Microdieseling is a term often associated with changes in lubricant color and the formation of harmful byproducts within lubricated systems. It occurs when microbubbles of air (smaller than 5 microns) in the lubricant transition from a low-pressure environment to a high-pressure one, triggering implosions.
The size of these bubbles plays an important role, as these micro-explosions not only degrade the oil but can also damage machinery components where they occur.
The process of how the compression of air bubbles implodes in the high-pressure zone is very well defined, and it is possible to calculate, at least theoretically, the temperature at which this phenomenon can easily exceed 1000°C.
Microbubbles imploding at over 1,000°C cause more damage than meets the eye.
The best-known case of this phenomenon is OceanGate in 2023, which had to withstand around 4000 atmospheres of pressure when imploding.
Lubricated systems such as turbines or hydraulic systems should suffer from this phenomenon at some point in their life in service, since they have air in the lubricant due to the operating conditions. A new turbine oil has around 8% air, while an oil in service in areas such as the reservoir can reach a concentration of 18%.
Microdieseling: cause or effect?
In lubricated systems such as turbines or hydraulics, Microdieseling is the effect caused by the partial or total degradation of an additive, a very special one…
Let’s look at a power generation plant case study:
Day 1: Everything was going well!
A high percentage of gas turbine oils work with groups I and II, mainly because of the cost-benefit ratio these provide. These oils can reach specific areas of high temperature that exceed 100°C. In these areas, the lubricant suffers a lot, but we are talking about thousands of liters in the system—8, 12, or 20 thousand liters. In this case, the temperature and temperature variations do not have an immediate effect on the oil; it takes some time.
Day 2: Change the filters!
For some reason, the filters of both turbines were clogged a couple of days apart, a strange coincidence, of course.
Something is already out of the ordinary, and the maintenance team has begun to pay attention to this situation. During their research, they observed that the temperatures of both oils have increased in recent months, still below the recommended limits to put on standby the group but above normal. Something is happening, it’s already obvious. After a more in-depth check of the lubrication circuit, it was observed that there is also a material similar to that of the filters in other areas of the system, especially in low areas, in discharge pipes, and in the tank.
Day 3: The oil goes dark!
For some reason, the oil began to lose the typical color it had to acquire an increasingly darker tone. The images below show the color difference between both oil samples.
Laboratory analysis showed an advanced degradation (AN) problem.
Day 4: Filtering the oil is the solution!
The matter found in the filters and the low and cold areas of the system are lacquers or sludge, and the presence of varnishes in other areas was also evidenced. The decision was immediately made to install a varnish filter by choosing a supplier who ensured their system could remove those unpleasant byproducts without any problems.
The lab reports didn’t reveal anything unusual – you can’t ask for much more for a $75 analysis – so no further investigation was done. After 3 months of filtration, the consumption of filters from the system and organic matter removal equipment (varnishes, sludge, etc.) exceeded the 5-year filter budget.
Turbine Oil Temperature
Day 5: Change of supplier and imminent stoppage!
Degradation byproducts continued to clog the filters, and the filtration system was replaced with another supplier. The problems remained, and the shutdown of both turbines was imminent. The costs of changing the oil, not only the volume but also the logistics of the change, greatly impacted the plant’s budget.
Due to the number of byproducts present, chemical and physical flushing had to be done on the entire system. In total, there were 16 days of unscheduled stoppage. Imagine the production losses!
Advanced Analysis Techniques for Identifying Microdieseling
The trend towards a dark color of turbine oil is mainly due to an air compression problem in high-pressure areas, yes, Microdieseling!
Air is usually just one piece of this reaction puzzle, so blaming excess air in the lubrication system alone is not the solution.
Air in the oil is a piece of the puzzle, but not the whole story.
The vast majority of turbine mineral oils have in their formulation a modified silicone additive in a base that can be ester or ether, whose primary function is to break the wall of the bubbles, minimize their presence, and eliminate the accumulation of air bubbles. This molecule comprises a silicone backbone (polydimethylsiloxane) with branches or modifications of polyether or polyester side chains.
This hybrid structure allows the compound to retain the unique properties of silicones (such as low surface tension and thermal stability) while becoming more compatible with the hydrocarbon chain. Compared to traditional silicones, the modified one offers better compatibility at a lower concentration, it is dissolved, which makes it present throughout the fluid. This makes it preferable when robust defoaming performance is needed without compromising system stability and uniformity.
Modified silicone additives are the hidden heroes—and villains—in turbine oils.
But like any compound, this one is also susceptible to degradation. The main cause of degradation is due to the reduction or loss of its thermal stability caused by extreme temperature peaks.
Their degradation generates fragmented polymers, esters, aldehydes, organic acids, and very low concentrations of silicates. One of these elements is the key to identifying Microdieseling problems.
Microdieseling Analysis, Control, and Recommendations
Traditional analyses on turbine oils cannot identify this failure mode until it is well advanced. In general, the problem is evident when the concentration of the Acid Number (AN) exceeds >3 times that of the original oil, when the color gives away the problem, with an increase in temperature, or when the filters are changed more frequently.
Late tests, such as the determination of varnishes, also known as MPC, are very close to the end of the P-F curve of this type of failure. On the other hand, the concentration of silicates or silicon oxides is so small that it goes unnoticed by atomic emission spectroscopy, so the silicon element is not an indicator of failure.
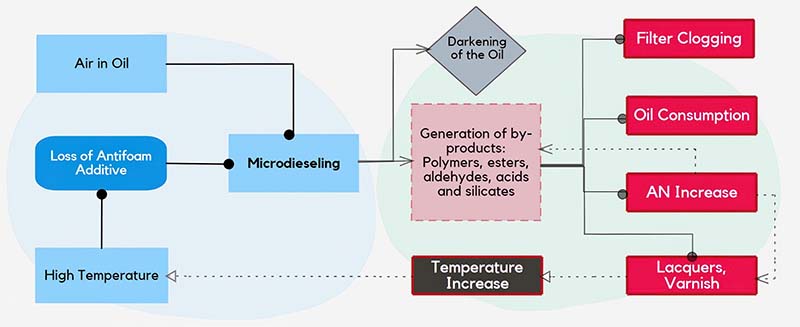
Microdieseling Degradative Process
The only way to identify both the concentration of this additive and its degradation and the formation of byproducts is achieved through the analysis of Fourier Transform Infrared Spectroscopy (FTIR). This is the only laboratory technique that allows the chemical cause of Microdieseling to be accurately identified.
However, this analysis requires particular knowledge and a lot of experience in the FTIR technique applied to industrial oils, only a couple of laboratories and individuals worldwide can determine this problem, so it is very important to choose your lubricant analysis provider wisely.
One last comment: If your oil is suffering from a Microdieseling problem, do not waste time looking for the source of air entry into the system. Identify the area or hot spots that have caused the degradation of the aforementioned additive; that is the real cause of the problem.