In most industrial facilities, many lubricant application tasks are performed manually using either a grease gun, an oil can, an oil top-off container, or an aerosol spray.
Done correctly, manual lubrication can be an efficient and effective way to keep smaller equipment running reliably while also allowing us to inspect the asset easily at the same time.
But is there a better way? Sometimes, the answer is a resounding “yes” using single or multipoint automatic lubrication systems.
Automatic Lubrication Overview
Automatic lubrication systems range from simple single-point lubricators to large, complex multiline systems that lubricate hundreds of individual lubrication points. While some are designed just for grease, others can be used with either oil or grease, offering flexibility to accommodate various scenarios.
Automatic lubrication systems vary widely in design and layout. However, they all offer similar positives while having some very real negatives if they are not properly selected, installed, and maintained.
Perhaps the most significant benefit of automatic lubrication is ensuring that a bearing or other lubricated point receives the optimum amount of lubricant.
With manual lubrication, there is always a tendency to add too much initially, creating a period of oversupply.
Conversely, the bearing may be under-lubricated as we reach the prescribed relubrication interval. With automatic lubrication, we can add a smaller amount of lubricant over a shorter time interval, helping always to maintain an amount closer to the ideal quantity (Figure 1).
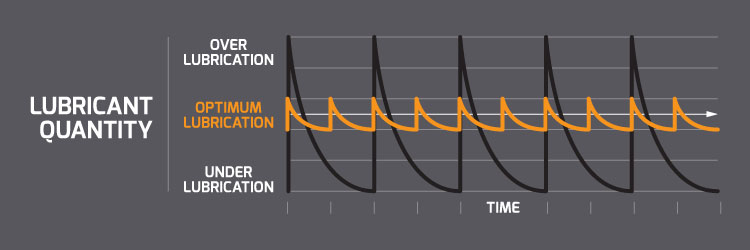
Figure 1: Optimized lubricant volume through automatic lubrication
Aside from optimizing lubricant volume, automatic lubrication can also help in applications where it is difficult to access the lubricated component safely during normal operation.
In mobile applications, using a central greasing system to lubricate pins and bushing can also help to purge contaminants out of the bushing. This is particularly useful in off-highway applications where high dust and dirt ingression can cause significant wear problems.
Perhaps the biggest downside to automatic lubrication is the false sense of security or a so-called “set-it-and-forget-it” mentality. Left unattended and uninspected, automatic lubrication systems can stop working, become plugged, or run empty.
Often, automatic lubrication systems need just as much and sometimes more maintenance to ensure proper operation.
Single-Point Automatic Lubricators
The simplest type of automatic lubricator is the single-point auto-luber (Figure 2). As the name implies, the automatic lubricator is connected to a single point, often a pillow block or other bearing housing. Single-point auto-lubers are commonly used with grease and are a good option where safety concerns preclude manual lubrication.
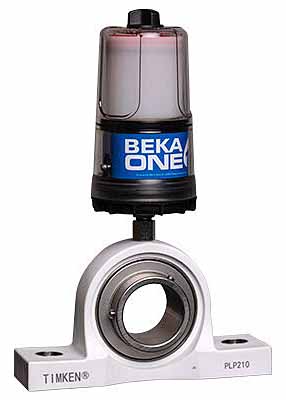
Figure 2: Example of a single-point automatic lubricator
Most units can be adjusted to vary the quantity and frequency of lubricant and come in different designs that use either a prefilled cartridge of grease or a grease zerk for refilling.
The simplest form of single-point lubricator uses a spring and plate design. By filling the reservoir, the plate compresses a spring. Over time, as the bearing rotates, the force created by the compressed spring in conjunction with the centrifugal force of the rotating bearing causes grease to be injected into the housing.
Spring-type auto-lubers are probably the most unreliable. Over time, the spring may weaken or break, or the force generated may be too low to inject grease into the housing effectively.
Likewise, changes in ambient temperatures can affect both the lubricant viscosity and grease consistency, resulting in under or over-lubrication.
In some applications, such as explosion-proof atmospheres, some auto-lubers use a chemical reaction to generate gas.
