Heat Transfer Systems (HTS), also known as thermal fluid heating systems or hot oil systems, operate by circulating a fluid through a closed-loop system to transfer heat to and from various process equipment. These systems are widely used in industries for applications requiring precise temperature control and high-temperature operations without the need for high pressure.
Heat transfer oils are formulated for long service life and to resist thermal cracking and oxidation. Eventually, they will deteriorate, generating deposits that may interfere with the system’s heat transfer efficiency. Remedying these efficiency losses and system deposits involves a costly system shutdown and complex flushing processes.
A new maintenance approach has been developed to restore system efficiency and improve lube oil quality without requiring an outage. We will review the science behind this innovation and present a case study demonstrating its effectiveness.
Heat Transfer System Basics
HTS are simple in design and consist of a heater, pump, expansion tank, and process vessel. The components are shown in Fig. 1 below.
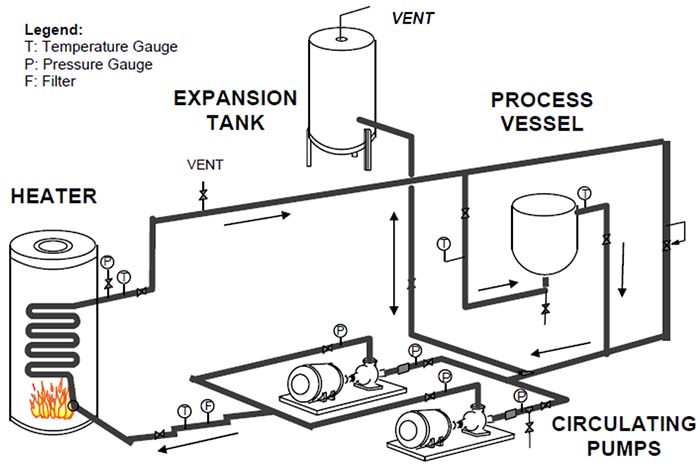
Figure 1: Components of a thermal fluid heating system
Understanding the bulk oil temperature can help estimate the thermal stress placed on the oil. However, there are also higher thermal loads placed on the fluid at the interface of the piping as the oil flows are lower in this region, as can be seen in Figure. 2.
In a properly functioning HTS utilizing hydrocarbon oil heat transfer fluids, the oil film is typically 14-28°C (25-50°F) higher than the bulk oil temperature. However, if the oil velocity is reduced, film temperatures can be more than 40°C (104°F), causing accelerated oil degradation. Well-established calculations are used to estimate film temperature based on oil flow, pipe diameter, and heater capacity.
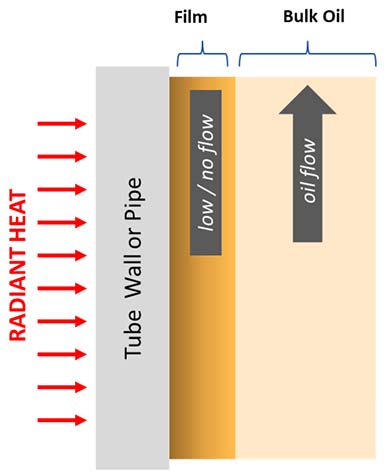
Figure 2: Fluid film temperature is higher than the bulk oil temperature due to lower flow rates.
Conventional heat transfer oils thermally crack at 360°C (680°F), so understanding the fluid film temperature is essential to fully understand the oil’s thermal stress.
Thermal Fluid Degradation and Analysis
Mineral-based heat transfer fluids can degrade in two main ways: thermal cracking and oxidation. Thermal cracking involves breaking the bonds between carbon atoms and forming shorter hydrocarbon molecules. This happens more often in closed HTS systems that may have nitrogen blanketing.
Oxidation involves transferring an electron from one molecule to another, increasing its oxidation state. This happens more often in open systems that have contact with air.
Even though the two oil degradation mechanisms are due to high temperatures, the impact on the oil differs depending on which pathways are involved. Table 1 illustrates the differences between the two phenomena.
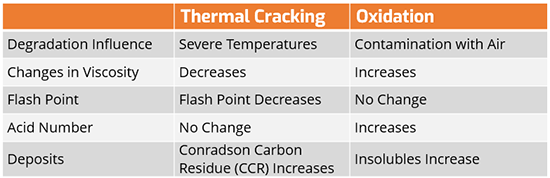
Table 1: A comparison between thermal cracking and oxidation
To determine the condition of in-service heat transfer fluids, Mobil has developed an oil analysis package that includes the following tests:
- Viscosity
- Water volume % Karl Fischer (KF)
- Oxidation
- Total Acid Number (TAN)
- Particle Quantifier (PQ) Index
- Metals
- Flash Point (Cleveland Open Cup)
- Micro Carbon Residue (MCR)
Other tests may include Flash Point (Penske Martin Closed Cup), Conradson Carbon Residue, Pentane Insolubles, or Simulated Distillation by Gas Chromography.
