Wear monitoring is one of the primary objectives of oil analysis for predictive maintenance. Many oil analysis tests are considered suitable for wear debris analysis, and some, like elemental analysis and Wear Particle Index, are recommended within routine analytical slates.
Others, like Analytical Ferrography, are only requested occasionally and are typically reserved for in-depth investigations whenever required.
Elemental Analysis
Elemental analysis is a part of almost all routine oil analysis test slates across many applications. It is a cornerstone of lubricant analysis and a powerful ally for wear detection at early stages.
Inductively Coupled Plasma (ICP) or Rotating Disc Electrode (RDE) are the most common analysis methods for conducting elemental analysis for used lubricants, and they are performed respectively per ASTM D5185 and ASTM D6595.
Elemental analysis is a standard method used to determine quickly and in one single measurement the concentration of various elements within an oil sample.
It identifies and quantifies at low parts per million (ppm) concentrations for at least 21 elements: Iron (Fe), Copper (Cu), Aluminum (Al), Chromium (Cr), Nickel (Ni), Lead (Pb), Silver (Ag), Tin (Sn), Silicon (Si), Sodium (Na), Potassium (K), Magnesium (Mg), Calcium (Ca), Phosphorus (P), Zinc (Zn), Boron (B), Molybdenum (Mo), Titanium (Ti), Vanadium (V), Barium (Ba), Sulfur (S).
Oil analysis professionals can monitor the levels of wear metals, additives, and some contaminants through elemental analysis. This helps assess the condition of oil and equipment and identify potential issues, such as contamination, additives depletion, or excessive wear.
However, it is essential to acknowledge the inherent limitations of elemental analysis. The ICP technique can detect elements accurately (with high repeatability) if the elements are below five microns in size, with repeatability tailing off for particles approaching and exceeding seven microns.
The RDE technique also provides confidence for detection up to a five µm size range, with detectability tailing off as particles exceed 10 microns. For RDE and ICP techniques, particle size visibility can vary by element type, such as copper and chromium.
While the accuracy of the analysis can be influenced by factors such as sample handling and instrument calibration, these techniques (ICP and RDE) are considered the preferred means for routine wear debris assessment for commercial labs.
Considering these constraints, most laboratories complement elemental analysis with additional test methods that detect particles beyond the incipient wear range (>5 µm size).
In the context of gearbox oil analysis, techniques like Particle Quantification and Ferrographic Analysis are complementary tools that provide a more holistic approach to monitoring gearbox condition.
Ferrous Density Analysis
The most prevalent and affordable method for assessing ferrous density is Particle Quantification Index (PQI), also known as Wear Particle Index (WPI).
This test directly quantifies the magnetic mass of ferrous debris in the oil sample, regardless of particle size and shape. It provides a non-dimensional value representing the total amount of the existing ferrous debris in the sample.
PQI is a powerful tool for wear detection, monitoring ferrous particles larger than the elemental analysis detection range.
In this regard, PQI is an invaluable complementary test to elemental analysis.
Performed per ASTM D8184, Particle Quantifier Index is recommended as a routine test for all types of industrial, mining, shipping, and aviation equipment.
Direct Read Ferrography (DRF) is another cost-effective technique for characterizing the wear concentrations of larger-size particles.
By leveraging the magnetic susceptibility of particles, DRF enables the calculation of the Wear Severity Index based on a direct reading of both large and small particles. Consequently, DRF can serve as a suitable alternative to PQI.
Analytical Ferrography
It is helpful to understand the underlying reason (the wear mode) whenever elemental analysis, PQ Index, or DR Ferrography indicates the presence of an elevated wear metal concentration. In these circumstances, it is helpful to ‘see’ what is occurring inside the machine.
Analytical Ferrography is a powerful and proven qualitative technique that utilizes a microscope to examine wear particle appearance, including the color, size, and shape of particles in the oil sample, to determine the different wear modes and the possible sources of wear debris.
The results are provided per ASTM D7684 and are complemented by photos, allowing the comments to be visualized. Given the time and expertise required to perform the diagnosis, its cost is relatively high.
Accordingly, it is conducted as a secondary test when other lower-cost methods have strongly indicated a problem.
With routine testing, the oil sample is drawn from the primary sampling location and represents the whole system. Secondary sampling locations close to the components should be utilized if a machine has multiple branches or subsystems.
These samples will reveal the highest concentration of wear metals and the likely source of the wear and failing components.
