatibility must always be addressed. Most lubricant manufacturers can provide evidence of compatibility testing for commonly used greases with their own and their competitors’ products. However, if no data exists or is ambiguous, proper compatibility testing prior to switching greases is always recommended.
To do this, binary mixtures of grease A and B should be made in the ratios of 75:25 and 25:75 and key thickener performance properties, mainly worked penetration and dropping point compared to pure samples of both A and B.
Any significant deviation in thickener performance between the mixtures and the pure greases should be considered evidence of an incompatibility requiring careful cleaning and flushing before switching greases.
Multipurpose vs. All-purpose Grease: Understanding the Difference
While most grease manufacturers make dozens of different greases, by far (50-75%) of lubricated bearings are greased with multipurpose EP2 grease. Most of these greases use a simple lithium or lithium complex soap, though calcium complex can also be found in some formulations.
Aluminum complex is also used, particularly in food-grade NSF H1 greases, since lithium is not considered safe for incidental food contact. Most multipurpose greases have a base oil viscosity in the 150-320 cSt range, are ideal for pillow block bearings and other moderate-speed applications, and are usually formulated with chemically active AW or EP additives.
While “multipurpose” suggests a wide variety of applications, multipurpose is not the same as “all-purpose.”
Common Misapplications of Multipurpose Grease
The base oil viscosity of most multipurpose greases is too high for electric motors – particularly higher HP or with rotational speeds >1800 RM – or directly coupled bearings. This can give rise to excess internal (fluid) friction, which can increase internal temperatures, resulting in premature lubrication degradation and damage to the motor’s winding insulation.
The base oil viscosity of most multipurpose greases is too high for electric motors.
A better choice would be a designated “electric motor grease,” likely to have a base oil viscosity in the 100-120 cSt range and a more shear-stable thickener.
Another common misapplication of multipurpose grease is its use in grid and gear couplings. Larger couplings exert significant torque, which must be accounted for when formulating a grease for a lubricated coupling. Most coupling grease is formulated with a shear-stable lithium complex thickener, together with a high (700-3500 cSt @ 40°C) base oil viscosity to support the load.
Most are NLGI Grade 1 to permit ease of dispersion and are formulated with tackiness agents to help the grease stay on the coupling under high-speed centrifugal force. The specific gravity of the thickener is also carefully balanced to be similar to the base oil to prevent excess base oil bleed-out under operating conditions. Whenever greasing a coupling, always use a designated coupling grease rated for the coupling type (CG-1, CG-2, or CG-3).
Grease Selection: Matching Performance to Application Needs
One of the biggest mistakes I see from my 28 years of field experience is incorrect grease selection. Unlike oil-lubricated assets, where OEM recommendations are often a great starting point, there is a lot of “tribal knowledge” and “smoke and mirrors” around grease selection.
I recall dozens of times when I was told that red grease is better than blue or green beats purple. For the record – grease color has no relevance to how it lubricates. The color is simply a die the manufacturer puts into the lubricant for branding and identification purposes.
Understanding Application-Specific Requirements
Like any other application, grease selection starts with the viscosity of the base oil contained within the grease. This can be found on the grease Product Data Sheet (PDS), which is readily available online. For rolling element bearing lubrication, the viscosity should be chosen to yield a Kappa value (the ratio of the actual viscosity of the base oil relative to the bearing minimum viscosity) of 2-4.
For a primer on Kappa and viscosity selection for element bearings, refer to my article in the April 2023 edition of Precision Lubrication Magazine.
We must decide the best thickener once the correct viscosity has been selected.
Evaluating Delivery Mechanisms and Environmental Factors
This requires understanding the ambient conditions (speed, moisture, ambient temperature, machine temperature, etc.) and delivery mechanism. We need to choose not just the correct thickener chemistry but also the preferred consistency.
In doing so, we need to know, “Will the regrease be applied to a zerk fitting on the bearing housing or through 20 feet of grease line? Is this for a large multi-point centralized grease system, or will we simply pump grease via a grease gun? How cold will it get in winter?”
Lastly, we need to decide what other properties do we need. Do we need AW or EP additives? Is synthetic grease better due to higher or lower temperatures or extended grease intervals?
Grease selection is as critical, if not more critical, than oil selection. So, think carefully and don’t get caught up in the hype of the latest “silver bullet grease” that’s “slicker” than everyone else’s and as sticky as molasses!
Correct grease selection requires careful consideration of bearing operating conditions such as load, speed, size, and type, along with some basic knowledge of ambient stressing conditions and delivery mechanisms. That is all that might stand between successful lubrication and a failed bearing!