Assessing Fluid Safety
Thermal cracking breaks the backbone of hydrocarbon molecules. The newly created, smaller chain molecules lower the viscosity and flash point of the oil. Flash point testing is essential because safety risks are introduced to the system if it falls too low.
The first screening is the Cleveland Open Cup flash point test (ASTM D-92). If it has not decreased, thermal degradation is not a significant influence. However, further testing is warranted if the flash point has dropped to more than 50°C (122°F). The Penske-Martins Closed Cup flash point test (ASTM D-93) concentrates the light ends or low boilers produced through thermal cracking.
It is not uncommon to see 100°C (212°F) differences between flash point testing methodologies, with ASTM D-93 delivering a lower flash point result when light ends are prevalent.
It’s important to ensure the closed-cup flash point of in-service oil is at least 14°C (57°F) above the temperature of the oil exposed to air (i.e., an open expansion tank). Values lower than this are typically considered critical, as the oil’s flash point approaches the exposed oil temperature, the chances for ignition or fire increase.
Flash point testing is an important parameter, but it only measures the presence of light ends, not their concentration. To get deeper insight into the degree of thermal degradation and estimated remaining useful life of the oil, one can employ Simulated Distillation by Gas Chromatography (GCD).
This test measures the relative proportions of the entire range of molecules in the sample and provides a deeper understanding of the thermal stress on the fluid. An example can be seen in Figure 3.
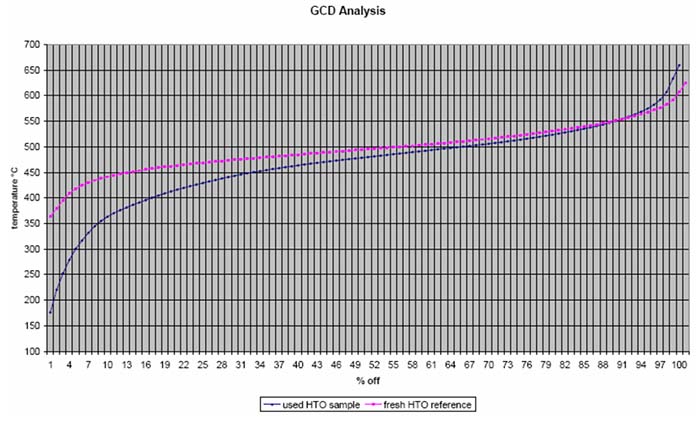
Figure 3: An example of GCD analysis on fresh and used heat transfer oil
Degraded Oils Impact HTS Efficiency
Measuring efficiency in a Heat Transfer System involves evaluating how effectively the system transfers heat without incurring unnecessary energy loss. Here are key factors and methods used to measure efficiency:
- Thermal Efficiency: This measures the ratio of heat transfer effectiveness of the hot oil system to the energy input. It can be calculated by comparing the heat transferred to the process to the total energy supplied to the hot oil heater.
- Temperature Differential: Monitoring the temperature differential between the inlet and outlet of the process equipment can indicate how effectively the hot oil system is transferring heat. A smaller differential may indicate heat loss or inefficiency in the system.
- Flow Rate: The flow rate of the oil through the system impacts heat transfer efficiency. Too low a flow rate can lead to inadequate heat transfer and accelerated oil degradation, while too high a flow rate can increase energy consumption without proportional benefits. Measuring and optimizing flow rates are crucial.
- Pump Efficiency: Since pumps are used to circulate the hot oil, their efficiency impacts the overall system efficiency. Measuring the electrical energy input to the pump and comparing it to the hydraulic energy delivered by the pump can indicate its efficiency.
Sufficient thermal stress on heat transfer fluids over a long enough time will cause even the most highly refined products to degrade. One of the failure mechanisms of these fluids is the formation of carbon-rich deposits. The formation of oil deposits can lower HTS efficiency in each of the above four areas.
The Challenge with Treating Thermal Fluids
Shutting down heat transfer systems for maintenance can be costly as their operation is tightly linked with production. Furthermore, in badly degraded systems, the oil may solidify, requiring shovels or even the removal of piping to evacuate the deposits.
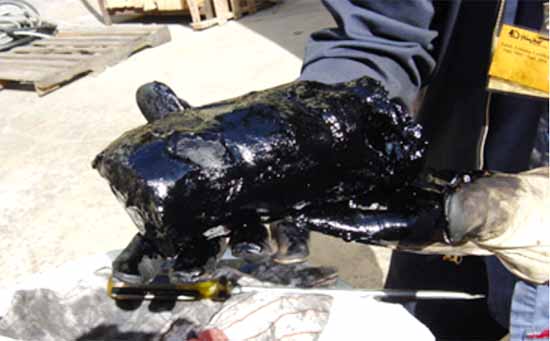
Figure 4: A “carbon log” removed from a HTS.
