Gears are used in all aspects of life, from bicycles to tiny watch gears, car transmissions, and even highly specialized surgical equipment. Gears keep the world moving. However, when they move, they often rub against each other, and if this friction is not managed, it can cause wear and eventually lead to significant damage or failure. This is where gear oil makes a difference.
In this article, we will explore the various types of gear lubricants, their composition, how they degrade, some storage and handling tips, and what the future holds for these types of oils.
There’s More Than One Type of Gear?
If you’re familiar with gears, you know that despite the standard emoji keyboard, more than one type of gear exists. There are several types of gears, each suited for various applications. As such, each application will have varying environmental conditions, which will require specialized lubricants to reduce friction and wear.
One of the main operational conditions for gears is the transfer of torque. Even when torque is transferred, gears will have sliding and rolling contact, leading to frictional losses and heat generation. Therefore, the lubricants selected for these applications must be able to significantly reduce these frictional losses and cool the gears.
As per (Pirro, Webster, & Daschner, 2016), several types of gears can be classed into three groups based on the interaction of the teeth of these gears and the types of fluid films formed between the areas of contact:
- Spur, Bevel, Helical, Herringbone, and spiral bevel
- Worm gears and
- Hypoid gears
Figure 1 shows some of the types of gears which exist.
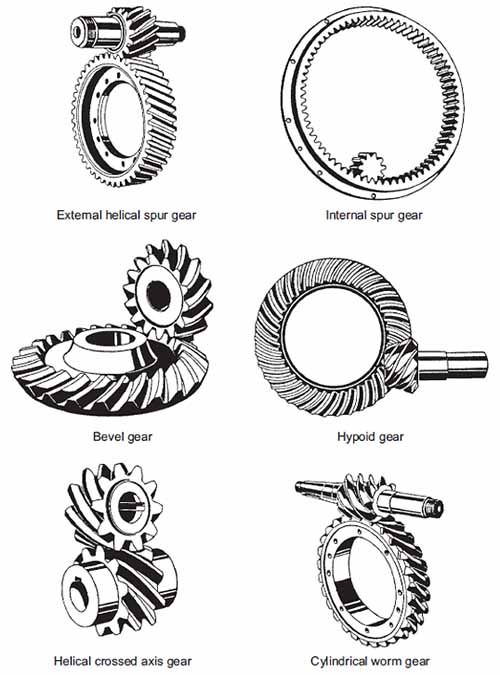
Figure 1: Different types of gears according to (Mang & Dresel, Lubricants and Lubrication – Second Edition, 2007) Chapter 10
It must be noted that hypoid gears transmit motion between nonintersecting shafts at a right angle. Additionally, there is a difference between rolling and sliding.
Rolling indicates continuous movement, whereas sliding varies from a maximum velocity in one direction at the start of the mesh through zero velocity at the pitch line and then back to maximum velocity in the opposite direction at the end of the mesh, as seen in Figure 2.
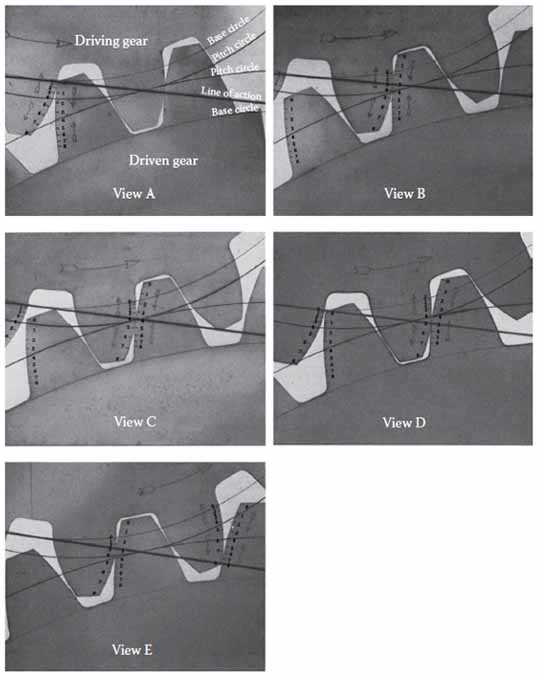
Figure 2: Meshing of involute gear teeth. These photographs show the progression of rolling and sliding as a pair of involute gear teeth (a commonly used design) pass through mesh. The amount of sliding can be seen from the relative positions of the numbered marks on the teeth adapted from (Pirro, Webster, & Daschner, 2016), Chapter 8.
According to Mang, Bobzin, and Bartels (Industrial Tribology—Tribosystems, Friction, Wear and Surface Engineering, Lubrication, 2011), hypoid gears require heavily loaded lubricants. These should have high oxidation stability, good scuffing, scoring, and wear capacity, as the tooth contacts have a high load.
