What is Lubricant Foaming?
Lubricant foaming is a deceptively complex phenomenon often dismissed as mere surface bubbles on top of oil reservoirs. Yet seasoned lubrication engineers and tribologists understand the critical threat foaming poses to lubricant performance and equipment reliability.
In this article, we delve into the mechanisms behind foam formation, its adverse impacts, standardized testing methods, antifoam additive technologies, and actionable solutions to address this prevalent industry challenge.
Understanding Foam vs. Air Release
To effectively manage lubricant foaming, it’s crucial to differentiate between foam properties and air release characteristics. Air release refers to the lubricant’s ability to rapidly separate entrained air bubbles and release them, thereby preserving oil integrity. Foam formation, however, involves the stabilization of air bubbles at the oil surface. Imagine a pint of beer—bubbles within the beer represent air release behavior, while the foam atop symbolizes lubricant foaming (See Figure 1).
This is what it looks like if you are a drop of oil flowing through a return line from a turbine bearing, back to the reservoir. The bright, flashing lights are air bubbles all around you. If the turbine oil has poor foaming performance, it’s easy to see how easy it is for foam to develop!
Each phenomenon impacts equipment differently. Entrained air compromises lubrication effectiveness, accelerates oxidation, enhances compressibility, induces microdieseling, and contributes to cavitation. Particularly problematic in hydraulic systems, this can lead to spongy responses and reduced valve precision. Conversely, foam on top of lubricant reservoirs disrupts lubricant film consistency, hampers heat dissipation, and presents safety risks if an overflow occurs.
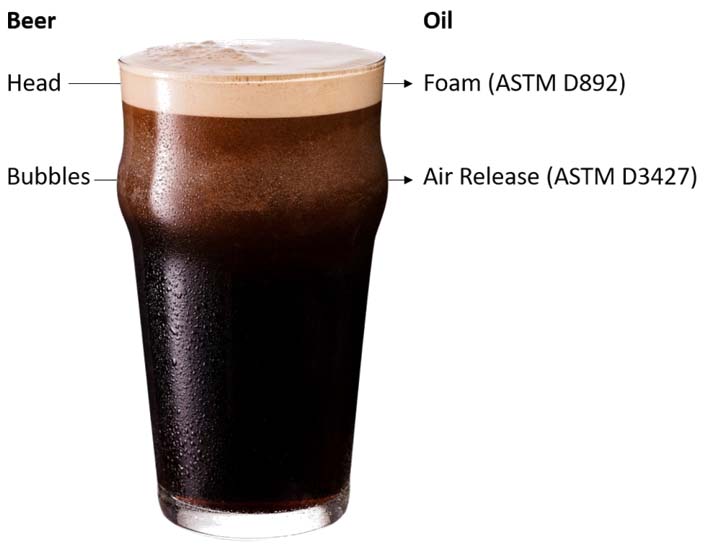
Figure 1: Foam vs Air Release
Causes of Foam Formation
Lubricant foam arises primarily from the entrapment and stabilization of air bubbles within the fluid. There are several potential causes, but foam is generally initiated by either a mechanical or chemical reason.
Mechanical Reasons for Foam
Mechanical agitation, such as rapid flow rates, pump operation, gear mesh interactions, seal leaks, and bearings agitation, may introduce air bubbles into the oil. It can be particularly challenging for these bubbles to dissipate in high-viscosity fluids (especially at low temperatures), as these fluids impede efficient air release.
Poor reservoir design can also contribute to lubricant foaming due to deficient baffling and insufficient residence time for air to settle out of the oil. Additionally, if the return line is positioned above the surface of the lubricant, significant splashing may occur, resulting in foam. Finally, systems that are under vacuum with a degasification or demister system will also be more prone to foam generation.
Chemical Reasons for Foam
Contaminants are a common cause of foam formation. Moisture and degraded additives may reduce the oil’s surface tension, allowing the bubbles to form more easily and making the foam more stable. Particulate, soot, or dispersants may also act as foam-stabilizing nucleation sites.
Oxidation byproducts are also polar, which reduces surface tension and increases foaming tendencies. Some types of contaminants may form films at the air-oil interface, thereby increasing the interfacial tension of the fluid and making it more difficult for bubbles to collapse.
Foam After an Outage?
It is common to see foam occurring after an outage, as human interaction with the lubricant system always introduces risk. Sometimes, maintenance crews walking over your equipment during downtime may inadvertently crack a pipe connection leading to a pump, which can introduce new sources of air. Or, contaminants may inadvertently enter the system during outages, causing chemical changes in the oil and creating more opportunities for foam.
The first step in diagnosing a foam issue is to determine if it is a mechanical issue or a chemical issue. Fortunately, this can be easily accomplished by performing oil analysis tests.
