Whether we realize this or not, oil refineries are critical in our everyday lives. They convert crude products into diesel, gasoline, LPG, and plastics. The equipment in this plant must withstand very high temperatures, sometimes over 500°C (in the distillation unit).
The lubrication systems in these plants also must withstand very harsh environmental conditions. Quite often, the bearing temperatures in critical compressors may increase to over 100°C, threatening a trip or shutdown. Unplanned downtime reduces refinery output and may cost a refinery up to Euro 1.2 M/day. All of this can be avoided by maintaining the quality of the lubricants.
Why Varnish Threatens Refinery Operations
Varnish, lubricant-derived system deposits occur in most types of equipment. It plates out as deposits on the insides of the equipment, which will act as a thick layer of insulator, preventing heat from escaping. One of the main functions of oil is to provide cooling to the equipment by transferring heat away from the internals of the equipment. However, with the formation of varnish, this function of the oil is eliminated.
Essentially, varnish can be described as polar compounds that have been formed as a result of the degradation of oil. There are various ways in which oil can degrade to produce deposits. As such, varnish can have varying characteristics depending on the system’s conditions, the formulation of the oil, and any contaminants that may be present in the system.
Despite the way varnish was created, some aspects remain the same. The presence of varnish can cause the sticking of valves or impact the efficiency of heat exchangers. Given the small clearances for hydraulic or other precision equipment (such as turbines or in bearings), any deposits inside these components can affect oil flow.
This results in elevated temperatures, which further increase thermal stress on the oil, thereby establishing a continuous feedback loop.
Varnish buildup creates a feedback loop of rising temperatures and increased stress on oil.
According to the varnish lifecycle illustrated in Figure 1, varnish can precipitate in and out of the solution even after oxidation has occurred.
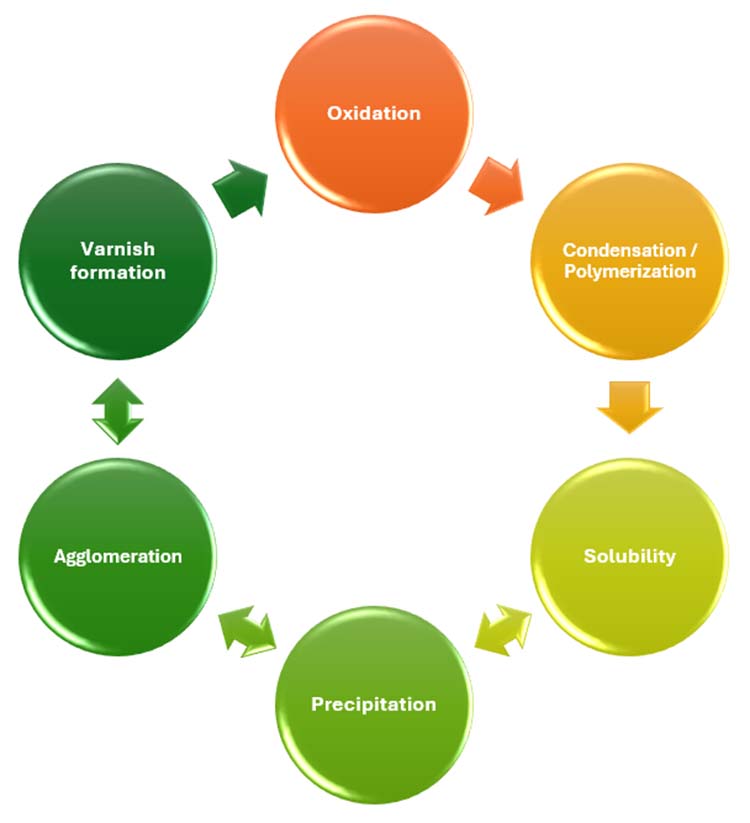
Figure 1: The Varnish Lifecycle showing the typical stages of oxidation to varnish formation
From this lifecycle, it is clear that the double arrows are used between the solubility and varnish formation stages. As such, even if varnish is formed and deposited using the right technologies, it is possible that it can be redissolved into the oil.
In compressor applications, its bearings are the most critical place for varnish to form. This occurs in the minimum film thickness zone, as seen in Figure 2.
