Oil analysis has a strong history of being incorporated into maintenance strategies to optimize lubricant life and protect oil-lubricated assets from wear and damage. Grease-lubricated components, which are much more widely present, are often neglected from consideration because of some of the challenges of obtaining representative grease samples and methods for analyzing small quantities typically available.
More recently, developments of grease sampling tools and enhancement of grease analysis methods have led to global standards for grease sampling and analysis and the opportunity to incorporate this as a strategy to improve sustainability in these assets.
Standards and methods for sampling various grease-lubricated components and analysis tools and tests for characterizing grease consistency, wear, contamination, and oxidation condition have been developed and are widely adopted.
Using these tools to optimize grease life, reduce waste and maintenance resources, improve grease-lubricated assets’ availability and uptime, and extend grease-lubricated components lead to sustainable asset management practices.
Principles of Sustainability
There are numerous principles of sustainability applied to various economic undertakings and industries. A common basis for these initiatives is the 17 Goals of Sustainable Development from the United Nations
Keying in on several of these goals, a list of “Attainable Goals of Sustainable Development through Grease Sampling and Analysis” can be provided:
- Conserving Energy – Selection of optimal viscosity and grease consistency at operating temperature to prevent friction and wear AND minimize energy losses
- Conserving Natural Resources – Utilizing Condition-Based Grease Replenishment to minimize lubricant consumption; early identification of abnormal wear for proactive intervention to purge contaminants and extend equipment life
- Minimize Environmental Impacts – Reduce waste by reducing grease consumption, timely and targeted grease replenishment instead of time-based or lagging indicator
- Economically Sound Processes – Factoring the total cost of operation rather than the price of the product, greater RONA (Return on Net Assets) on equipment with longer life.
- Enhancing Employee, Community, and Product Safety – Less over-greasing means less spillage and potentially fewer maintenance tasks.
Grease Sampling Considerations
Existing practices for obtaining grease samples from bearing housing and gears often need to be more consistent. They likely do not represent the actual condition of the “active” grease near the lubricated surface. The challenge in optimizing a grease analysis is the development of tools that utilize a smaller amount of grease that enables representative grease samples without disassembling the component.
In the example of the Grease Thief, such a sampling fitting is also optimized for the subsequent laboratory analysis with just 1 gram of grease.
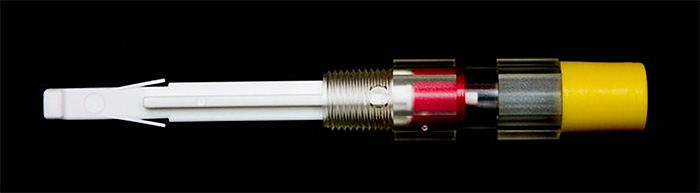
Figure 1: The Grease Thief
The Grease Thief was developed for this purpose, with the first design focusing on pillow block bearings. At the National Institutes of Health, failures were being experienced on critical grease-lubricated fan bearings.
Without a good way to test greases, vibration analysis was used to detect failures in progress and schedule repairs. The root cause of the problem was often overlooked. After implementing the Grease Thief tool for sampling, systemic issues were identified, including grease mixing and greases contaminated with particulate during greasing. By sampling the equipment in the field, many potential problems were identified and corrected without damage to the bearing.
The principle behind the Grease Thief is obtaining a targeted grease sample from the live zone. Similar to the principle of a liquid sample “thief,” the device can travel from the access hole to the active lubrication location near the bearing or gear mating area and bypass the non-representative grease.
The sampler remains closed with the piston in place over the opening until it is positioned to core a representative sample.
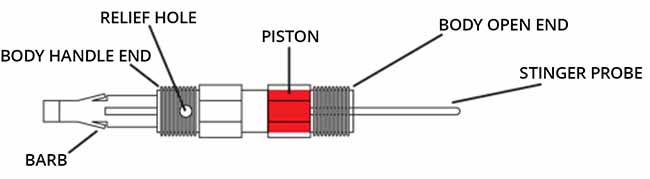
Figure 2: Grease Sampler for Gearbox Testing
To achieve this, the grease sampler is inserted into a t-handle extension to permit remote actuation and capture of the sample at the site of active grease use and wear generation adjacent to the mating gears or bearing surface.
