Many people emphasize the impact of particle and moisture contamination on equipment reliability, but few consider how air might affect their equipment.
While usually benign, excessive air entrainment can lead to many issues, including rust, cavitation, oil leakage, and premature oil degradation.
Air is particularly problematic in hydraulic systems since it lowers the bulk modulus of the hydraulic fluid, which can cause problems with volumetric efficiency, precision positioning of tools and actuators, longer response time, and overall poor system stability.
How Does Air Exist in Oil?
At atmospheric pressure, mineral oil will hold approximately 10% air by volume. Under these conditions, no visible air bubbles will exist. However, as pressure increases, the air-in-oil will also increase.
Conversely, as the concentration of air increases or the pressure decreases, tiny air bubbles will appear in the oil, making the oil look cloudy. This is known as entrained air.
Entrained air can be problematic when it enters the load zone of a bearing since it reduces overall film thickness. In journal bearings or hydraulic pumps, the rapid change in pressure can result in adiabatic compression of the air bubbles, which can cause cavitation and micro-dieseling.
In reservoirs and oil sumps, entrained air will increase the rate of oil degradation and impact the rate of rust and corrosion.
The oil will form foam when the amount of entrained air reaches 30% by volume. Since the foam is lighter than oil, it will collect on top of the oil sump or reservoir, much like the “head” on top of a craft beer.
Excess foaming and aeration can lead to leakage as oil levels rise higher than the tank’s capacity or to a shaft seal interface. It can also act as an insulator, raising overall oil temperatures and impacting long-term oil life.
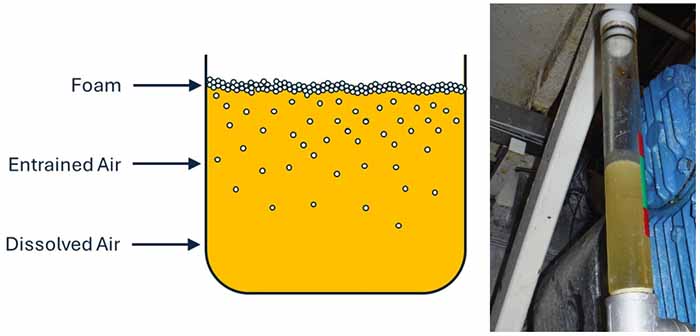
Figure 1: Coexistence of air in oil
In some instances, free air pockets can form in pipes, lines, and hoses. Free air can impact oil flow, causing lubrication starvation and vapor lock.
While all forms of air-in-oil are problematic, entrained air is perhaps the most harmful since it is most likely to be pulled into hydraulic pumps or the load zone of a bearing or gear.
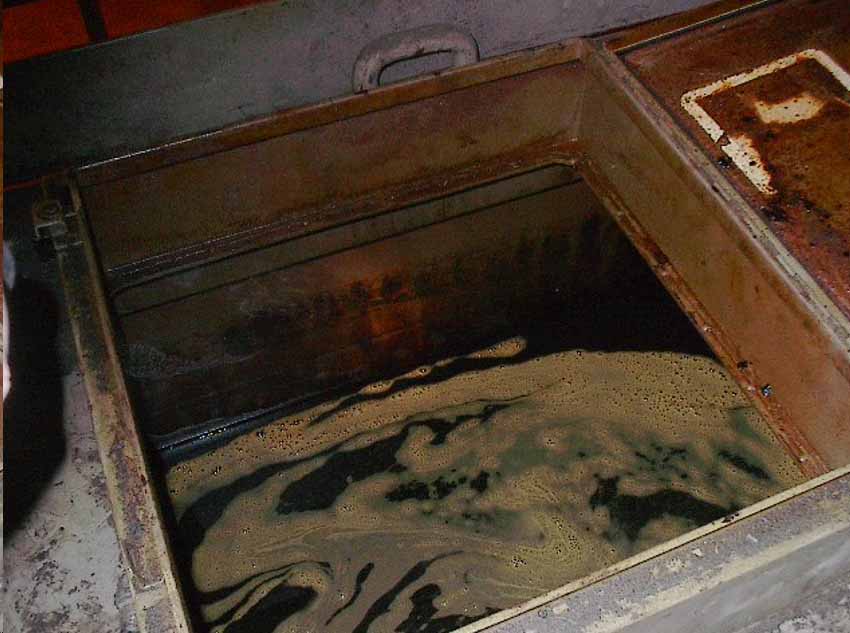
Figure 2: Aeration and mild foam formation inside a paper machine lube oil reservoir due to additive incompatibility.
Oil manufacturers understand the impact of foaming and aeration on lubrication properties, so they formulate most oils with air release agents and antifoam additives, also known as defoamants or foam inhibitors.
There are two main types of antifoam additives used in lubricants: methyl silicones and acrylate copolymers such as polymethacrylate.
Silicone-based additives are preferred in high-viscosity oils used in applications where a high degree of turbulence is expected, such as engines and gear oils. This is because silicones have been shown to hinder the formation of air bubbles by changing the surface tension of the bubble, making it weaker and more prone to releasing the air.
By contrast, silicone-based additives can hurt air release in static or slow-moving fluids, so acrylate copolymers are primarily preferred in hydraulics and other circulating fluids.
Testing for Foaming and Aeration
Several tests can be run to determine the degree to which an oil can detrain air and resist foaming.