Standardized Foam Testing Methods
Determining the foaming tendencies and stability in used oil analysis is standard in most commercial laboratories by following one of the three tests:
ASTM D892 (or DIN 51566)
This test was developed in the mid-20th century. It measures foaming tendencies and foam stability, performed in three sequences: 24 °C, 93.5 °C, and then again at 24 °C. In each sequence, air is blown through the oil for 5 minutes, and foam is measured immediately after (foam tendency) and again after 10 minutes (foam stability).
The results are measured in mL and separated by tendency/stability for each sequence. For example, 450/0 means that 450 mL of foam was initially generated (tendency) and 0 mL of foam remained after 10 minutes (stability).
ASTM D6082: High-Temperature Foaming Characteristics
This testing method was developed to measure foam in hotter operating environments, as the test is performed at 150°C. The test is interpreted in a similar way to D892. The first value represents the foam tendency, measured in mL after 5 minutes of air blowing, and the second value represents the foam stability, also measured in mL after 10 minutes of rest.
Flender Foam Test, ISO 12152:2002
The Flender Foam Test measures foaming behavior (formation and stability) of lubricants under mechanical stress at elevated temperatures, simulating the conditions found in Flender gearboxes. The fluid is stressed in a specialized gear test rig (conveniently named Zahnradversuchgerät!) at 90°C for 5 hours with a gear speed of 1,450 rpm.
It’s typically used on ISO VG 150 – 320 industrial gear oils. The results are typically reported as Foam Formation Height (mm), Foam Collapse Time (secs), Air Entrainment (visual/subjective), and Overflow or Oil Loss (pass/fail).
Effective Antifoam Additives
New oils are typically formulated with antifoam additives to minimize foam stability. Although multiple chemistries have been used as foam inhibitors, there are two major categories in most industrial lubricants.
Silicone-Based Antifoam Agents (Polydimethylsiloxane or PDMS)
Silicone-based antifoam additives or silicone oil dispersions exist in lubricant formulations as finely dispersed droplets. These droplets are typically about 5 microns in size and offer efficiency at low concentrations. However, in close-tolerance or high-pressure systems that require clean fluids, silicone antifoam agents are susceptible to filtration. This is why we no longer see this additive used in hydraulic or turbine applications.
Have you ever noticed that when you rapidly fill up a soda in a convenience store, there’s seldom foam? Even though the same soda will create all sorts of foam when you open a can or bottle? This is because soda dispensing systems also inject a small amount of PDMS foam inhibitor into the carbonated water or syrup line. It’s incredibly effective, just like it is in a lubricant, as long as it’s not filtered out.
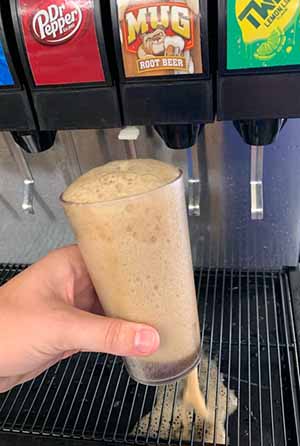
Figure 2: If the soda machine doesn’t inject PDMS (Silicone) foam inhibitor into the soda stream.
The second challenge with silicone foam inhibitors is their adverse reaction to the fluid’s air release properties. In 1982, the German Utility Industry published a document warning, “Although there are silicone additives which suppress the foaming tendency, caution is advised when using them, as these additives often have a very unfavorable effect on the air release value”.
Polyacrylate Defoamers
Polyacrylate defoamers have a lesser impact on the surface tension of the fluid compared to silicone foam inhibitors. Although they may not be as effective at reducing foam, they have a much less severe impact on air release properties. They are also more soluble in the fluid and, unlike silicone foam inhibitors, cannot be removed through filtration. This is the technology of choice in applications where clean oils and low air release values are desired.
Measuring the content of silicone foam inhibitors can be done by elemental spectroscopy. However, if dirt or sealant enters an in-service oil, assessing the foam protection by elemental spectroscopy is impractical. Unlike silicone foam inhibitors, directly measuring the health of silicone foam inhibitors for in-service lubricants is not practical for commercial oil analysis labs.
Practical Solutions for Foam Management
Managing foam can be a challenge. Determining the root cause of foaming is always preferable, starting with a diagnosis of whether it is a chemical or mechanical issue. However, even after extensive testing, the cause of high foam levels may remain unclear.
Below are a few suggestions on different strategies that can be effective.
Operational Optimization: Reservoir design improvements, such as enhanced baffling to ensure sufficient dwell time for air separation. System venting and deaeration can be effective.
Filtration: Removes contaminants that stabilize foam. Be sure to use filters rated at 5 microns or higher when filtering oils with silicone-based foam inhibitors.