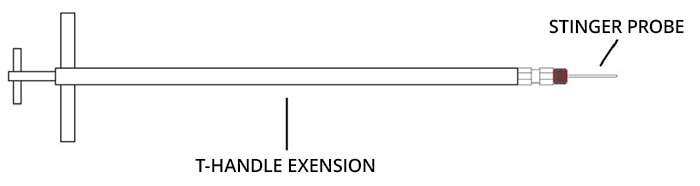
Figure 3: Grease Sampler in T-handle Extension
Grease Analysis Approach
A program that targets the “Attainable Goals of Sustainable Development” will include a test slate for grease analysis that helps to inform decision-making to address these goals.
An example of this was a grease analysis project initiated by Boeing to enhance the asset availability and sustainability of the Chinook helicopter, a key component for cargo and personnel movement for numerous military organizations worldwide.
The analysis test slate selected would be based on the known oxidation stressors and contaminant sources found in the machine application and additives present in the grease to extend life. The ASTM Standard Test Method for evaluating in-service greases is D7918.
This method uses the tests identified in TABLE 1, which list the key parameters measured and assessed in the grease. Two additional tests (TABLE 2) are typically included in the analysis, although they are not found in the current version of the ASTM D7918 standard.
The Rotating Disc Electrode (RDE) Spectroscopy test and Fourier-Transform Infrared (FTIR) Spectroscopy test provide elemental and molecular spectroscopy results, respectively, and complement the analysis performed in D7918 by monitoring non-ferrous wear particles, additives, contaminants, and the oxidation of the grease.
While the ASTM D7918 method does provide for a particle counting test, a thin-film direct imaging technique, it was determined that the variables in the greases used in the aircraft, as well as the anticipated conditions of the greases, may make this method ineffective due to insufficient optical clarity of the grease. Therefore, the particle counting function was substituted by monitoring the grease’s elemental Silicon (Si) levels as measured by the Rotating Disc Electrode Spectrophotometer.
As the most common source of external particulate was expected to be sand or dirt based on operating environments and action of air turbulence, Silicon was deemed to be a suitable indicative parameter to measure the ingression of these particles.
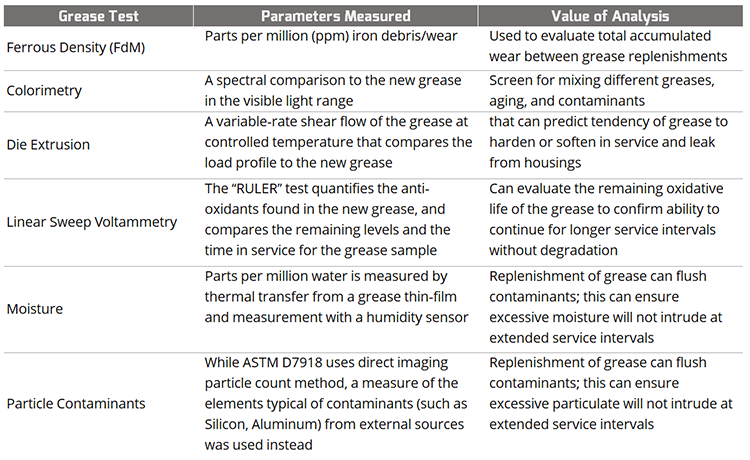
Table 1: ASTM D7918 Grease Analysis Tests
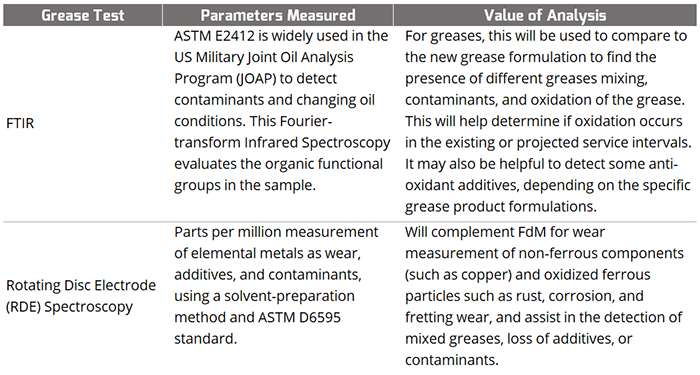
Table 2: Additional Grease Tests, not in ASTM D7918
The individual grease sample results were compiled to find the seven parameters influencing grease life. These included elemental iron (Fe), elemental silver (Ag), elemental Silicon (Si), ferrous debris level, moisture, Die Extrusion Index (consistency), and oxidation index.