As the gas expands, the force causes a diaphragm to push grease into the housing. Like spring-activated auto-lubers, ambient conditions greatly influence how effective gas-activated auto-lubers work.
In cold climates, the reaction rate may be too slow to generate enough pressure, while in warmer temperatures, the reaction may work too well, injecting too much grease into the housing.
The most reliable single-point lubricators use a motor and positive displacement pump to inject the lubricant. These can be hardwired or battery-activated and generate hundreds of PSI of pressure. In some cases, they can also be connected to the plant’s PLC and DCS system to stop pumping if production shuts down.
Some single-point lubricators can be used with divider blocks to distribute lubricant to as many as sixteen lubrication points nearby. These can be particularly helpful in applications such as conveying systems where many grease-lubricated pillow block bearings can be found at the head or tail of the conveyor.
Multipoint Automatic Lubricators
Multipoint automatic lubrication systems are used for distribution across a wider area. Multipoint systems can be divided into two general categories: parallel (non-progressive) or series (progressive).
In non-progressive systems, a pump pressurizes a supply line with lubricant. Divider blocks connect the grease supply line to individual application points, which can be uniquely adjusted to dispense different quantities of oil or grease (Figure 3).

Figure 3: Example of a single-line parallel system
While parallel systems are inexpensive, they have some drawbacks, most notably a limited distance range, particularly in cold climates. At the same time, each injector needs to be periodically inspected and tested using a grease gun to ensure both the supply line and injector are functioning.
Progressive Multipoint Automatic Lubrication Systems
Single-line series or progressive systems are slightly more complex and use injectors that are connected in series.
The supply line is pressurized and primes and fires the first valve. This, in turn, primes and pressurizes the second valve, and so on Figure 4). Series systems can be used over a slightly longer distance since they carry more pressure to a single lubrication point.
The valve blocks are often automatically monitored for pressure and alarmed to ensure the system is still functioning. The biggest drawback for any series system is the progressive nature of the system, whereby any valve failure early in the series will result in no lubricant being dispensed further down the line.
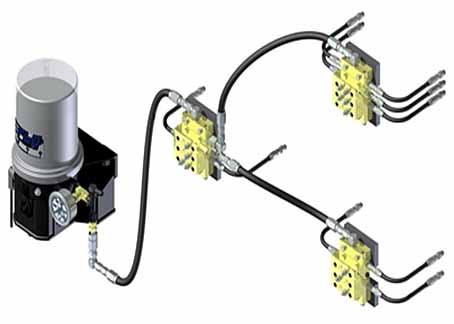
Figure 4: Example of a single-line series (progressive) system
In applications where oil or grease has to be dispensed over large distances or where high-viscosity oils or thicker greases are in use, it is common to use a dual-line parallel system.
Like the single-line parallel system, a dual-line system has two lines that pressurize and de-pressurize the system to feed multiple lubrication points through adjustable injectors.
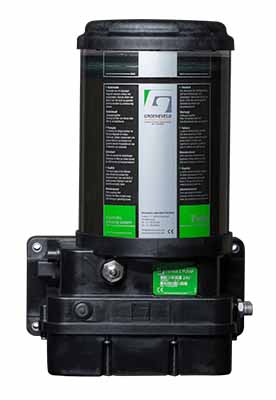
Figure 5: Example of a dual line parallel system for use with NLGI 2 grease
Automatic lubrication systems are not foolproof. They must be inspected, topped up, tested for obstructions or failed injectors, and properly maintained. Likewise, we need to consider the viscosity of the oil or thickness of grease to be used, particularly at very high or low ambient operating temperatures.
So, too, thickener type should be considered. Some thickeners have a higher bleed rate than others, causing grease to separate in a multipoint lubrication system. This can result in plugged lines and a lack of lubrication.
Used judiciously, the case of automatic lubrication is clear. Whether to ensure that just the right amount of lubricant is supplied at the right time or to help ensure that we don’t expose our lube techs to unnecessary safety risks, automatic lubricators can play an essential role in any lubrication program.
But they are not and never will be, an excuse for laziness or no maintenance. Choose them carefully, inspect them regularly, and never “set it and forget it.”