Ugly. Torturous. Scourge. Devastating. Catastrophic. Insidious. These are just a few of the words used in papers and presentations to describe the effects of water in oil. You get the picture. For good reason, water has been called the second most destructive contaminant, next to hard particles. OEMs and end users are seeking solutions to battle water and looking for suggestions on how it can be controlled.
Winning the war on water contamination starts with recognizing its threat and taking steps to remove it quickly.
Water Contamination – A Dangerous Opponent
Water in oil is dangerous because it causes many problems with the machine and the oil itself. The following are some of the effects of water contamination:
- Rust and corrosion
- Film strength loss
- Filter plugging
- Steam damage
- Aeration
- Lower viscosity
- Accelerated oxidation
Many experiments have also shown that water promotes micropitting. Water is always present in oil, and all lubricants are susceptible to attack. It is introduced through ingression, condensation, or oxidation. Sometimes, it enters through leaks and faulty seals. It can also be added through improper or careless oil storage and handling.
Once it gets in, the battle with water is on. Water is a formidable foe as it exists in three phases: dissolved, emulsified, and free. In the dissolved state, water molecules are finely dispersed in the oil, similar to the humidity surrounding us.
Emulsified water is a mixture of oil and water that produces a milky or cloudy appearance. It is similar to fog. Lastly, free water is visible as it settles out like rain. Water is most dangerous in the free and emulsified states. Most component manufacturers today state that water content in oil should never exceed 500 ppm if the full life potential is to be realized.
For instance, research has shown that water adversely affects bearing life. Reliability and lifetime are functions of reducing water content (see Figure 1).
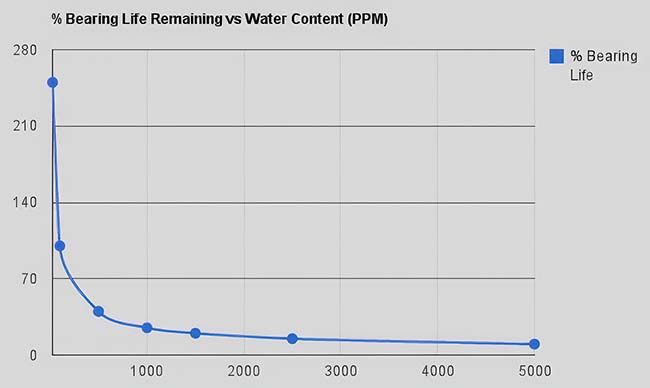
Figure 1: Effect of Water in Oil on Bearing Life (Timken)
Waging the war against water is worth the effort. For example, reducing water content from 100 ppm to 25 ppm can extend the life of the bearing by a factor of 2.5. Conversely, increasing water from 100 to 500 ppm can cut the lifetime in half.
Water Removal Methods
There are several methods to remove water from oil. Some are more rigorous than others. Some are simple and inexpensive, while others are more complex and require a significant investment. Every method has advantages and disadvantages, so each must be carefully evaluated to determine the right fit. Here is a look at some of the most commonly used technologies to consider when drawing up a battle plan against water.
Desiccant Breathers
Airborne moisture penetrates reservoirs through unguarded passageways. The best way to combat airborne water contamination is to have a solid defense. Use high-quality desiccant breathers to restrict ingression. Shielding reservoirs with desiccant breathers not only keeps moisture out but also simultaneously protects against dirt ingression.
NOTE: Changing old-school bayonet-style twist-on caps to a quality desiccant breather will modernize your contamination control army. The change can be made in less than five minutes and will provide a higher level of security (see Figures 2-3).
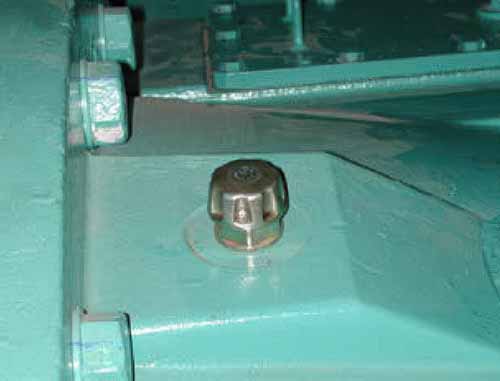
Figure 2: Don’t use old-school breather caps
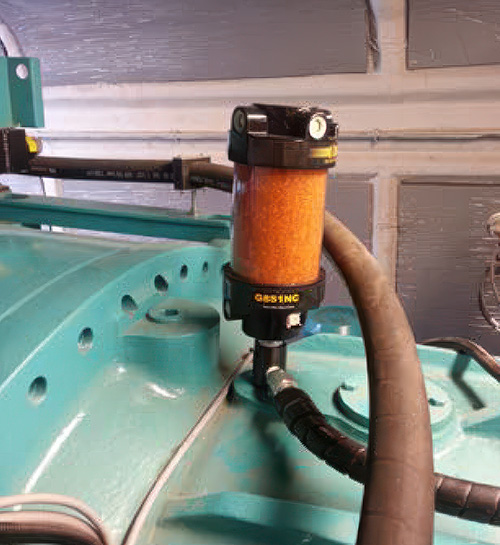
Figure 3: Do use high-quality desiccant breathers
Gravity Separation
Allow water to settle out of the oil. This natural approach will combat free water only. Gravity acts on moisture, tending to settle at the bottom of the reservoir. This is an inexpensive method, but the oil reservoir must be properly designed to promote efficient settling. The oil must have an adequate amount of dwell time.