These parameters were plotted as a function of flight hours since the last grease service to determine the interval at which each parameter began to degrade. A curve fit was developed for each graph based on the flight hour trend behavior of the parameter. These relationships were primarily linear, but some were logarithmic.
The formula for the curve fit was used to calculate the number of flight hours that corresponded to the target parameter replenishment level. The optimal service interval was described as the number of service hours that would allow grease replenishment before the onset of degradation.
In this way, each component would be adequately protected against wear and damage by ensuring that the grease would be replaced by new grease before it degraded or accumulated significant contaminants. An example of the regression analysis used to project the optimal interval is shown in FIGURE 5.
In the case of this parameter, “Oxidation Rating,” the target parameter replenishment level was selected at a value of 75, which corresponds to the remaining 25% of the original level of anti-oxidant additive protection. In this case, the curve fit line equation produces a value of 171 flight hours.
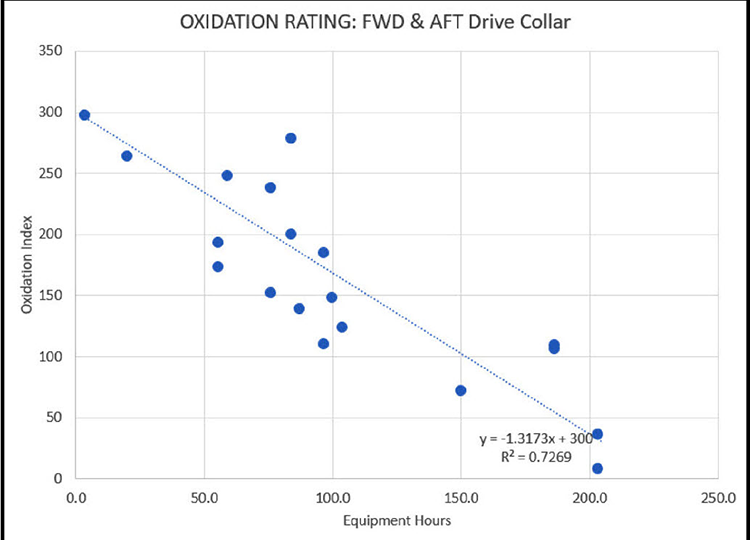
Figure 5: Drive Collar Samples Oxidation Rating
Findings
As a result of the study, the majority of the lubrication intervals were extended, many double the established grease service intervals currently fielded by the various operators. This extension allows each operator to adjust their grease servicing intervals, thus allowing a reduction in downtime and maintenance costs while ensuring the continued safe operation of the aircraft.
The benefit of the study is that final service interval determinations can be aligned with existing maintenance intervals to support a maintenance optimization effort completed by Boeing. These results translate to fewer interruptions to operations for required servicing.
In total, an estimated reduction from 98 lubrication tasks per 1000 flight hours to just 56 lubrication tasks per 1000 flight hours, and a reduction from 20 service interruptions per 1000 flight hours to just ten service interruptions per 1000 flight hours.
Sustainable approaches to asset management, electricity generation, transportation infrastructure, and other capital-intensive enterprises must be found to continue in an economically viable manner.
Our resources are limited, and approaches that optimize our use of these valuable resources are necessary sooner rather than later. Many corporations now recognize a responsibility to achieve this and are adopting new strategies to meet such goals.
A closer look at grease lubrication and recently developed technologies for grease sampling and analysis can help organizations operating grease-lubricated assets accelerate initiatives to increase sustainability in their enterprises.