Those who have worked in or around maintenance and reliability have probably heard about the hidden plant. This term refers to that portion of the productivity of any industry that, for some reason, is wasted and goes completely unnoticed in the eyes of the maintenance, operation, or reliability departments.
One of the advantages of having a predictive maintenance program is precisely identifying those points where this valuable opportunity is wasted. Timely identification will bring the potential defect or underutilization to light so that it can be eliminated and later improved.
The main problem in cases where the hidden plant is genuinely hidden is when everything seems to be going well, equipment does not fail, unscheduled maintenance stops are minimal, and productivity objectives are met.
When a component is replaced based on time and not on its condition, such replacement may be premature or late, and the impact of the benefit or damage may not be addressed. This is one of the clearest examples of that hidden plant.
Don’t settle for the in-service life of physical assets without asking whether they have reached their expected life cycle.
Laboratory oil analysis has a long history, dating back to the early 1940s. However, grease analysis enjoyed a different fortune, and its entry into the predictive tool hall of fame was delayed until well into two thousand’s.
Grease analysis has a comprehensive battery of tests ranging from the most straightforward, such as determining its elemental composition or knowing the type of thickener, to determining its characteristics by simulating actual operating parameters.
However, due to its short history, grease analysis still needs to be noticed by many industries. The advantages it can provide, not only for maintenance but also for the hidden plant, are relatively unknown.
Grease Analysis Case Study
Let’s look at an actual case study in an industrial plant where everything was going well, and unscheduled stops have been at a minimum for years.
For quality reasons unrelated to maintenance, it was decided to do a grease analysis on two products from different suppliers. After repairing one of the bearings, a third-party workshop added Grease 1 to the bearing. The other grease (Grease 2) has been in service for many years in this type of bearing, among others in the plant.
The results of both the technical data sheet and the lab analysis of both products in service are shown in the table below:
The bearings in these cases are a 23248EMW33 type with a life cycle of approximately ten years, a speed of 250 rpm, a maximum working temperature of 190°F, an ultrasound level that does not exceed 18dB, and a regreasing volume of 10 – 15 grams per week, a luxury for any maintenance team. However, during a visit to the plant, a couple of symptoms are observed that, to the expert eye, can be of great importance.
The lower part of the bearing has a black stain of an oily substance that reaches the ground, and when the bearing is replaced (when it has reached its life cycle), the race and the housing have a black crystalline powder in them.
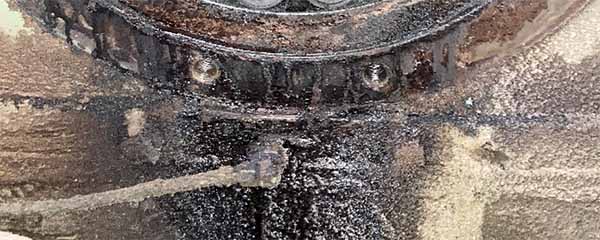
Exterior Bearing Base
These two symptoms indicate several things that are of high importance for the life cycle of the bearing and, therefore, for the availability and reliability of the plant.
- The black stain is only oil bleeding from the grease
- The powder in the housing is the grease thickener
In this case, we see a complete separation of the two main elements of the grease. Due to certain conditions, the oil and the thickener can separate. What are these conditions? These are mainly high temperature and EHL lubrication (elastohydrodynamic).
A simple analysis and calculations about the grease type that this bearing requires result in grease with about ~500cSt mineral oil, extreme pressure additives, and high-temperature resistance, or its equivalent with synthetic oil.
A basic calculation of the expected life reveals that the L10 bearing life is 180,000 hours, which means an expected life of almost 21 years.
However, the bearings are replaced around every ten years!
Let’s go back to the hidden plant. Of course, we want to avoid unscheduled downtime. However, sometimes the scheduled downtime may have been programmed differently or without rethinking scenarios that could cause a component to fall short of its desired useful life.
Based on some life cycle calculations, if the correct grease were in place, the bearing could stand for 18 years, and the regreasing frequency would drop to once every four weeks.
Conclusions
In maintenance and life in general, we are used to keeping things as they are without wondering if anything can be improved. In most cases, improvements are made due to a problem or failure that results in an economic issue or lost production.
Unfortunately, our reality is that we are reactive rather than proactive, and job needs mean that we often do not stop for an instant and wonder if what we have been doing for years can be improved in some way.
The economic savings, in this case, are not intended to reduce grease consumption or relubrication intervals but rather to take care of the asset used to produce a good, in this case, the bearing.
If the grease had been selected correctly, the life of this bearing would reach 20 years without problems. Still, for day-to-day reasons, it is only half that, and the maintenance personnel feel satisfied with this service time. For many, seeing a bearing reach this time in service is an achievement.
How many industrial plants today have equipment that maintains the type of grease or oil since the beginning of its commissioning?
How many bearings use a type of grease that is not the most appropriate but that, for reasons of time or lack of attention, will never see an improvement?
How many maintenance teams waste those valuable hours of work on something that, if a bit of time is spent, can directly impact improving the availability of the equipment?
How often have you considered doing a grease analysis on the most critical bearings in your plant?
How often have you gone from being reactive to being proactive in your day-to-day life?
The hidden plant is one of the market niches that can give the best performance if treated from a profit point of view. In this case study, replacing the type of grease has an impact on production of 0.06% over ten years.
This is equivalent to increasing the finished product sales by 1.3% accumulated in ten years. Of course, finding the hidden plant provides many benefits at all levels of the production and sales chain.