The lubricant must also have a high viscosity at operating temperature such that the formed film can sufficiently support the load while cooling the gears.
Conversely, hydrodynamic gears such as torque converters, hydrodynamic wet clutches, or retarders require high oxidation stability characteristics but do not need good scuffing or scoring load capacity characteristics. Unlike hypoid gears, hydrodynamic gears experience viscosity-dependent losses, so they must have a lower viscosity at operating temperature.
According to (Mang & Dresel, Lubricants and Lubrication – Second Edition, 2007), there are some frequent failure criteria for gears and transmissions, including:
- Extreme abrasive wear
- Early endurance failure, fatigue of components in the form of micropitting and pitting
- Scuffing and scoring of the friction contact areas
Continuous abrasive wear is usually observed at low circumferential speeds and during mixed and boundary lubrication. Typically, continued wear can cause damage that extends to the middle sector of the tooth flank. Understandably, lubricants with a high viscosity and a balanced quantity of antiwear additives promote a higher tolerance to wear.
Micropitting can be observed on tooth flanks at all speed ranges. Those with rough surfaces are prime candidates for micropitting. Typically, this develops in negative sliding velocities or the slip area below the pitch circle.
Usually, microscopic, minor fatigue fractures occur first, which can lead to further follow-up damage such as pitting, wear, or even tooth fractures. A lubricant with a sufficiently high viscosity and a suitable additive system can help reduce this type of gear fatigue.
At predominantly high or medium circumferential speeds, scuffing and scoring of the tooth flanks occur, and the contacting surfaces can weld together for a short time. Due to the high sliding velocity, this weld usually breaks, causing scuffing and scoring.
Typically, this damage is seen on the corresponding flank areas at the tooth tip and root, which experience high sliding velocity. In this case, lubricants with higher EP (Extreme Pressure) additives can help reduce this damage.
According to (Ludwig Jr & McGuire, March 2019), the type of gear can aid in determining the most appropriate industrial gear oil. The following table is an adaptation from the article:
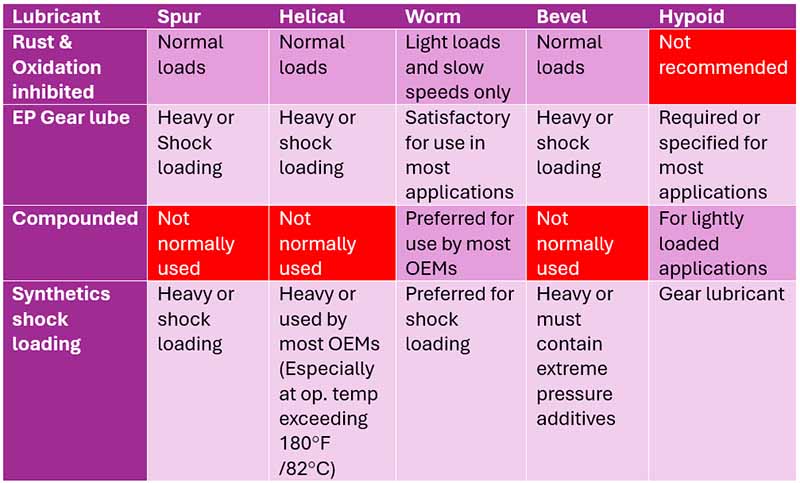
Table 1: Gear type and appropriate lubricant adapted from (Ludwig Jr & McGuire, March 2019)
As per (Mang & Dresel, Lubricants and Lubrication – Second Edition, 2007), transmission gears can be broken down into two main types: those with a constant gear ratio and those with a variable gear ratio. These can be seen in Figures 3 and 4 below.
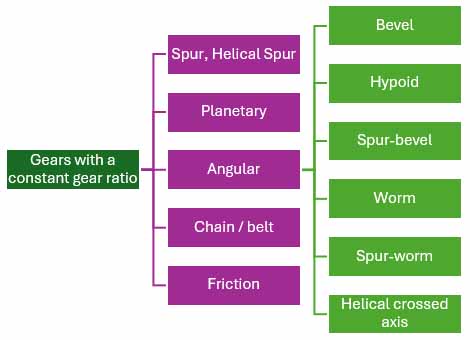
Figure 3: Gears with a constant gear ratio adapted from (Mang & Dresel, Lubricants and Lubrication – Second Edition, 2007), Chapter 10
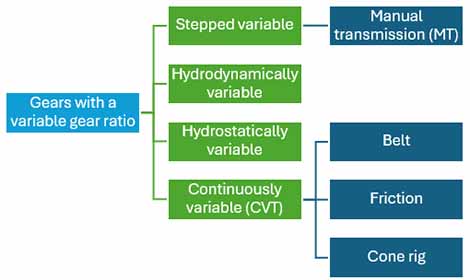
Figure 4: Gears with a variable gear ratio adapted from (Mang & Dresel, Lubricants and Lubrication – Second Edition, 2007), Chapter 10
Gear Oil Characteristics and Naming Systems
From the information covered thus far, we can appreciate that gear oils need to accommodate many changes to their environment. A few characteristics stand out when looking at industrial gear oils (Mang, Bobzin, & Bartels, Industrial Tribology—Tribosystems, Friction, Wear and Surface Engineering, Lubrication, 2011).
