The global natural gas and landfill gas engine market is growing at annual compound rates of 6% to 8%, and these segments are expected to increase their share in the coming years, supported by technological advances and circular economy policies.
Currently, and depending on the source consulted, power generation with gas engines represents between 8% and 10% of global generation. In 2023 and part of 2024, natural gas generation accounts for approximately 60% of the market, while landfill and natural gas occupy 25% and 15%, respectively.
The natural gas engine market is consolidated and led by emission-efficient technologies, while landfill gas and biogas are gradually gaining traction as more sustainable options thanks to clean energy policies and increased investment in value-added infrastructure.
In regions such as Europe and North America, strict regulations and government incentives have accelerated the adoption of engine technologies that use landfill gas and biogas.
These gases, composed mainly of methane, are increasingly used for electricity generation in waste treatment plants and landfills. Companies are improving the efficiency of biogas-powered engines, although they face technical challenges, such as corrosion and lubricant contamination due mainly to the sulfur content in biogas.
Demanding Conditions Require High-Performance Lubricants
Lubricating stationary engines that run on gas requires specialized oils due to each type of gas’s combustion characteristics and contaminants.
Natural gas engines typically have cleaner and more stable combustion, which allows for longer intervals between oil changes and makes it easier to anticipate chemical changes that may occur. They require low-ash lubricants to minimize deposit formation and protect critical components such as valves.
On the other hand, these oils must have high thermal stability and resistance to oxidation due to the high temperatures and pressures in the engine.
Natural gas engines benefit from low-ash lubricants that protect critical components like valves.
The combustion gas can vary depending on the geographical location and conditions of production. However, it is mainly composed of methane and carbon dioxide and can contain pollutants such as hydrogen sulfide and siloxanes.
These contaminants generate acidic byproducts and abrasive particles affecting oil performance and lubricated components. For this reason, biogas engine lubricants need higher detergency and higher BN (Base Number) to neutralize acids and minimize the effect of corrosion.
As for landfill gas engines, the gas has a greater variability in its composition, with high levels of contaminants.
Oils must be able to handle a higher load of residues and offer a strong neutralization capacity for acidic byproducts. As with biogas engines, gas pre-treatment, and regular lubricant monitoring are crucial to maintain engine performance and protect internal components.
In all three cases, a proper in-service oil analysis program is vital in preventing failures and optimizing the engine’s life and the lubricant.
Tribological Conditions in Power Generation in Gas Engines
If you’ve been in the lubrication area for a while, you’ve probably heard of the Stribeck curve. The Stribeck curve is a fundamental tool in tribology as it describes how the coefficient of friction varies depending on lubrication conditions.
It was developed by Richard Stribeck in 1902 (although the same study is also attributed to Mayo Hersey in 1914) and is critical to understanding lubrication regimes in mechanical systems.
This curve includes three main regions:
- Limit lubrication: when there is direct contact between surfaces due to a shortage of lubricant or an unfavorable lubricant condition.
- Mixed lubrication: Some areas are separated by a lubricant film, while others have direct contact.
- Hydrodynamic lubrication: the surfaces are completely separated by a fluid lubricant film.
In gas engines, this curve serves to optimize the selection and formulation of lubricants, as well as the determination of the wear suffered by the components under the effects of lubrication.
In these engines, factors such as viscosity, relative speed between components, and load affect the lubrication regime, influencing the efficiency and service life of the components.
In the limit and mixed lubrication regime, there is a high degree of contact between the moving parts of the lubricated system, which causes premature aging or wear of these components.
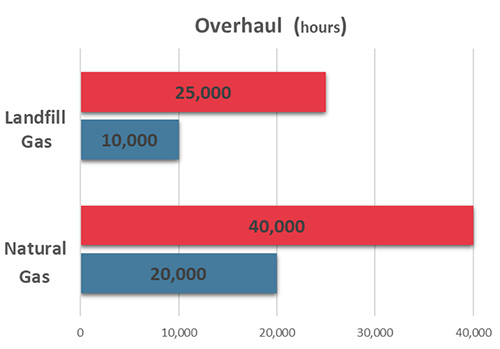
Maximum and Minimum Working Hours
This can become evident when comparing major maintenance on these engines, where an engine running on landfill gas receives maintenance at half the hours that an engine running on natural gas does.