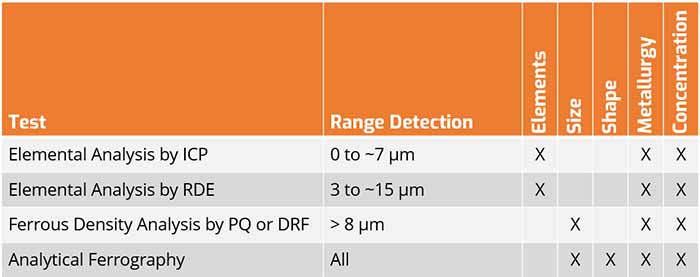
Ferrous Debris Analysis methods are complementary. Some are quantitative, and some others are qualitative. To get the complete picture of wear status in terms of concentration and characterization, routinely perform elemental analysis and ferrous density analysis. Follow up with Analytical Ferrography when necessary and cost-justified.
Given the above information, a well-designed analysis slate includes elemental analysis and Wear Particle Index as essential elements. When further investigation is needed, conduct Analytical Ferrography.
Please note that using permanently located oil sampling ports will yield the most representative results.
For a deeper investigation, oil analysts may opt for Filter Debris Analysis. This analytical technique involves examining debris and particulate matter captured within oil filters, which are explicitly designed to trap solid particles, wear debris, and sometimes even water contaminants.
Analysts can find critical clues about the types of wear occurring in the equipment by carefully scrutinizing the composition, size, shape, and quantity of particles in the oil filter.
By understanding the origins of these particles, maintenance teams can take proactive measures to rectify issues, prevent further damage, and extend the lifespan of machinery.
Case Study: Gearbox Condition Monitoring through Iron Content, Wear Particle Index, and Analytical Ferrography
The table below provides the oil analysis results of two samples drawn from a gearbox in the port industry. This case study focuses on the wear metals concentration data acquired through ICP and Particle Quantification Index.
Additionally, the Analytical Ferrography analysis was conducted only for the second sample, promptly following the release of the report of the first sample. All the other parameters are satisfactory, including Viscosity at 40°C, Total Acid Number, and Water Content.
A notably elevated PQ Index compared to the iron concentration detected by ICP has led us to deduce that there has been an accumulation of large ferrous debris within the oil sample, reaching notably high levels. This finding prompted consideration of abnormal wear phenomena inside the gearbox.
This could be attributed to various factors like the ingress of abrasive contaminants, suboptimal lubrication, misalignment issues, or excessive mechanical loading. It should be investigated further.
In this situation, maintenance personnel were asked to draw an urgent representative sample to confirm these abnormal results because this was the inaugural sampling for this gearbox.
One oil analysis report should never be used as the basis for a decision involving replacement or immobilizing equipment.
In addition to the routine analysis slate, Analytical Ferrography was requested. The lab was notified of the emergency and was asked for a quick turnaround.
Simultaneously, maintenance personnel checked the operating conditions of the gearbox, verifying the OEM-recommended parameters, the load, the speed, and the operating temperature.
They were also asked to assess alignment and vibration. Considering other non-destructive inspection techniques to confirm findings is recommended in these situations before embarking on any potentially expensive decision or action.
These combined actions are essential to promptly address and rectify any potential issues within the gearbox and provide a supporting finding. They will serve as crucial inputs for Root Cause Analysis once the lab releases the oil analysis report.
When the second sample report was received, the PQ Index result was confirmed high, and the iron content was relatively the same as the previous sample.
The Analytical Ferrography examination revealed the presence of several types of particles, including those attributed to Normal Rubbing Wear, Fatigue Chunks, Laminar Particles, Corrosive wear debris, Dark Metallo-Oxides Particles, Non-Metallic Crystals, Friction Polymers, and Fibers. Below is a compilation of potential sources of these particles:
- Rubbing wear particles indicative of normal rubbing wear.
- Friction polymers can be attributed to excessive mechanical load or stress on the lubricant.
- Fatigue chunks, suggestive of abnormal periodic machine vibration.
- Laminar particles are suggestive of a rolling contact failure.
- Dark Metalo-Oxides, potentially resulting from high operating temperature and/or suboptimal lubrication conditions.
- Fibers that may have entered the gearbox during maintenance or been introduced to the sample during its extraction.
These insights into the origin of the detected particles are invaluable for understanding the underlying factors contributing to the observed wear patterns. This case study is a concrete example of how combining wear debris analysis techniques is essential for gearbox condition monitoring.
By implementing this proactive approach, equipment managers can maintain high levels of equipment uptime and prevent costly breakdowns.