Case study data, information and images provided by POLARIS Laboratories®
Traditionally, for gas engines utilizing class 2 type gas, usually landfill, biogas, or mine gas, the gatekeeper for oil change intervals has been the silicon content. The industry condemning limit for silicon varies from around 100ppm up to 300ppm, depending on the engine’s original equipment manufacturer (OEM), the application, and the type of gas used as fuel.
Considering operating hours or loads, it is a common practice to change the engine oil weekly as the silicon content exceeds the recommended condemning level. Typically, this takes place regardless of the overall condition of other frequently measured parameters (base number, acid number, initial pH, etc.). It is not unusual to see the lubricant conditions well within OEM specifications, with only the silicon content considered abnormal.
Because these high levels of silicon can be derived from environmental dirt or siloxanes in the gas, they can be highly abrasive and cause significant damage to the components in the engine. The industry standard for measuring silicon content in gas engine oils is Elemental Analysis by ICP (typically ASTM D5185). However, this method only measures particles less than 10 microns in size and does not differentiate between different forms of silicon that may be present within the oil.
Looking for a Solution
When looking at options available to extend oil drain intervals, a U.K.-based power generation company contacted Delta-Xero® (a fluid systems manufacturer) to assess their new filtration systems as a potential way to remove or reduce contamination levels, optimize oil drain intervals, and realize better cost and environmental savings on the company’s operating units.
Proven Impact
DX-1006T Powertrain filtration units were installed on three gas engines at landfill locations in The United Kingdom to assess performance. Routine oil samples were taken during the operation. In addition to routine, industry-standard test packages, a micropatch test was also performed by POLARIS Laboratories® to assess the contamination levels present visually.
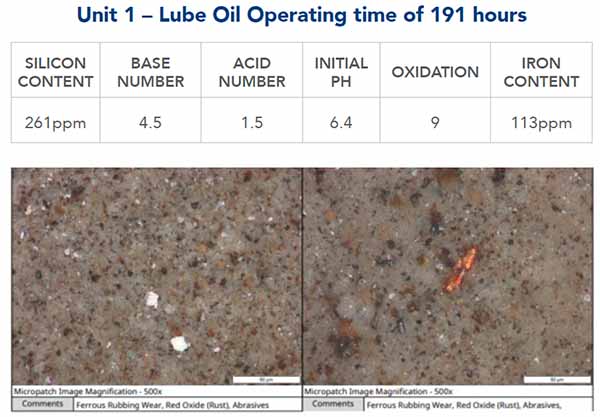
Micropatch testing results found contamination within the sample
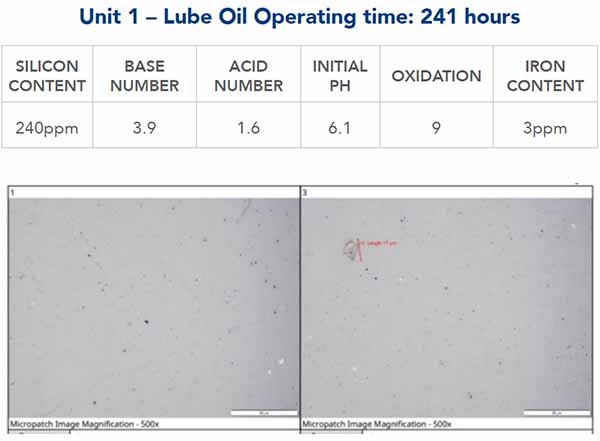
Micropatch testing results found contamination within the sample – 241 Hours
This example shows after a period of time with the new filters fitted, even though the silicon contents were similar (261ppm and 240ppm), the amount of visible abrasive contamination was significantly less – the filter unit had removed the majority of the abrasive particulate present. Additionally, the physical condition of the lubricant (base number, acid number etc.) remained well within the acceptable limits required by the OEM.
Visibility into Harmful Contamination
The inclusion of a micropatch test along with the standard analysis performed on these types of gas engine oils provides further information and visibility of the levels of abrasive contamination found within the system. This added insight could assist with increased monitoring of the conditions and harmful contamination levels determined in the samples.
Proven Savings
The power generation customer has utilized the additional micropatch testing on recent samples to better understand the condition of the oil, and with close monitoring and regular sampling, has extended the oil drain interval from a weekly change of around 150 hours, to an operating time of 650 hours on average. This has resulted in a significant decrease in the amount of oil changes required on each engine, as well as significant savings on the labor involved, and the associated disposal costs of the used oil from each change out.