These include viscosity-temperature, Fluid Shear Stability, Corrosion and Rust Protection, Oxidation Stability, Demulsibility and Water Separation, Air release, Paint Compatibility, Seal Compatibility, Foaming, Environmental, and Skin Compatibility.
Depending on where you are in the world, you may use a different system to classify gear oils. The ISO Viscosity grade system is used internationally, but the AGMA (American Gear Manufacturer’s Association) system is used in the Americas and some parts of Asia. A chart can be used to move that across these grading systems, as shown below in Figure 5.
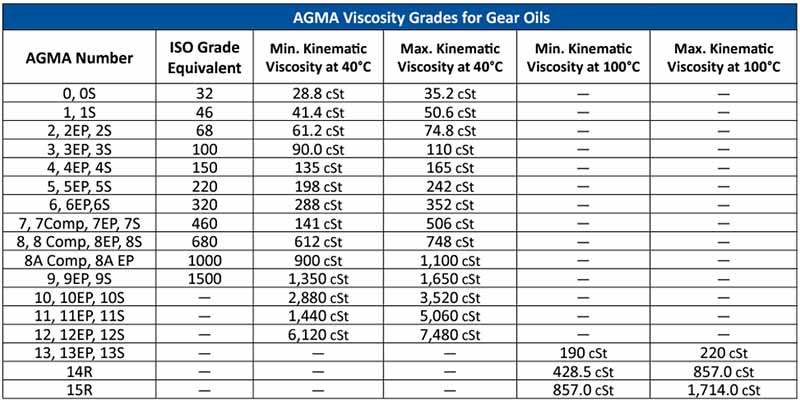
Figure 5: Various gear oil grading systems as adopted from (Sander, 2020)
As per (Sander, 2020), the AGMA numbers have some particular meanings as stated:
- No additional letters (only a number) – Contains only R&O additives
- EP – Mineral oil with Extreme Pressure additives
- S – Synthetic gear oil
- Comp – Compounded gear oil (3-10% fatty or synthetic fatty oils)
- R – Residual compounds called diluent solvents which reduce the viscosity to make it easier to apply
Another rating that is seen a lot is the CLP rating. This is a German oil standard defined by ASTM DIN 51517-3, in which the test requirements to meet the CLP specification are documented.
This DIN standard covers petroleum-based gear lubricants with additives designed to improve rust protection, oxidation resistance, and EP protection. Some typical classifications seen are CLP-M (which represents mineral gear oil), CLP HC (which represents synthetic oils [SHC, PAO, POE]), and CLP PG (which represents polyglycol PAGs), according to (Santora, 2018).
There are three main DIN 51517 classifications as per (Rensselar February 2013), namely;
- DIN 51517 CGLP – contains additives that protect from corrosion, oxidation, and wear at the mixed friction spots and additives that improve the characteristics of sliding surfaces
- DIN51517-3 CLP – contains additives that protect against corrosion, oxidation, and wear in the mixed friction zone
- DIN 51517-2 CL – contains additives that protect against corrosion and oxidation suitable for average load conditions
The above are some of the more prevalent naming systems for industrial gear oils, and they are found on most gear oils globally.
Degradation
The first set of additives to decrease in gear oils is often the antiwear or extreme pressure additives. This is no surprise, as these oils are subjected to high levels of wear and must withstand extreme pressures. One can also notice a decline in the rust and oxidation additives or even a change in the air release values.
All these properties significantly impact how a gear oil functions. As such, they should be monitored when establishing the health of the oil.
When monitoring the health of these lubricants, some guidelines can be utilized. If there is a change in viscosity of either ±10%, one should look for any other correlating changes.
Typically, if the viscosity increases by 10%, we’re looking at increases in wear metals or the risk of oxidation and development of some deposits in the oil or even contamination of the oil with some water. However, for a decline of 10%, one can expect some form of contamination, typically fuel or another substance which will thin out the lubricant.
The lubricant’s warning levels for wear metals will vary depending on the manufacturer/OEM. However, any consistent rise in wear metals indicates that some component on the inside of the equipment is slowly wearing away.