Proactive Maintenance: Regular fluid-level checks will help maintain the fluid at the recommended level, minimizing agitation. Sealing integrity checks to prevent external air ingress.
Keep Systems free of Sludge and Varnish: Regularly test for varnish using tests such as the MPC test (ASTM D7843). Consider using a varnish mitigation system or solubility-enhancing technology to provide long-term protection from deposits. This will help minimize foam.
Strategic Antifoam Additive Management: In some cases, with sufficient upfront testing, the addition of antifoam agents may provide temporary relief. This should be considered carefully, along with sufficient laboratory simulation testing and the involvement of lubricant formulation experts in the process.
Real-World Case Study: Risks of Antifoam Additive Mismanagement
A power plant recently had a foaming issue in its turbine oil, as can be seen in Figure 3.
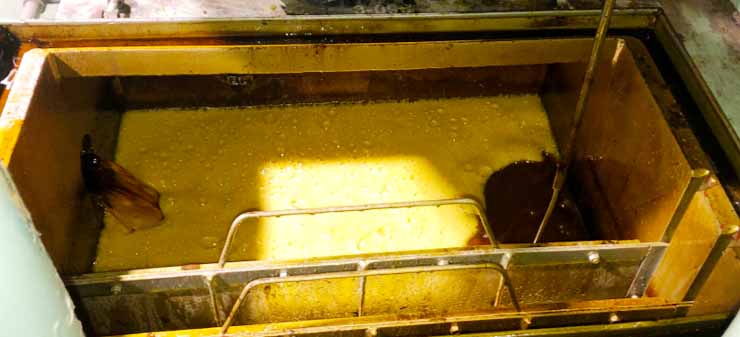
Figure 3: Turbine oil foaming issues in a power plant.
The power plant performed the D892 foam test, revealing that it exceeded the suggested critical limit of 450 mL. The original foam and air release values are shown in Figure 4.
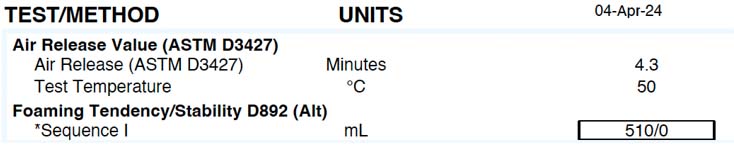
Figure 4: Power Plant with poor turbine oil foaming values.
The power plant added silicone foam inhibitor to the turbine oil. (Even though this foam inhibitor chemistry is not recommended by turbine OEMs.) However, the impact on the fluid’s air release values was significantly more severe than the original foaming issue, creating an even greater operational risk and rendering the oil unusable.
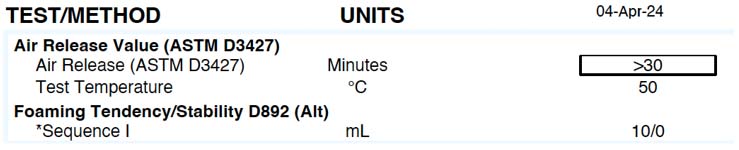
Figure 5: The same turbine oil treated with PDMS foam inhibitor.
Although treating foaming fluids with tank-side additives can sometimes be effective, caution should be exercised before attempting to do this on-site, including extensive upfront testing.
Final Takeaways
Lubricant foaming poses a significant challenge, affecting lubrication efficiency, equipment performance, and operational safety. Armed with insights into foam mechanisms, robust testing methodologies (ASTM D892, ASTM D6082, ISO 12152), and informed additive selections, one can deploy effective foam-management strategies.
Strategic system design, meticulous additive management, proactive maintenance, minimizing varnish deposits, and informed oil analysis form the foundation for mitigating foaming, safeguarding equipment reliability, and extending operational life.
References
- ASTM D892 – Standard Test Method for Foaming Characteristics of Lubricating Oils.
- ASTM D6082 – Standard Test Method for High Temperature Foaming Characteristics of Lubricating Oils.
- ISO 12152:2002 – Lubricants — Determination of foaming and air release characteristics of lubricating oils — Flender foam test
- DIN 51566 – German Standard for Foaming Characteristics of Lubricating Oils.
- Bhushan, B. (2013) – Introduction to Tribology. Springer.
- Totten, G. E., Westbrook, S. R., & Shah, R. J. (Eds.) (2017) – Fuels and Lubricants Handbook: Technology, Properties, Performance, and Testing. ASTM International.
- Verlags – und Wirtschaftsgesellschaft der Elektrizitätswerke M. B. H. (VWEW), (1982) Stresemannallee 23, 6000 Frankfurt/Main, ISBN-3-8022-0045-4 (Translated from German)