When it comes to hydraulic systems, oil contamination is one of the most insidious and persistent enemies. It is estimated that about 80% of failures in these systems are directly related to fluid contamination. The issue goes beyond simply cleaning the oil; It involves preserving the performance and lifespan of equipment. And if contamination is the main cause of failures, effective control of it is the solution for a more reliable and economical operation.
How Contaminants Quietly Destroy Your System
Lubricant contamination occurs when unwanted particles, such as dust, water, metal or chemical residues, enter the system. This contamination can occur through various means, including poorly sealed reservoir vents and caps, worn seals, environments with a high concentration of contaminants, or improper storage and handling practices of lubricants.
When these contaminants enter the lubricant, they reduce its effectiveness in protecting mechanical components, thereby accelerating wear and deterioration. Excessive friction, loss of oil viscosity, and accelerated oxidation are some of the direct problems that arise.
Contamination not only affects the lubricant itself but also compromises the integrity of vital components, such as pumps, valves, and actuators, thereby increasing the risk of catastrophic failures and unplanned downtime.
What Contamination Is Really Costing You
The economic impact of uncontrolled contamination goes beyond the cost of contaminated lubricants. The expenses related to equipment repairs, replacement of damaged parts, and the downtime required for maintenance far outweigh the investment that could be made in prevention.
Studies indicate that the cost to remove a gram of dirt can be as little as 10% of the potential damage that this contaminant causes when it enters the system.
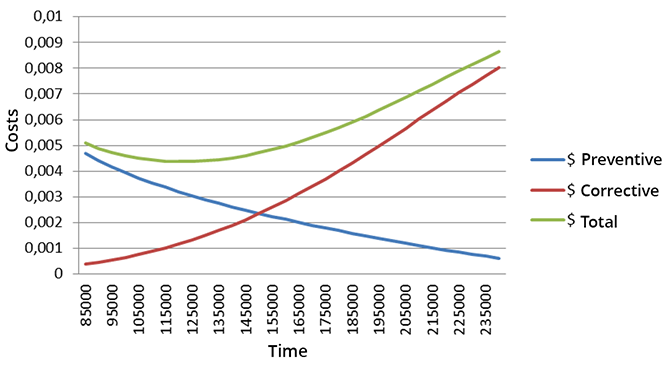
Maintenance Costs
Therefore, hidden costs accumulate in lost operational efficiency, premature component wear, and an increase in the frequency of corrective maintenance. The decision to invest in effective contamination control strategies is undoubtedly a crucial factor in reducing long-term operating expenses.
Top Entry Points for Lubricant Contamination
Contamination can occur at various stages of the operational process. Here are the main sources of contaminant entry:
- Inadequate vents and reservoir caps: Systems without effective vent filters allow dust and airborne particles to enter the lubricant.
- Worn seals: Equipment with damaged or poorly sized seals, when installed, is susceptible to the ingress of contaminants during operation.
- Harsh working environments: Industrial facilities with a high concentration of dust, moisture, or other pollutants in the air are more likely to introduce contaminants into hydraulic systems.
- 4. Poor handling and storage practices: Dirty containers, inappropriate storage locations, and unprotected transfer equipment can facilitate contaminants’ entry into lubricants.
Contamination Control: A Pillar of Proactive Maintenance
Adopting a rigorous fluid contamination control program is essential to protecting hydraulic systems and ensuring reliable operation. This approach should be seen as a central pillar of proactive maintenance, focusing on preventing failures rather than just reacting to problems.
Best Practices for Effective Contamination Control
To achieve a contaminant-free operation, some practices are indispensable:
- Regular monitoring of contamination levels: Perform periodic analysis of fluids to verify their health and the presence of solid particles, water, and other contaminants. Using technologies such as particle analysis and water counting can indicate oil quality and prevent problems before they occur.
- Filtration and contaminant removal: It is crucial to invest in efficient filtration systems that can remove fine particles and water from the lubricant. Dewatering, continuous filtration, or filtering in specific cycles can help keep fluids clean and ready for use at all times.
- Shielding systems and protecting vulnerable points: Ensure that vents, seals, sampling points, and connection points are protected from external contamination. This includes using three-dimensional sight glasses, BS&W cups, high-efficiency vent filters such as coalescing or desiccant vents, and protective covers in locations with high contaminant exposure.
- Adoption of real-time control and monitoring devices: Implement contamination sensors and monitoring devices to warn of variations in particle levels or the presence of water. This allows for a quick and effective response to prevent damage.
- Correct handling and storage practices: Lubricants should be stored in clean, covered, and dry places, using hermetically sealed drums and containers. During lubricant transfer, dedicated, clean, and suitable transfer and application equipment should be used to prevent cross-contamination and the introduction of these malfunctions into the system.
Thank you to Valciro Andrade Batista for this image.
Importance of Controlling Other Factors: Water, Temperature, and Oxidation
In addition to removing solid particles, it is crucial to control the presence of water, the system’s temperature, and the oil’s oxidation levels. Water, for example, can cause corrosion and emulsification of the oil, while excessive temperatures accelerate the degradation of additives and base oil. Controlling these factors helps maintain lubricating properties and extends the life of components.
Reducing water content, controlling temperature, and eliminating solid particles are practices that restore the lubricant to its essential properties, ensuring optimized asset performance and greater operational reliability.