Heating the oil will increase molecular motion, promote coalescence, and reduce viscosity, improving the gravity separation process. A cone-shaped tank is also recommended to further aid separation.
NOTE: Gravity separation alone will not remove emulsified or dissolved moisture.
Depth Filters
Superabsorbent depth filters commonly used in offline filter systems are well suited to soak up water like sponges. The filter media used is cellulose or other water-absorbing materials such as polymer. Depth filters feature a thick filter mass that provides a low initial pressure drop, high water-absorbing capacity, and structural strength. Free and emulsified water is trapped by the depth filter’s media (see Figure 4).
Water removal capacity is directly related to the construction and surface area of the depth filter. While many depth filters look similar from the outside, some are built and designed to handle higher water loads, while others are more limited.
Your filter supplier will need to know these details. Ask your filter supplier. Don’t bring a knife to a gunfight. Select a depth filter with a higher water removal capacity to keep operational costs down and effectively control water.
These filters will not remove dissolved moisture. However, most reservoirs or systems without steady water ingress will keep the oil dry and clean. Minor water ingress from condensation will be controlled. Water levels can be maintained at 500 ppm or lower in most cases. If sudden water ingress occurs, they can provide early warning by plugging—a sort of condition monitoring.
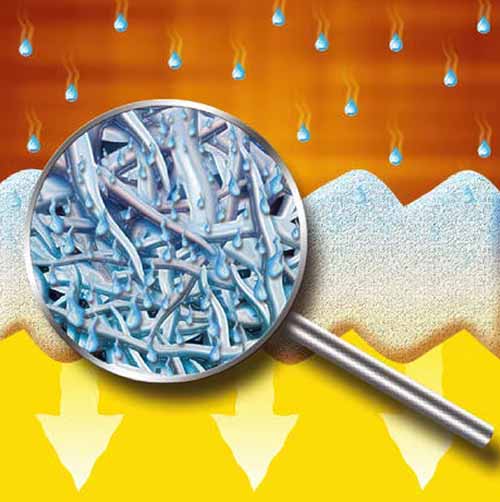
Figure 4: Cross-section view of water trapped by depth filter media
Centrifugal Separation
Centrifuges are a traditional solution for separating free water and some emulsified water. They follow the same principle as gravity separation but greatly speed up the process (6,000 to 10,000 times faster). Water is forced to the outside of the spinning element.
Centrifuges are a proven option for continuous moisture removal. They do not need filter insert replacements. They are best for oil viscosities < ISO VG 150. Consider the operational and maintenance costs when evaluating this solution. Some centrifuges have a reputation for not being user-friendly and maintenance-intensive.
NOTE: Centrifugal separators do not remove dissolved water. Because this is a method of physical separation, there is a risk that additives will be removed.
Coalescing Separation
Looking for a solution that is lower cost and easier to use than a centrifugal separator? Coalescing separators are the answer. They work by attracting water droplets to the coalescing media. As the moisture-laden oil passes through the filter, water droplets will impinge upon the media. Smaller droplets will merge together, forming larger droplets. Larger droplets have a lower surface area, so they will drop out of the oil more easily (see Figure 5).
Coalescers will remove free water and some emulsions. They will not remove dissolved water. However, in most systems, they are an ideal solution because their purchase and operating costs are lower than those of other traditional methods of water removal. They are well suited for diesel, hydraulic oil, lube oil, and gear oil up to ISO VG 150.
NOTE: Consider Coalescing Separators in applications such as thrusters for marine vessels, pulp and paper machinery, diesel storage tanks, diesel backup generators at data centers, and diesel fuel systems. Typical water results are 50-300 ppm. They will simultaneously retain hard particles and varnish.
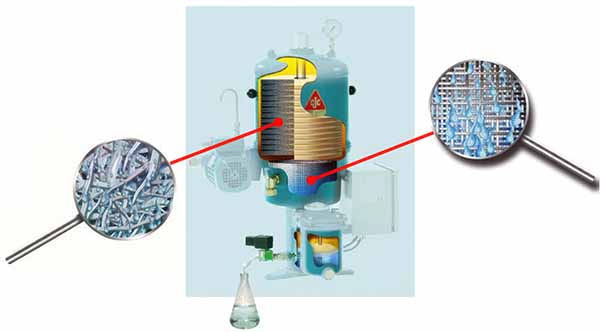
Figure 5: Cutaway view of coalescing separation process
Vacuum Dehydration
This solution can remove free, emulsified, and dissolved water. Oil should be filtered before passing through the dehydrator to minimize contamination of the elements. It is an effective but costly means of removing water. The dehydration process typically runs at 90°F – 150°F and vacuum between 23″ – 28″ Hg.