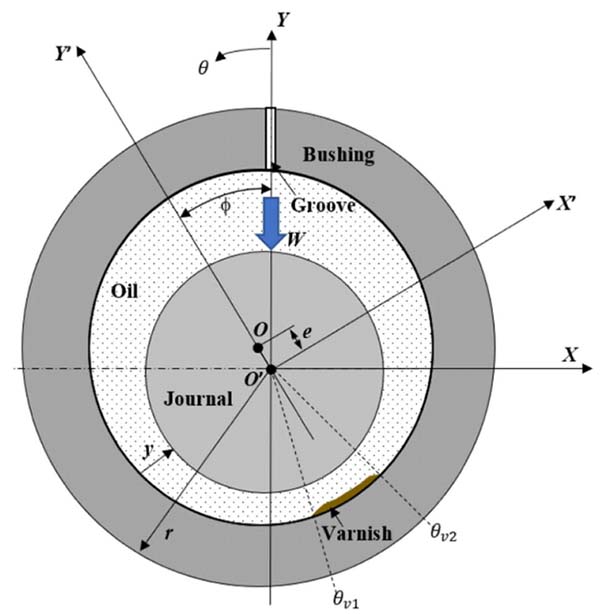
Figure 2: Schematic diagram of a journal bearing with one axial groove illustrating the location of varnish occurring in the minimum oil film thickness region.
As per (Jang, Khonsari, Soto, & Livingstone, 2024), one can predict the effect of varnish on bearing performance by solving the Reynolds equation for pressure distributions with the mass conservation algorithm coupled with the energy equation through viscosity. However, this method was not utilized at the refinery.
Based on the study by (Jang, Khonsari, Soto, & Livingstone, 2024), the maximum pressure decreases when the varnish size extends circumferentially at a given varnish thickness, but the temperature remains relatively constant.
Case Study: How TÜPRAŞ Tackled Varnish Issues
Tüpraş is Turkey’s largest oil refiner, and it is located in western Turkey. It manufactures LPG, gasoline, jet fuel, and diesel fuel. They experienced trips on their compressor in the Kırıkkale Refinery, which has a mid-level complexity by Mediterranean Standards, including hydrocracker, isomerization, diesel sulphurization, and CCR reformer units.
The Kırıkkale Refinery has an annual crude oil processing capacity of 5.4 M tonnes, and its supply is carried by the BOTAȘ’ Ceyhan Terminal and Ceyhan- Kırıkkale pipeline. It was established in 1986 to meet the petroleum demands of the Ankara, Central Anatolia, Eastern Mediterranean, and Eastern Black Sea regions.
The K1151 compressor (RB5B Thermodyne compressor) in the Kırıkkale Refinery is critical to the Crude oil processing and isomerization unit. Every time this asset trips, the facility undergoes maintenance and repairs, typically lasting seven business days. This issue may occur at least 4 times annually, and each trip costs roughly around USD274k per event.
A trip usually occurs when the bearing temperature goes above 115°C, however, based on the history of the machine, the temperatures typically see a spike to 100°C followed by a rapid increase to 115°C.
For this compressor, it was also noticed that there were sawtooth-like temperature patterns where the values fluctuated between 76-86°C, as shown in Figure 3 below. The “safe zone” of operation for the bearings is less than 89°C.
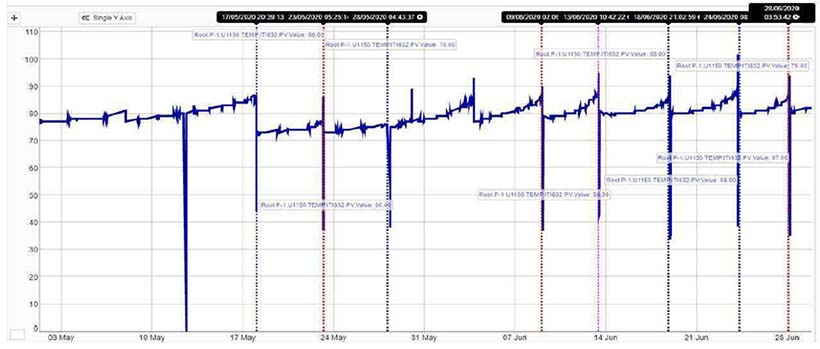
Figure 3: Sawtooth temperature pattern
This sawtooth temperature pattern is typically seen in instances where there is varnish buildup on bearings or shafts. Usually, the varnish builds up layer by layer, acting as an insulator, which causes the temperatures to increase.
Eventually, the buildup will get to a point where the shaft wipes away the varnish, resulting in a plunge in temperature, forming this sawtooth pattern. This repeats constantly until the varnish is either removed from the system or shut down so it can be removed.
After dismantling the NDE (Non-Drive End) bearing, varnish was found along the shaft and the actual bearing, as shown in Figures 4 and 5 below.