Gear Oil Storage and Handling
Similar to most oils, gear oils should be stored in a clean and dry space. Often (especially in the past), these gear oils see a settling of the additives to the bottom of the container, indicating a slightly shorter oil life span than other lubricants. However, this is no longer a highly occurring incident with the advancements in additive technology and improved blending practices.
As usual, it is always best to adhere to the OEM’s expiry dates for these products, as different OEMs recommend varying storage times for their products. Generally, synthetic lubricants have an estimated shelf life of 5-10 years, while mineral oils usually last for around 2-3 years, but this is heavily dependent on the OEM and storage conditions.
In some cases, customers tend to store these drums outside in the elements as it makes it easier for them to be readily accessible for decanting into the equipment. However, in these environments, the drums can collect water, which will enter the oil and then, by extension, enter the gearbox. This can cause issues for the equipment and lead to accelerated oil degradation.
Ideally, these oils should be stored in a cool, dry place with ready access to decanting equipment where the decanted oil will not be easily contaminated. Many industrial gearboxes typically require larger quantities of oil, and decanting can take place directly from the drum into the equipment or via a pump.
In these cases, the level of contamination must be minimized by ensuring that the fittings, hoses, etc., are clean and have not been used to decant other types of oils.
The Future of Gear Oils
According to (Industry ARC (Analytics. Research. Consulting), 2024), the global industrial gear oil market size is forecasted to reach USD 5.2 B by 2027. While the Asia-Pacific market holds a significant market share for industrial gear oils in 2021 at around 56.2%, it is interesting that its nearest rival is Europe, at 17.7% or less than ⅓ of its size.
The rise in the Asia Pacific market can be accounted for due to the increase in the rising population and, by extension, the needs of that population and the service sectors they support, including the energy, oil & gas, construction, and steel industries. The figure below depicts the global industrial gear oil market revenue share by Geography for 2021.
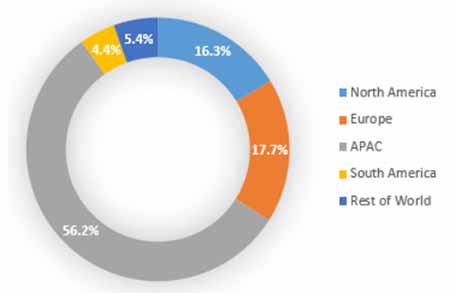
Figure 6: Industrial Gear Oils (Mineral & Synthetic) Market Revenue Share by Geography 2021 adapted from (Industry ARC (Analytics. Research. Consulting), 2024)
From the research conducted by (Industry ARC (Analytics. Research. Consulting), 2024), helical gears appear to be the most popular choice for industrial gears. Interestingly enough, synthetic gear oil held the largest market share and is forecasted to grow by a CAGR of 5.6% for the forecasted period of 2022-2027.
Smaller gearboxes are being manufactured, tasked with outperforming their previous counterparts and producing more torque in a smaller space. With the advent of better, more precise machining tools for gears, there is an increase in the amount of pressure these gears now must handle in smaller spaces.
As such, we will continue to see the rise in the use of synthetic gear lubricants formulated to handle these extreme conditions, as well as more advanced additive packages that can help minimize foaming, reduce oxidation, and aid in the demulsibility of these oils.
References
Industry ARC (Analytics. Research. Consulting). (2024, September 04). Industrial Gear Oils (Mineral & Synthetic) Market – Forecast(2024 – 2030). Retrieved from Industry ARC: https://www.industryarc.com/Report/20008/industrial-gear-oils-mineral-and-synthetic-market.html
Mang, T., & Dresel, W. (2007). Lubricants and Lubrication – Second Edition. Weinheim: WILEY-VCH GmbH & Co. KGaA.
Mang, T., Bobzin, K., & Bartels, T. (2011). Industrial Tribology – Tribosystems, Friction, Wear and Surface Engineering, Lubrication. Weinheim: WILEY-VCH Verlag GmbH & Co. KGaA.
Pirro, D. M., Webster, M., & Daschner, E. (2016). Lubrication Fundamentals – Third Edition, Revised and Expanded. Boca Raton: CRC Press, Taylor & Francis Group.
Rensselar, J. v. (February 2013). Gear oils. Tribology and Lubrication Technology – STLE, 33.
Sander, J. (2020). Putting the simple back into viscosity. Retrieved from Lubrication Engineers: https://lelubricants.com/wp-content/uploads/pdf/news/White%20Papers/simple_viscosity.pdf
Santora, M. (2018, March 20). Tips on properly specifying gear oil. Retrieved from Design World: https://www.designworldonline.com/tips-on-properly-specifying-gear-oil/#:~:text=CLP%20Gear%20Oils&text=Often%2C%20a%20gear%20manufacturer%20will,a%20CLP%20polyglycol%20PAG%20oil