In the complex and evolving world of the lubricants industry, we’re constantly faced with new challenges. Most end-users have recently suffered from the increasing cost of lubricants and greases. In most instances, these changes have their root cause in supply chain disruptions and challenges brought about by extreme weather events and the second-order effects of Covid-19 lockdowns.
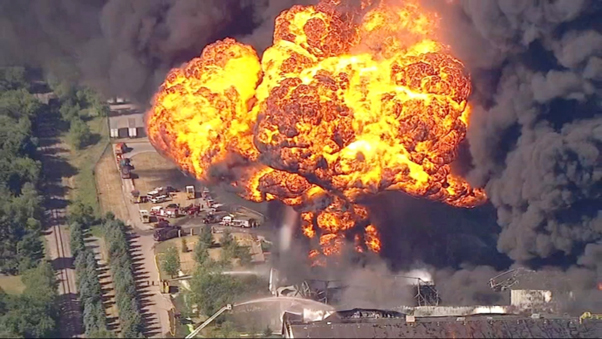
Fire at the Chemtool Rockton facility in 2021
Enter Calcium Suphonates
Calcium sulphonate complexes are an alternative thickener technology that has historically been sold as a high-performance (but also high-cost) alternative to lithium complex thickeners.
Often used in high-temperature or high-load applications, the major obstacle to broader adoption has usually been the steep price premium relative to lithium complexes.
Anecdotally the cost gap was 200-300%, but with the recent increase in lithium prices, this has shrunk to as little as 30-50%, making calcium sulphonates an attractive proposition.
These thickeners owe their performance properties to the unique structure of the thickener. Derived from the same over-based TBN 400 calcium sulphonates in engine oils detergents, these thickeners exhibit excellent corrosion resistance.
The complex gel structure gives them excellent shear stability, water resistance, and high-temperature performance. On the structure of these greases, Andy Waynick explains in episode 36 of Lubrication Experts:
“You’ll see drawings of it, and it will typically have a spherical core, which we do know exists, and presumably inside that core resides all the excess calcium carbonate in the amorphous form, calcium cations, carbonate anions, and some hydroxide anions because usually, you need some of that as well to make a stable structure. And then around the sphere pointing outward is the neutral calcium alkyl benzene sulfonate in what’s called a reverse micelle structure.”
The excess calcium carbonate gives rise to yet another valuable property of these greases – the EP performance. Calcium carbonate (in the form of calcite) is a lamellar material on the nanometre scale with low shear stability that can act as an effective solid lubricant similar to Molybdenum Disulphide or Graphite. This makes them extremely useful in slow-speed high-load applications commonly associated with the mining industry.
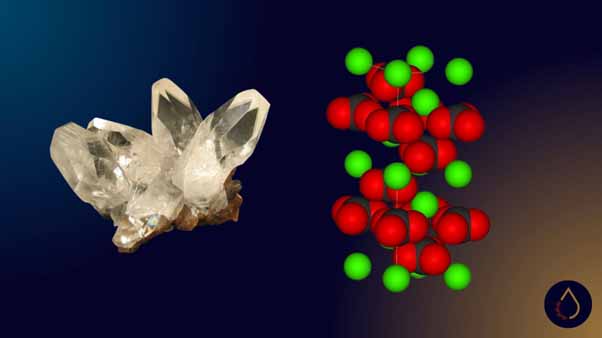
Calcite crystal and crystal structure
One note of caution when selecting these greases – the manufacturing process is significantly more sensitive than that of standard simple and complex soaps. The result is some significant divergence in the quality of these thickeners available on the market.
I have tested several calcium sulphonate thickeners where the calcite particles were on the millimeter-scale or the thickener liquefied at temperatures less than 70°C. This makes a manufacturer’s quality control program essential to the procurement process.
Cost-Effective Alternatives
Given their performance and relative cost, calcium sulphonate complexes are a compelling alternative to lithium complex greases. Still, if the raw price of lithium continues to increase, options will also be needed for the standard lithium soap greases that dominate market share.
This is not so simple – lithium soaps have historically been used as multipurpose greases for their “jack-of-all-trades” performance profile.
Lithium greases don’t perform any function spectacularly well, but they also do not have a significant weakness.
This is untrue of other metal soaps – sodium greases, for example, are water soluble, and aluminium soaps are susceptible to shear. Simple calcium greases have historically had an upper operating temperature limit of around 60°C because water is part of the thickener structure.

Relative performance profile of grease thickeners – note this is a select, not comprehensive list of performance attributes!
Another form of calcium thickener may play a role. Some grease manufacturers have begun to make anhydrous calcium soaps (anhydrous, meaning “without water”).
These offer improved high-temperature performance allowing for sustained operating temperatures above 100°C and other properties similar to or exceeding lithium soaps.
Best of all, the raw material required is lime rather than lithium hydroxide. Lime is abundant, widely available, and can be purchased at a fraction of the cost.
Better still, anhydrous calcium-lithium soaps can be manufactured. Blending the two can offer a compromise of cost and performance when a performance profile almost exactly matching lithium greases is required.
The Future
There are still several barriers to adoption before lithium soaps can be displaced as the world’s most popular grease type. The first is the overwhelming approvals given to lithium and lithium complex greases by equipment OEMs, who will need to be convinced of the benefits of alternative technologies.
The second is manufacturing capacity and capability. Very little anhydrous calcium is currently being produced, and as remarked upon earlier, the quality of calcium sulphonate complexes can vary greatly, even batch-batch at certain facilities.
But suppose EV demand continues to increase at an exponential rate. In that case, the ever-increasing price of lithium will likely be a solid motivation to find, test and approve alternative formulations.