Developing a robust oil sampling program can be a rewarding effort when these essential foundations are put in place:
- Meticulously selecting equipment to monitor with oil analysis, using a suitable criticality assessment.
- Setting the initial oil sampling frequency for each selected piece of equipment. For this objective, ISO 14830 recommended FMSA analysis, which shall be carried out in accordance with ISO 13379-1, to determine initial sampling and inspection periods [1].
- Careful selection of an oil analysis lab, specifying the appropriate analysis slates, and ensuring the delivery of independent and accurate results.
- Providing thorough training for personnel involved in the oil sampling process while fostering awareness of the importance of collecting only representative equipment samples. Establish an internal procedure to help ensure oil samples are truly representative.
These steps are crucial for ensuring the oil sampling program’s success and initiating the next phase of the oil analysis program, which focuses on using the results to monitor equipment and lubricant condition.
However, it’s essential to understand that simply carrying out these steps doesn’t guarantee successful implementation.
Oil sampling becomes part of routine operations only when it consistently runs smoothly according to best practices.
This article does not focus on implementing an oil sampling program within an oil analysis strategy. Instead, it assumes the four key components are already in place and centers on effectively managing the oil sampling program to ensure it meets its intended objectives.
Below I introduce four performance metrics for managing an efficient oil sampling program, covering the process from sample extraction to receiving the oil analysis report.
These metrics include monitoring adherence to the sampling schedule, minimizing delays before sending samples to the lab, tracking the time from sample collection to lab delivery, and assessing the lab’s turnaround time for testing and report release.
Sampling Schedule Compliance
Sampling Schedule Compliance could be automatically obtained using a Computerized Maintenance Management System (CMMS).
In its absence, the calculation can be done monthly by dividing the number of oil samples drawn during the month (or oil analysis reports received) by the forecasted number of samples based on the established sampling frequency during the program implementation.
Oil Analysis Data Management Systems (DMS) have become a key element of the Oil Analysis Service offered by many labs today. A standout feature of these systems is the ability to create an oil sampling schedule and user reminders via email or notifications.
They also enable tracking the completion of scheduled sampling tasks. Additionally, there are various specialized software options designed for comprehensive lubrication management.
These solutions, whether from LAB DMS or commercial software, provide a valuable alternative, especially for smaller companies without a CMMS.
In his book Maintenance and Reliability Best Practices [2], Ramesh Gulati presented examples of maintenance and reliability benchmarks; the typical word class of schedule compliance is over 90%. Similarly, the minimum adherence for oil sampling PMs is 90%.
Waiting Time for Shipping
Through this metric, the objective is to measure the duration between the moment a sample is drawn from the equipment and when it is picked up for conveyance to the laboratory.
The waiting time for shipping can vary, ranging from zero to several days, depending on the contract between a company and its oil analysis service provider. Some companies opt for full outsourcing, including sampling, sample shipment, and analysis at the laboratory.
In such scenarios, the oil analysis lab or service provider delegates an inspector or technician to extract samples from the customer’s equipment and promptly transport them to the laboratory for analysis immediately after sampling.
In contrast, some companies simply extract and prepare samples from their equipment for collection. The sampler leaves the samples in the mailroom, and collection is handled by the lab or a specialized transport company.
Contracts may specify collection schedules based on sample quantity or batches. If sampling routes aren’t optimized to meet the minimum sample threshold, customers may delay shipment until more samples are collected or incur additional costs.
I recently came across a noteworthy example of effective coordination between a laboratory and a transportation company. In this arrangement, the lab has partnered with an international transportation company.
As part of this collaboration, the lab’s customers are granted access to the transportation company’s platform, allowing seamless sample pick-up scheduling. Undoubtedly, this service incurs a cost, but its tangible benefits significantly enhance the overall efficiency of the process.
In all cases, minimizing the waiting time for shipping is essential.
Shipment Time
This metric measures the time between collecting the sample from the site and physically receiving it at the lab facilities.
Several factors contribute to the delay in achieving the agreed-upon shipment time for oil samples, including customer-related issues, challenges associated with the transportation company, and unforeseen natural events.
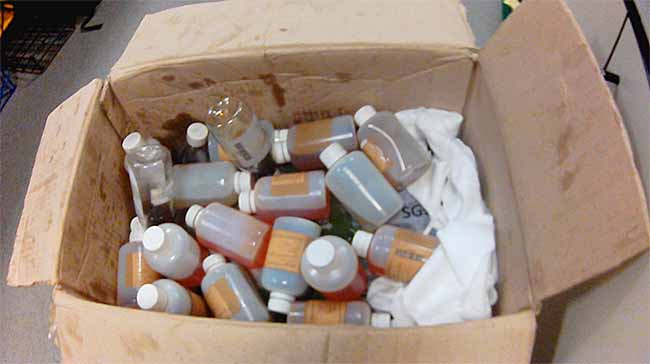
The oil samples in this picture are not well-sealed or adequately packaged. This led to leaks in the samples, which affected the readability of the labels. Additionally, the quantity of oil in each sample does not seem to be enough to conduct the required tests, and the samples are no longer representative.