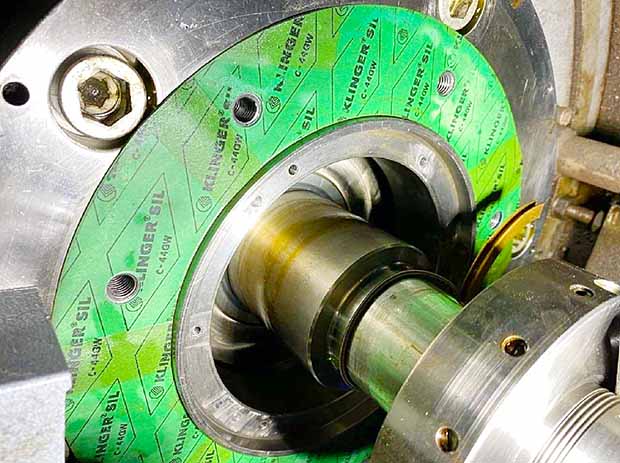
Figure 4: Varnish along the NDE shaft region
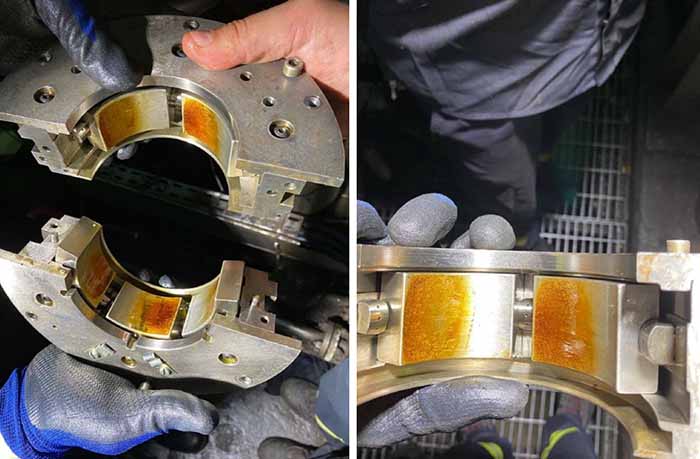
Figure 5: Varnish present on the NDE bearing
Interestingly enough, the bearings gave different temperature readings for this component. TI 633 showed slightly different readings compared to TI 632 mainly because of where they are positioned on the bearing, as these pads had varying levels of varnish on them, as shown below in Figure 6.
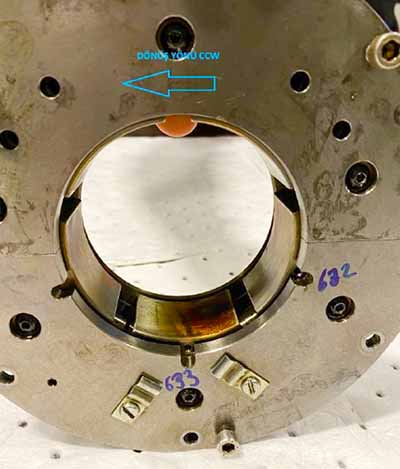
Figure 6: Location of the bearings TI 632 & TI 633
The refinery elected to add Fluitec’s DECON to the system during operation to provide immediate temperature relief to the bearing. DECON enhances the solubility of the oil, which does two things:
- It dissolves varnish throughout the system, and in this case, specifically in the bearings and shaft.
- It prevents future varnish from forming again.
Solubility enhancers are soluble in the oil and can react with already degraded products (deposits or varnish) to make them soluble in the oil. In this way, the degraded products are not allowed to agglomerate into the layers of deposits and remain in the oil as inert, harmless products.
After Fluitec’s DECON was added to the system, the compressor saw an immediate decline in temperature from 101°C to 93°C and continued to decline afterward. Currently, this bearing is operating in the temperature range of 63°C. The highest temperature experienced by the system is 73°C, which is significantly below their “safe-zone” temperatures of 89°C.
After adding DECON, compressor bearing temperatures dropped from 101°C to 63°C.
Since adding DECON to their system, they have not had any other trips due to rapid temperature increases, and their bearings now operate below the maximum threshold temperature range.
Tüpraş is committed to sustainability and aims to be carbon-neutral by 2050. The company focuses on innovative technologies and digital transformation to enhance operational efficiency and reduce carbon emissions. DECON is consistent with their organization’s objectives as it significantly improves compressor efficiency while increasing operational reliability.
Using Fluitec’s Value Impact Calculator, it is estimated that 32 tons of CO2e will be reduced from their operation over 5 years simply by optimizing the life and performance of their lubricant.
References
Jang, J. Y., Khonsari, M. M., Soto, C., & Livingstone, G. (2024). Effect of varnish on the performance and stability of journal bearings. Tribology International, Volume 198.