The two most common are ASTM D892, often referred to as foaming tendency and stability, and ASTM D3427, which can be used to measure how quickly an oil can release entrained air. The two are often run in parallel when determining the root cause of a foaming or aeration issue.
ASTM D892 involves three distinct testing sequences. Sequence I testing requires 200 ml of the sample to be heated to 24 °C.
The sample is then aerated with clean, dry air for 5 minutes, after which the amount of foam (in ml) initially generated is recorded as the oil’s foaming tendency. The sample is then left to sit for a further 10 minutes, after which the oil’s foam stability is recorded, again in ml.
Sequence II repeats the same process with a fresh sample heated to 93 °C, while Sequence III uses the same sample previously heated in Sequence II after the oil temperature has been reduced and stabilized to 24 °C.
The purpose of the three steps is to evaluate the impact of the oil’s viscosity and any aqueous and volatile contaminants that may evaporate after heating to 93 °C.
While ASTM D892 has been the industry standard for many years, it may not necessarily reflect what might happen in a real-world application with a high degree of mechanical agitation.
For this reason, Flender, a major German gearbox manufacturer developed a test rig to measure the impact of splashing gears on an oil’s tendency to become aerated and foam. Initially an internal test procedure, the method is now an industry standard under ISO 12152.
The Flender test rig deploys a single-stage spur gear to agitate and aerate the oil sample. After a defined test period, the increase in oil volume due to air entrainment and the volume of foam created are recorded, both initially and after a settling period.
An initial increase in oil volume over 15% from baseline or more than 10% remain volumetric increase after sitting for 5 minutes is considered a failing grade for the Flender test (Figure 3).
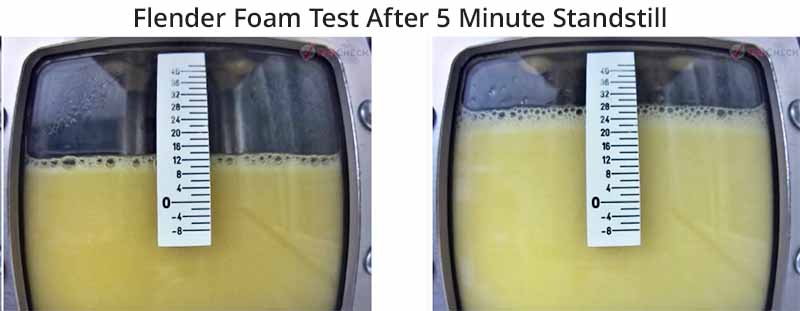
Figure 3: Flender test of a new oil (left) and a used oil (right). The used oil has failed the Flender test due to additive stripping.
Causes of In-service Foaming and Aeration
While new oils will typically pass either the Flender or ASTM D892 test, once an oil is put into service, several factors can result in an overall increase in foaming over time. Perhaps the most common reason for foaming is incorrect oil level.
In wet-sump applications such as pumps and gearboxes, too much or too little oil can result in significant air entrainment and foaming. Likewise, in circulating lube oil or hydraulic systems, air leaks on the suction side of the pump can manifest as aeration and can directly result in pump cavitation.
Similarly, poor system design, such as plunging return lines or insufficient settling time due to small reservoir sizing, can cause air in circulating systems.
Since a “mechanical maintenance issue,” such as a wrong oil level or an air leak, is not directly related to the health or quality of the oil, testing an oil sample from a system showing signs of foaming due to a maintenance issue will show similar foaming tendency and stability results to the new oil using either ASTM D892 or ISO12152.
However, suppose an in-services sample shows a significant deviation from the new oil baseline. In that case, it is important to take additional steps to try to determine the underlying root cause of air entrainment and foaming.
Most commonly, an increase in foaming with an in-service oil is due to chemical contamination.
Since the tendency for an oil to entrain air and form air bubbles is strongly tied to the oil’s surface tension, anything that changes the surface tension can result in aeration.
This includes certain process chemicals, cleaning agents containing a detergent, and accidental grease ingression, perhaps due to over-greasing shaft seals or bearings.
In some industries, such as mining and cement manufacturing, it is common to see significant amounts of dust and dirt ingress, resulting in high concentrations of tiny particles in the oil.
Under some circumstances, these particles are a perfect size to act as nucleation sites, creating an ideal point for air bubbles to coalesce.
In oils that contain silicon-based antifoam additives, foaming can result if the additive is lost or removed. This can occur due to over-aggressive filtration.
Where silicon additives are in use, it is generally not recommended to filter the oil below 5 microns and to ensure that the oil is at a reasonable temperature (>20 °C/68 °F) during filtration, which helps with additive solubility.
If the antifoam additive has been lost or consumed, it is possible to re-dose the oil with an antifoam treatment. However, extreme care should be exercised. If the cause of foaming is unrelated to additive removal, overdosing an oil with antifoam additives can have the opposite effect and induce increased foaming and aeration.
Another common cause of foam is due to accidental cross-contamination. Even small amounts (<10%) of mixing of two oils with different additives components can result in aeration, so testing for foaming tendency using ASTM D892 should always be part of the test slate when evaluating the compatibility of two fluids.
If incompatibility is suspected, extreme caution should be exercised when changing to a different fluid, including extensive flushing and cleaning.
While less common than other contamination-induced failures, aeration should not be ignored. New oils are formulated to detrain air quickly and efficiently and resist the tendency to foam. Any change in this fundamental oil property is a warning sign that something is not right and should always prompt further testing and investigation.