Let’s look at the Stribeck curve adapted to the three main types of gases. Natural, landfill, and biogas. What is the reason for this situation?
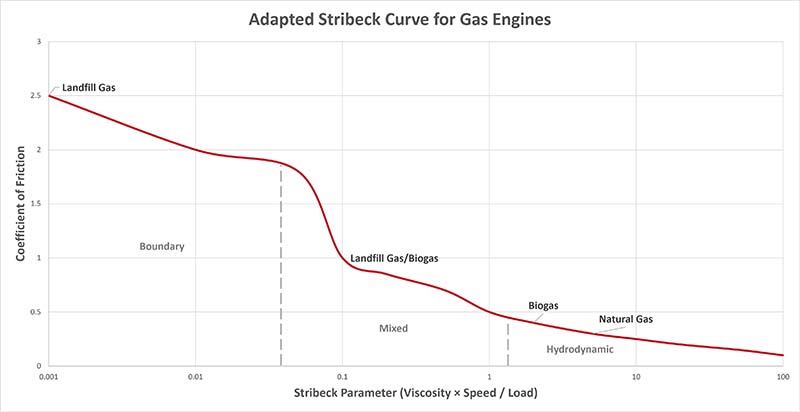
Source: JAB Gas Engine Lubrication Study
Let us ask the same question from a tribological point of view. What is the reason for an engine that works with landfill gas to work under a limited lubrication regime?
The lower values of the Stribeck parameter in a Landfill Gas engine are due to the particular characteristics of this type of engine and the conditions in which it operates, which affect the behavior of the lubricant and the frictional forces in the system. The main factors for the landfill gas engine to work at a limit regime are:
Composition of Landfill Gas
Landfill gas and biogas can have varying concentrations of contaminants, such as H₂Sand ammonia, which can affect operating temperatures and engine efficiency.
Operation at Low Load Levels
Engines operating at higher loads generate more heat, raising engine and oil temperatures.
Low Speed and Viscosity
Landfill gas may have less control in terms of operating speed and temperature, which can affect the oil’s viscosity. If the lubricant’s viscosity is lower than expected, the system tends to be closer to a limit lubrication state.
Impact of Particulate Matter and Contaminants
Landfill gas, a less refined fuel, can contain solid particles or water contaminating the lubricant. These impurities can alter the viscosity and ability of the oil to form a suitable lubricant film. As a result, the system could operate in a mixed lubrication condition or even at a limit, leading to a low Stribeck parameter.
Lower Operating Temperatures
Engines that run on landfill gas often fail to reach the optimal temperatures for oil operation, which can cause the lubricant not to flow efficiently, favoring limit lubrication. This can result in a higher coefficient of friction and a low value for the Stribeck parameter.
One of the products that are present in landfill gas is siloxanes. These organic compounds containing silicon atoms, oxygen, and alkyl or aryl groups (usually methyl) are primarily generated by the degradation of silicone-containing products.
Due to the high temperatures and pressure generated in the chamber during combustion, siloxanes are usually broken down into compounds such as formaldehyde, solid silicon oxides, and acids such as orthosilicic. The latter, when precipitating, forms highly abrasive particles that damage the components, causing accelerated wear.
Abundance Of Data to Generate Specific Knowledge
Due to the impact of lubricant quality on this type of engine, oil analysis programs are generally quite mature, and there is a lot of information, including operating data such as generated production.
However, it is important to know the composition of the engine components’ residues to determine the most common causes of accelerated wear caused by three-body abrasion.
The table below shows the average results of a set of residue samples collected near the pistons of different gas engines, analyzed by scanning electron microscopy (SEM).

Source: JAB Gas Engine Lubrication Study
The most common laboratory analyses are usually viscosity, AN, BN, ipH, water in ppm, and FTIR. Of these, the least exploited is the analysis of compounds by FTIR. A correctly performed analysis can determine the presence of siloxane-derived compounds that can become abrasive as the lubricant is in service. These values can be analyzed to anticipate wear problems in engine components.
On the other hand, the correlation between the hours in service of the oil and the formation of byproducts derived from siloxanes is almost perfect. This allows a more exhaustive analysis of the concentrations of formation of byproducts derived from siloxanes, both precursors of the formation of abrasive elements and those that promote the generation of acids.