Water will boil under these conditions. At the operating temperature range, it does not cause much damage to the base oil or additive package. However, there is some possibility of additive vaporization.
It is common knowledge that vacuum techniques are not user-friendly. If there is a large dose of water ingress (e.g., cooler leakage or sudden water ingress), the vacuum chamber will ‘boil over’ and create foaming problems. This will cause frequent nuisance tripping.
NOTE: The initial purchase price can be high, and they tend to take up a significant amount of space. Ask your supplier to also provide estimated yearly operational costs. Unless removing dissolved water is mission critical, a lower-cost solution such as Depth Filters or Coalescing Separation is ideal for controlling water.
Desorbers
These units operate by the “air stripping” principle. Desorbers heat the oil slightly before it enters the integrated chamber. The heated oil meets a counterflow of cool air inside the chamber. Now heated by the oil, air expands and draws water from the oil. The subsequent air cooling condenses the water and drains out of the system. The cycle continues as the now dry air is recirculated to remove water from incoming oil (see Figure 6). The cycle repeats, and the oil gets dry.
Desorbers effectively and reliably remove free, emulsified, and dissolved water from all types of oils. This technique can treat viscosities up to ISO VG 1000. Desorbers are ideal for use in applications where water ingress is a continuous and significant problem. They will not remove additives and are suitable for oil volumes up to 15,000 gallons.
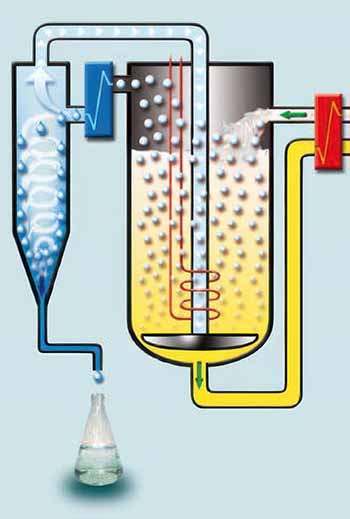
Figure 6 – Principle of Desorber operation
Seven Solutions – The Big Picture
Leading OEMs and end users are winning the war against water by employing one or a combination of the seven solutions discussed. Good practice is to set water level targets according to the reliability needs. Best practice is to remove water below the saturation point so the oil is clear and bright. The following table summarizes the seven solutions, including general ratings, advantages, and their corresponding tradeoffs.
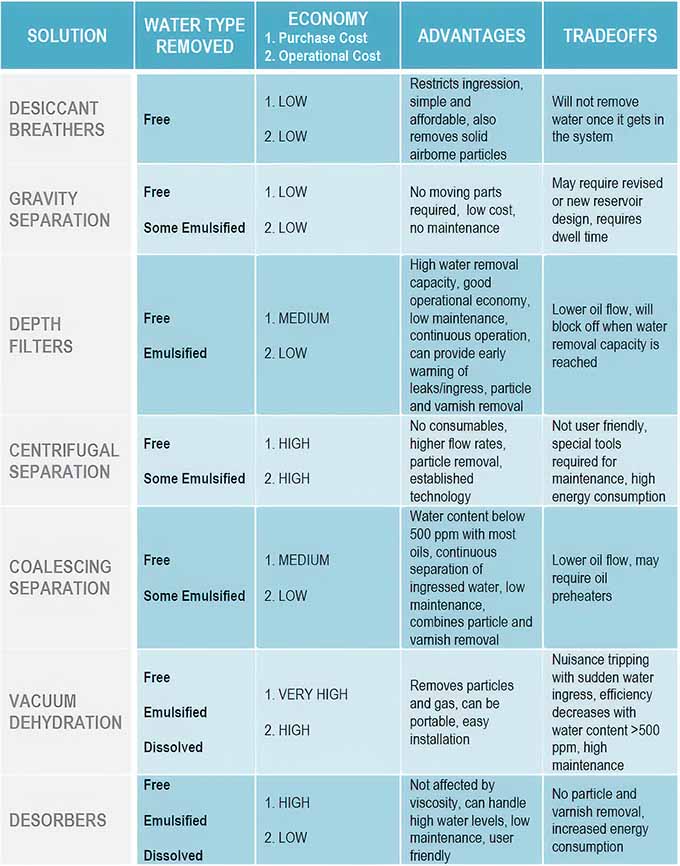
Table 1: Water Removal Solutions Performance Overview