Online remediation of thermal fluids in heat transfer systems is also challenging, stemming from the need to maintain system efficiency, safety, and integrity without disrupting the production process. Here are some of the key challenges:
- Safety Concerns: Handling hot thermal fluids poses significant safety risks, including burns, fires, and explosions. Performing online remediation requires stringent safety protocols to protect personnel from the hazards associated with high temperatures and potentially reactive or flammable fluids.
- Decontamination: Advancements in chemical filtration technologies to remove oil degradation products in other industrial lubricant applications are not suitable for heat transfer fluids due to the high temperatures.
- Detergent-based oil cleaners: Adding chemical cleaners to heat transfer fluids may be a suitable strategy when part of a turnkey flushing procedure but introduces operational risks when added to an operating system, including rapid deposit accumulation and decreased flash points.
Mobil™ Solvancer® is an Online Solution to Improve System Efficiency
Mobil Solvancer is a full synthetic, API Group V, oil soluble cleaner designed to be safely added to in-service oils with no measurable impact to fluid quality or system performance. It dramatically increases the solubility of an in-service oil allowing deposits to be dissolved. It also minimizes further deposits from being generated.
Mobil Solvancer helps to eliminate carbon deposits from heat transfer systems, making heat exchangers, pipes, and pumps cleaner. Mobil Solvancer is an effective solution to increase system efficiency in HTS by tackling carbon deposits.
Case Study: Improving System Efficiency in an Asphalt Plant
Inefficiency was slowing production at a US-based asphalt plant. Their HTS failed to consistently maintain thermal balance, causing increased labor costs and component wear. To improve plant thermal efficiency, the plant added 3.3% Mobil Solvancer to the in-service heat transfer fluid.
Figures 5 and 6 show the Mobil Solvancer being added to the HTS as well as the appearance of Mobil Solvancer.
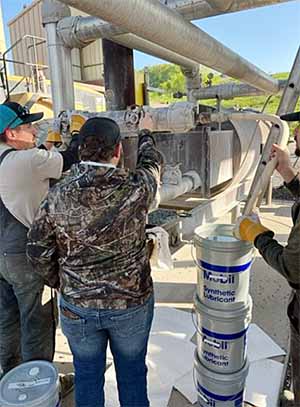
Figure 5: Mobil Solvancer being added.
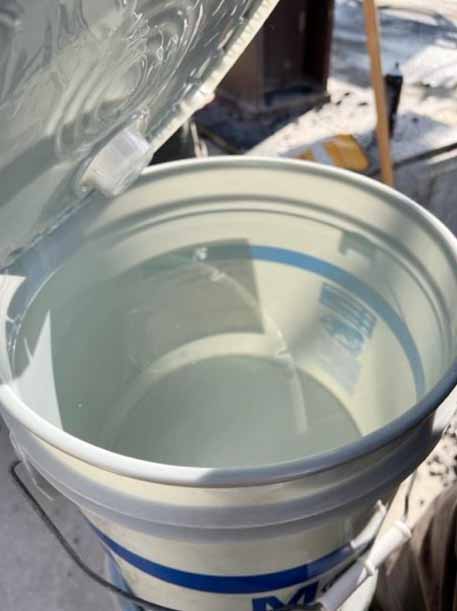
Figure 6: The Appearance of Mobil Solvancer.
After more than six months, the plant observed numerous benefits, including*:
- 20% decrease in fuel consumption.
- Increased plant capacity and flexibility with longer production runs.
- Decreased trucking expenses to deliver binder.
- Zero hot oil breakdowns (for the first time in the plant’s history).
- Reduced pump wear due to less direct heating.
- Restored thermal balance measured after a few weeks resulting in faster start-ups.
- Lower maintenance costs to restart the system, as previously, crews would have to manually heat pumps and injection pipes.
- Reduced oil consumption as the system’s overall oil parameters were stable enough to allow the plant to skip a full system oil change.
- The micro carbon residue (MCR) deposit test and viscosity showed improvements with no change to the fluid’s flash point.
*Individual results may vary depending on operating and weather conditions
Heat Transfer Systems exert sustained, high heat stress on their thermal fluids, resulting in the formation of carbon-rich deposits. The accumulation of these deposits lowers the efficiency and thermal balance of HTS. Traditionally, treating in-service heat transfer oils is challenging due to safety and system performance concerns. Mobil Solvancer represents a novel way of treating in-service heat transfer fluids, restoring system efficiency.
A case study in an asphalt plant was presented, which demonstrated that Mobil Solvancer restored thermal balance in their system and reduced fuel consumption by 20%. The quality of the in-service oil was also improved, avoiding an oil change.
Please contact your local Mobil or Fluitec technical specialist for specific details about adding Mobil Solvancer to your thermal fluid heating system.
© 2024 ExxonMobil. All trademarks used herein are trademarks or registered trademarks of Exxon Mobil Corporation or one of its subsidiaries. All rights reserved
© 2024 Fluitec. Fluitec and Solvancer are registered trademarks of Fluitec NV or one of its subsidiaries.