Most oil sample transportation issues on the customer side stem from improper storage and packaging. Customers must ensure samples are securely sealed and properly packaged to prevent leaks.
Leaks can lead to various problems, including cross-contamination, loss of label identification, and insufficient sample quantities for analysis, ultimately affecting the sample’s representativeness.
Additionally, customers play a crucial role in speeding up the process by declaring that their oil samples have no commercial value and including Material Safety Data Sheets (MSDS) with the shipment. Omitting this vital information can result in significant delays at customs, especially for international shipments.
Transportation company-related factors also contribute significantly to report release delays. Strikes within transportation companies and unforeseen traffic accidents can disrupt the timely movement of samples from one location to another.
These incidents not only introduce unexpected delays but also exacerbate the challenges posed by customer-related issues.
Moreover, other external elements beyond the control of customers and transportation companies add another layer of complexity. Bad weather conditions, for example, can further impede the transportation process, causing delays in the arrival of samples at the analysis facility.
The interplay of these factors makes it crucial for companies to establish contingency plans and collaborate closely with reliable transportation partners to minimize disruptions and ensure more efficient and timely deliveries.
Laboratory Turnaround Time
Laboratory turnaround time refers to the duration elapsed from receiving the sample at the laboratory to releasing the report to the end user. This includes testing all relevant parameters, completing the diagnosis, and making the report accessible online or via email.
In certain instances, labs may issue a preliminary report while awaiting the completion of testing the full parameters requested. In this case, the laboratory turnaround time is to be measured from the initial reception of the sample until the delivery of the final report.
Various factors, including laboratory-related and customer-related challenges, contribute to the delays experienced in meeting the agreed turnaround time for report release.
Some laboratories lack automated equipment capable of processing multiple samples simultaneously, leading to inefficiencies in the analysis process.
Additionally, some labs may not be fully equipped to process the required analysis slate, necessitating the subcontracting of specific tests. This subcontracting introduces additional complexities and time constraints, extending the turnaround time.
Additionally, various operational issues within the laboratory can arise, such as equipment downtime, calibration difficulties, accidents, or shortages of solvents or reagents. Retesting, sometimes necessary for result validation, further delays the report generation process.
Challenges often stem from the sample registration process on the customer side. Delays can result from incomplete identification or poorly labeled samples, highlighting the need for precise and detailed documentation.
Leaks can also cause label erasure, requiring prompt communication with the customer to retrieve accurate information and maintain the integrity of the analysis results.
Many labs include mobile applications in their oil analysis service packages to address these challenges. Each sample bottle is given a unique code, entered at the moment of sampling using the mobile app. This allows instantaneous sample registration on the lab Data Management System (DMS) before the sample arrives at the lab registration desk.
When the bottle arrives at the lab, the bar code is entered into the Lab DMS, extracting all associated data. This streamlined process will allow the lab to reduce the time spent on sample registration and enable quick integration of samples into the workflow.
Why Should the Time Between Sampling and Lab Registration Be Minimized?
Retaining oil samples onsite for the required duration poses no issue if they are securely sealed, adequately packaged, and protected from contaminants such as water, dust, intense light, or radiation. Additionally, leaving sufficient ullage is essential for proper sample preparation and agitation, ensuring that any particles settled on the bottle’s surfaces are resuspended in the sample.
In these conditions, if the sample is representative initially, it will remain representative but representative of the existing oil in the equipment at the moment of sampling. This is similar to capturing a screenshot of equipment status and lubricant condition at the moment of sampling.
Prolonged waiting times before dispatching samples—and consequently, delayed reports—can hinder timely awareness, delaying interventions in response to rapidly developing potential failures. This is especially critical for key components operating in harsh environments with rapid changes, such as heavy-duty engines.
Using online sensors or establishing onsite oil analysis capabilities can deliver quick results but presents challenges related to detection limits, repeatability, and reproducibility. Even with reduced frequency, regular analysis at a commercial lab remains essential. However, minimizing the time between sampling and receiving the analysis report is critical.
References
[1] ISO 14830-1: 2019-12, Condition monitoring and diagnostics of machine systems – Tribology-based monitoring and diagnostics – Part 1: General requirements and guidelines, P 4.
[2] Maintenance and Reliability Best Practices, Second Edition, Ramesh Gulatti, Chapter 1, P 6.